Quenching and heat treatment are both processes used to alter the physical and mechanical properties of metals, but they differ in scope and purpose. Heat treatment is a broad term encompassing various processes that involve heating and cooling metals to achieve desired properties such as hardness, strength, or ductility. Quenching, on the other hand, is a specific type of heat treatment that focuses on rapid cooling, typically using water or oil, to lock the metal's structure into a hardened state. While quenching is a subset of heat treatment, the two are not interchangeable, as heat treatment includes other methods like annealing, tempering, and normalizing.
Key Points Explained:
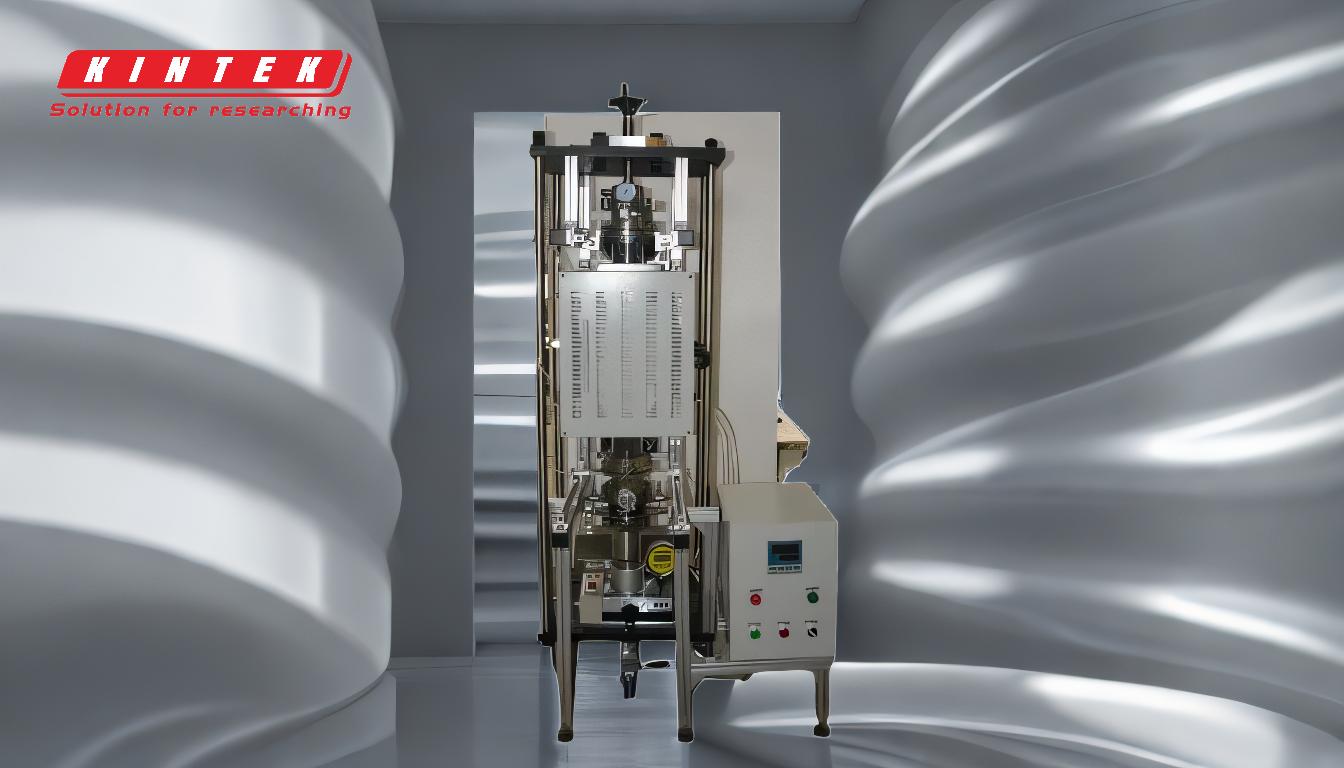
-
Definition and Scope:
- Heat Treatment: A general term for processes that involve heating and cooling metals to alter their physical and mechanical properties. It includes methods like annealing, tempering, normalizing, and quenching.
- Quenching: A specific heat treatment process that involves rapid cooling of a metal, usually by immersing it in water, oil, or other cooling mediums. Its primary goal is to achieve high hardness and strength by locking the metal's structure in a solidified state.
-
Purpose and Outcomes:
- Heat Treatment: Aims to achieve a wide range of properties, such as increased hardness, improved ductility, enhanced toughness, or stress relief. The specific outcome depends on the method used (e.g., annealing softens the metal, while tempering reduces brittleness).
- Quenching: Primarily focuses on increasing hardness and strength by rapidly cooling the metal from a high temperature. This process often results in a brittle material, which may require subsequent tempering to reduce brittleness and improve toughness.
-
Process Details:
- Heat Treatment: Involves heating the metal to a specific temperature, holding it at that temperature for a set period, and then cooling it at a controlled rate. The cooling rate can vary depending on the desired properties.
- Quenching: Involves heating the metal to a temperature above its transformation range and then rapidly cooling it, often using water, oil, or air. The rapid cooling rate is critical to achieving the desired hardened structure.
-
Types and Variations:
- Heat Treatment: Includes multiple methods, such as annealing, tempering, normalizing, and quenching. Each method has specific heating and cooling protocols tailored to achieve different material properties.
- Quenching: Has several variations, including direct quenching, fog quenching, hot quenching, interrupted quenching, selective quenching, slack quenching, spray quenching, and time quenching. Each type is suited for specific applications and materials.
-
Applications:
- Heat Treatment: Used across various industries to improve the performance of metals in applications ranging from automotive components to aerospace parts. The choice of heat treatment method depends on the material and the desired properties.
- Quenching: Commonly used for hardening medium carbon alloy steels, tool steels, and other materials that require high surface hardness and wear resistance. It is often followed by tempering to balance hardness with toughness.
-
Material Considerations:
- Heat Treatment: Applicable to a wide range of metals and alloys, including steel, aluminum, copper, and titanium. The specific heat treatment process is chosen based on the material's composition and intended use.
- Quenching: Best suited for metals that can undergo a martensitic transformation, such as certain steels. Not all metals are suitable for quenching, as rapid cooling can cause cracking or distortion in some materials.
In summary, while quenching is a specific type of heat treatment focused on rapid cooling to achieve hardness, heat treatment is a broader category that includes various processes designed to alter a metal's properties. Understanding the differences between these processes is crucial for selecting the appropriate method to achieve the desired material characteristics.
Summary Table:
Aspect | Heat Treatment | Quenching |
---|---|---|
Definition | Broad term for processes involving heating and cooling metals to alter properties. | Specific heat treatment process involving rapid cooling to achieve hardness. |
Purpose | Achieves various properties like hardness, ductility, toughness, or stress relief. | Primarily increases hardness and strength through rapid cooling. |
Process | Heating, holding, and controlled cooling. | Heating followed by rapid cooling (water, oil, or air). |
Types/Variations | Includes annealing, tempering, normalizing, and quenching. | Variations include direct, fog, hot, interrupted, and selective quenching. |
Applications | Used in automotive, aerospace, and more for improved metal performance. | Commonly used for hardening medium carbon alloy steels and tool steels. |
Material Suitability | Applicable to a wide range of metals and alloys. | Best suited for metals that undergo martensitic transformation (e.g., steels). |
Need help choosing the right heat treatment or quenching process for your materials? Contact our experts today!