Plasma nitriding and traditional nitriding (such as gas or bath nitriding) are surface hardening techniques used to improve the wear resistance, fatigue strength, and corrosion resistance of metal components. The key difference lies in the process mechanism and the resulting benefits. Plasma nitriding uses ionized gas (plasma) to introduce nitrogen into the surface of the material, while traditional nitriding relies on gas or liquid mediums. Plasma nitriding offers advantages such as lower process temperatures, reduced distortion, shorter treatment times, and better environmental compatibility. It also eliminates the need for special preparation steps, making it suitable for a wider range of materials, including stainless steels.
Key Points Explained:
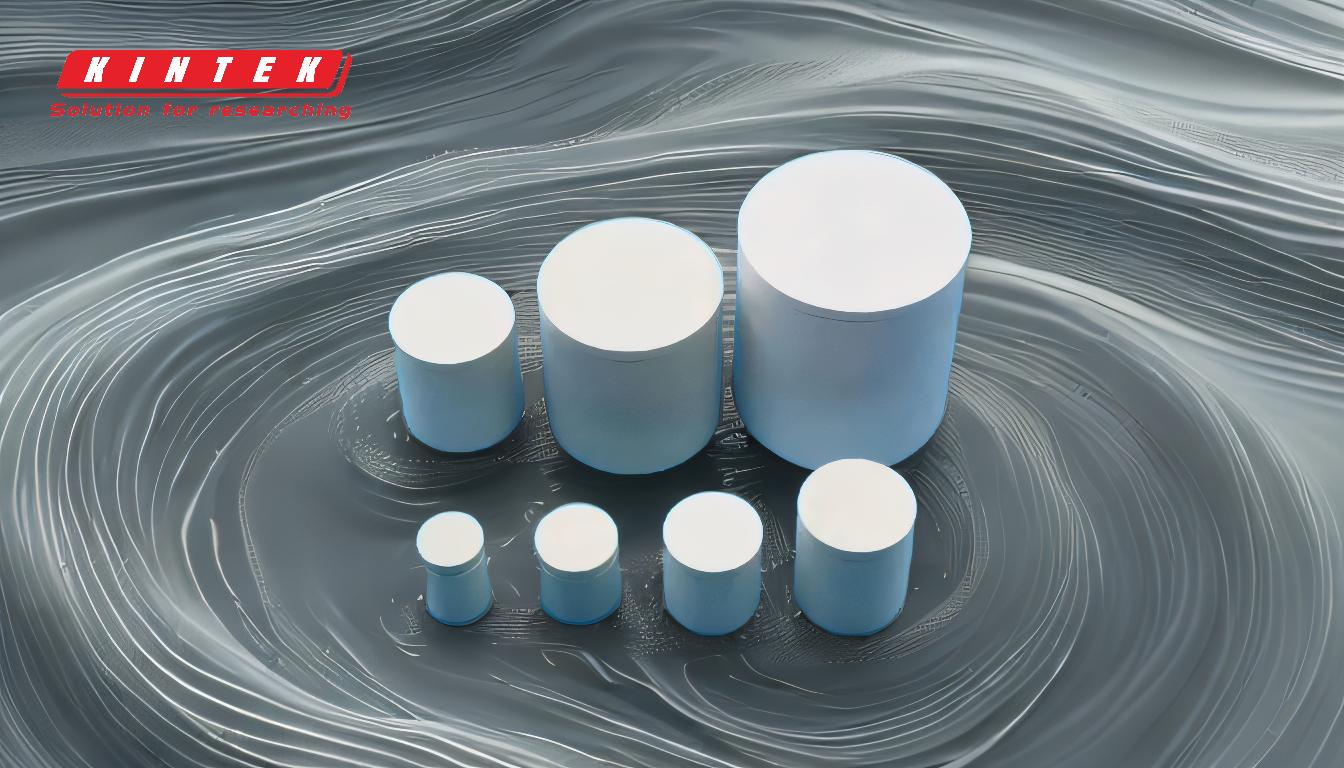
-
Mechanism of Plasma Nitriding vs. Traditional Nitriding:
- Plasma nitriding involves ionizing nitrogen gas to create a plasma, which bombards the surface of the workpiece, allowing nitrogen to diffuse into the material. This process is highly controllable and can be adjusted for specific material requirements.
- Traditional nitriding, such as gas nitriding, uses ammonia gas (NH₃) that decomposes at high temperatures to release nitrogen, which then diffuses into the material. Bath nitriding, on the other hand, involves immersing the workpiece in a molten salt bath containing nitrogen-rich compounds.
-
Material Compatibility:
- Plasma nitriding is versatile and can be applied to all ferrous alloys, including stainless steels, without requiring special preparation or activation steps. This is a significant advantage over traditional nitriding, which often requires additional surface treatments for certain materials.
- Traditional nitriding may not be suitable for some stainless steels due to the formation of a passive oxide layer that hinders nitrogen diffusion.
-
Process Temperature and Distortion:
- Plasma nitriding operates at lower temperatures compared to traditional nitriding methods. This reduces the risk of thermal distortion, making it ideal for precision components.
- Lower temperatures also minimize the need for rework, as the dimensional stability of the workpiece is better preserved.
-
Treatment Time and Efficiency:
- Plasma nitriding typically has shorter treatment times due to the efficient nitrogen diffusion enabled by the plasma environment.
- Traditional nitriding processes, especially gas nitriding, may require longer treatment times to achieve similar results.
-
Environmental and Energy Considerations:
- Plasma nitriding is more environmentally friendly, as it does not involve the use of hazardous chemicals or produce harmful byproducts. It is also more energy-efficient due to lower operating temperatures and shorter cycle times.
- Traditional nitriding methods, particularly bath nitriding, involve the use of molten salts, which can pose environmental and safety concerns.
-
Surface Quality and Reproducibility:
- The layers produced by plasma nitriding are less brittle and porous, resulting in improved surface properties and better wear resistance.
- Plasma nitriding offers higher reproducibility, as the process parameters can be precisely controlled to achieve consistent results.
-
Masking and Selective Treatment:
- Plasma nitriding allows for easy masking of specific areas using mechanical methods, such as covering threaded holes or other regions that need to remain soft after treatment. This is more challenging in traditional nitriding processes.
In summary, plasma nitriding provides a more advanced and efficient alternative to traditional nitriding methods, offering benefits such as lower process temperatures, reduced distortion, shorter treatment times, and better environmental compatibility. Its ability to treat a wider range of materials without special preparation makes it a preferred choice for many industrial applications.
Summary Table:
Aspect | Plasma Nitriding | Traditional Nitriding |
---|---|---|
Mechanism | Uses ionized gas (plasma) to diffuse nitrogen into the material. | Relies on gas (e.g., ammonia) or liquid (e.g., molten salt) mediums. |
Material Compatibility | Suitable for all ferrous alloys, including stainless steels, without preparation. | May require special preparation for certain materials, e.g., stainless steels. |
Process Temperature | Lower temperatures, reducing distortion and thermal stress. | Higher temperatures, increasing the risk of distortion. |
Treatment Time | Shorter treatment times due to efficient nitrogen diffusion. | Longer treatment times to achieve similar results. |
Environmental Impact | Environmentally friendly, no hazardous chemicals or byproducts. | May involve hazardous chemicals (e.g., molten salts) and environmental concerns. |
Surface Quality | Produces less brittle and porous layers, improving wear resistance. | Layers may be more brittle or porous, depending on the process. |
Reproducibility | High reproducibility with precise control over process parameters. | Less consistent results due to variability in process conditions. |
Selective Treatment | Easy masking for selective treatment of specific areas. | Challenging to mask specific areas effectively. |
Ready to enhance your metal components with advanced plasma nitriding? Contact us today to learn more!