Heat treatment and vacuum heat treatment are both processes used to alter the physical and mechanical properties of materials, particularly metals. However, they differ significantly in their methods, environments, and outcomes. Conventional heat treatment typically occurs in atmospheric air, which can lead to surface oxidation, decarburization, and contamination. In contrast, vacuum heat treatment takes place in a vacuum or low-pressure environment, eliminating these issues and providing a cleaner, more controlled process. This results in superior material properties, including a brighter and more purified surface, as well as improved performance and quality. Below, the key differences between these two methods are explained in detail.
Key Points Explained:
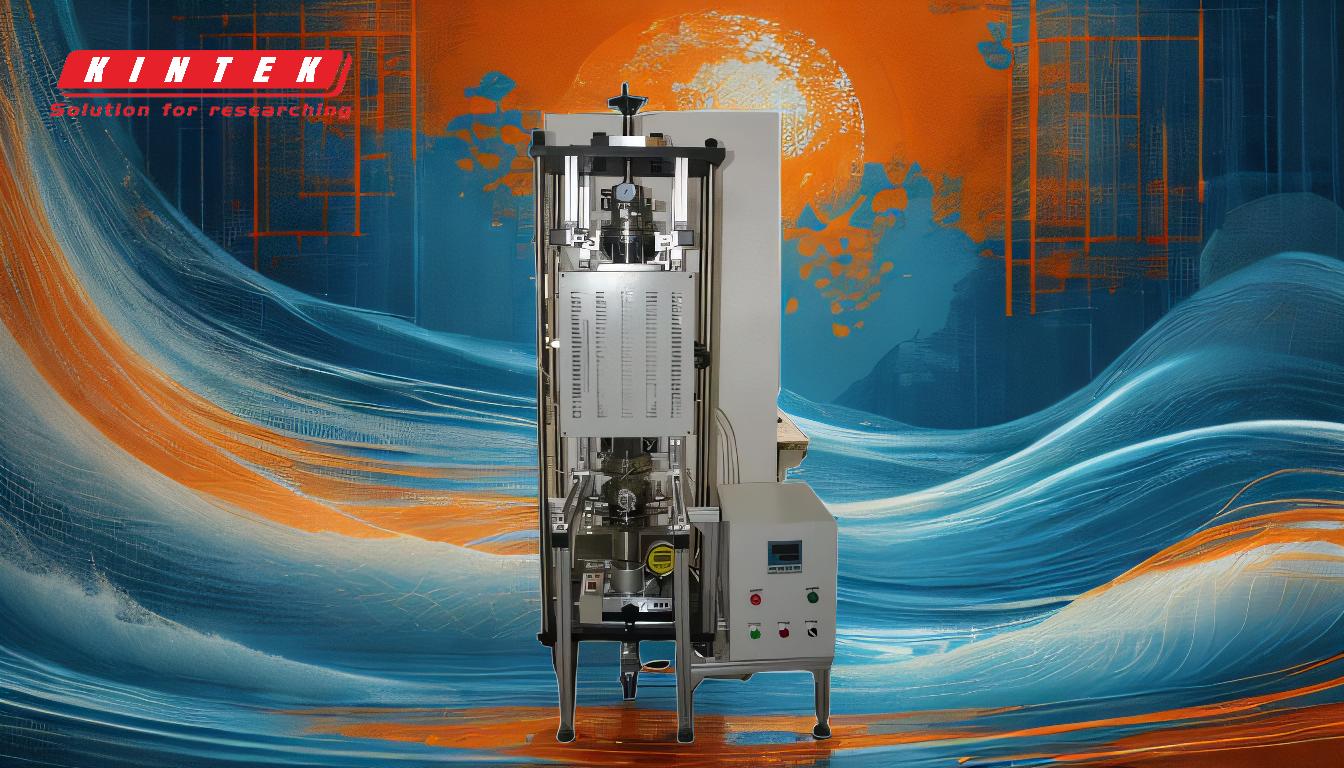
-
Environment and Atmosphere:
- Conventional Heat Treatment: This process occurs in atmospheric air, which contains oxygen, nitrogen, and other gases. These gases can react with the metal surface, leading to oxidation, decarburization, and other surface defects.
- Vacuum Heat Treatment: In this method, the air is removed from the heating chamber, creating a vacuum or low-pressure environment. This eliminates the presence of reactive gases, ensuring a contamination-free atmosphere. The absence of air prevents oxidation, decarburization, and carburization, leading to a clean and bright surface.
-
Surface Quality and Contamination:
- Conventional Heat Treatment: The presence of atmospheric gases can cause surface reactions, such as oxidation and decarburization, which degrade the surface quality. Contaminants like oils, greases, and oxides may also remain on the surface.
- Vacuum Heat Treatment: The vacuum environment removes contaminants and can even degas or convert oxides on the material's surface. This results in a purified surface with no oxidation, decarburization, or carburization. The process also removes phosphorus chips and has degreasing and degassing functions, further enhancing surface quality.
-
Process Control and Predictability:
- Conventional Heat Treatment: The process is less controlled due to the variable nature of atmospheric conditions. This can lead to inconsistent results and less predictable outcomes.
- Vacuum Heat Treatment: The process is highly controlled, with precise temperature regulation and cooling rates. The vacuum environment ensures uniformity and repeatability, leading to more predictable and superior results. Computer-controlled systems further enhance the precision and consistency of the process.
-
Temperature and Heating Methods:
- Conventional Heat Treatment: Heating is typically done using furnaces that operate in atmospheric conditions. The maximum temperature is limited by the oxidation and degradation of the material.
- Vacuum Heat Treatment: Heating is achieved using resistance or induction methods within a vacuum or protective gas environment. The process can reach very high temperatures (up to 2,400°F/1316°C) without causing oxidation or other surface reactions. This allows for more effective heat treatment of materials that require high temperatures.
-
Cooling Methods:
- Conventional Heat Treatment: Cooling is usually done in air, oil, or water, depending on the desired properties. However, the cooling rate can be less controlled, leading to potential inconsistencies.
- Vacuum Heat Treatment: Cooling is performed at controlled rates using different cooling media, such as gas or oil, within the vacuum environment. This controlled cooling ensures uniform microstructure changes and improved material properties.
-
Applications and Material Suitability:
- Conventional Heat Treatment: Suitable for a wide range of materials and applications where surface oxidation and minor inconsistencies are acceptable. Commonly used in industries like automotive, construction, and general manufacturing.
- Vacuum Heat Treatment: Ideal for high-precision applications and materials that require superior surface quality and mechanical properties. Commonly used in aerospace, medical devices, and high-performance tooling industries.
-
Cost and Complexity:
- Conventional Heat Treatment: Generally less expensive and simpler to implement due to the use of standard furnaces and atmospheric conditions.
- Vacuum Heat Treatment: More expensive and complex due to the need for specialized vacuum furnaces, pumping systems, and precise control mechanisms. However, the benefits in terms of material quality and performance often justify the higher cost.
In summary, while both heat treatment and vacuum heat treatment aim to improve the properties of materials, the key differences lie in the environment, surface quality, process control, and applications. Vacuum heat treatment offers significant advantages in terms of cleanliness, surface purity, and predictability, making it the preferred choice for high-precision and high-performance applications.
Summary Table:
Aspect | Conventional Heat Treatment | Vacuum Heat Treatment |
---|---|---|
Environment | Atmospheric air (contains oxygen, nitrogen, etc.) | Vacuum or low-pressure environment |
Surface Quality | Oxidation, decarburization, contamination | Clean, bright, purified surface |
Process Control | Less controlled, variable outcomes | Highly controlled, predictable results |
Temperature Range | Limited by oxidation risks | High temperatures (up to 2,400°F/1316°C) achievable |
Cooling Methods | Air, oil, or water (less controlled) | Controlled cooling with gas or oil |
Applications | Automotive, construction, general manufacturing | Aerospace, medical devices, high-performance tooling |
Cost | Less expensive, simpler setup | More expensive, complex equipment required |
Need help choosing the right heat treatment method for your materials? Contact our experts today!