Solid-state sintering and liquid-phase sintering are two distinct methods used in the densification of powdered materials, each with unique mechanisms and applications. Solid-state sintering relies on atomic diffusion to bond particles without melting, making it suitable for ceramics like zirconia and alumina. Liquid-phase sintering, on the other hand, involves the addition of a low-melting-point material that forms a liquid phase at sintering temperatures, facilitating particle rearrangement and bonding. This method is particularly useful for harder-to-densify ceramics like silicon nitride and silicon carbide. The choice between these methods depends on material properties, desired densification rates, and sintering temperatures.
Key Points Explained:
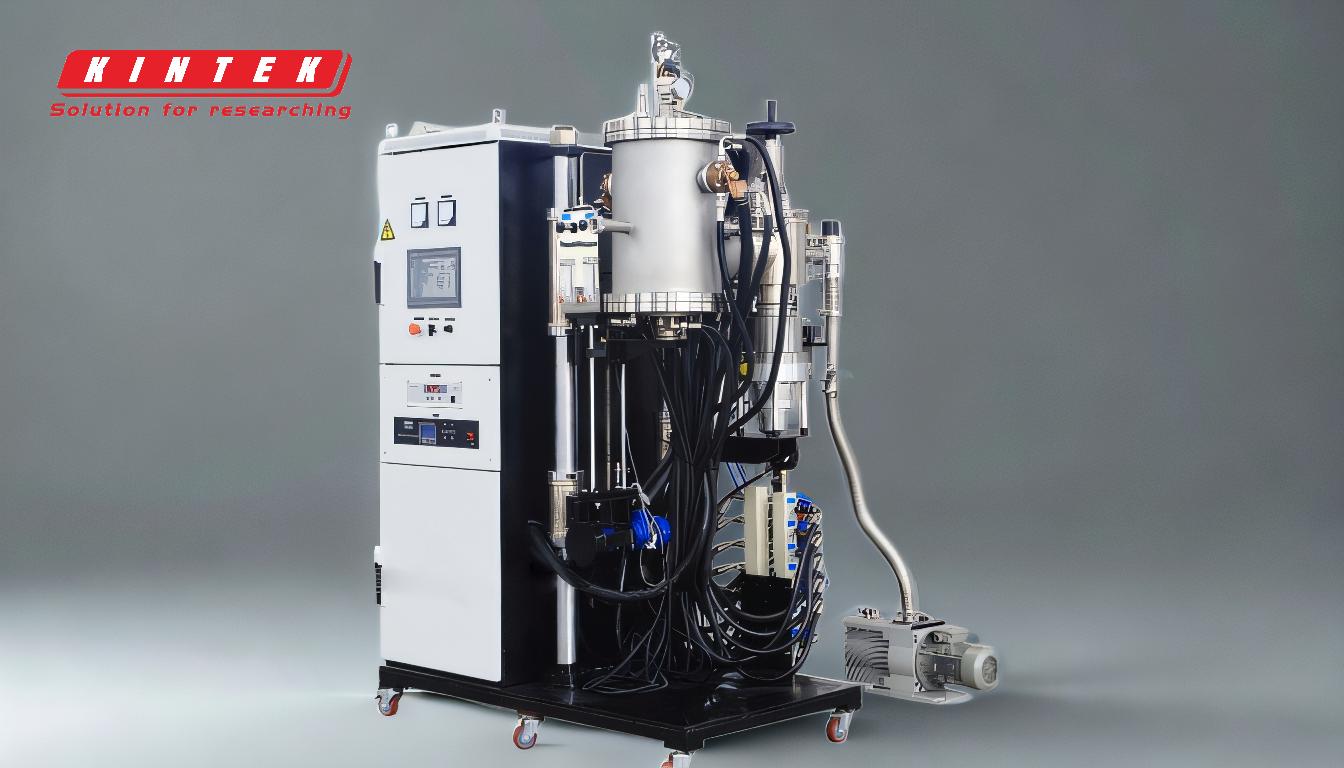
-
Mechanism of Bonding:
- Solid-State Sintering: In this process, powdered materials are heated to a temperature just below their melting point. Bonding occurs through atomic diffusion, where atoms move across particle boundaries, leading to densification and strength. This method does not involve any liquid phase.
- Liquid-Phase Sintering: Here, a small amount of a low-melting-point additive is introduced. At sintering temperatures, this additive forms a liquid phase. The liquid aids in particle rearrangement due to capillary forces, enhancing densification and bonding.
-
Temperature Requirements:
- Solid-State Sintering: Typically requires higher temperatures since it relies solely on atomic diffusion. The absence of a liquid phase means that the material must be heated close to its melting point to achieve sufficient atomic mobility.
- Liquid-Phase Sintering: Generally operates at lower temperatures compared to solid-state sintering. The presence of a liquid phase reduces the energy needed for particle rearrangement and bonding, making it more energy-efficient.
-
Material Suitability:
- Solid-State Sintering: Best suited for materials that can achieve densification through diffusion alone, such as zirconia and alumina. These materials have relatively lower melting points and can be effectively densified without the need for a liquid phase.
- Liquid-Phase Sintering: Ideal for harder-to-densify materials like silicon nitride and silicon carbide. These materials have high melting points and require additional mechanisms, such as the presence of a liquid phase, to achieve effective densification.
-
Densification Rate:
- Solid-State Sintering: The densification rate is generally slower due to the reliance on atomic diffusion, which is a slower process compared to liquid-phase mechanisms.
- Liquid-Phase Sintering: Offers a faster densification rate due to the enhanced mobility of particles in the presence of a liquid phase. This makes it particularly useful when rapid densification is desired.
-
Applications:
- Solid-State Sintering: Commonly used in the production of ceramic components where high purity and structural integrity are critical. Examples include medical implants, cutting tools, and electronic substrates.
- Liquid-Phase Sintering: Often employed in the manufacturing of advanced ceramics and composites that require high strength and toughness. Applications include aerospace components, cutting tools, and wear-resistant parts.
-
Advantages and Limitations:
-
Solid-State Sintering:
- Advantages: Produces high-purity materials with minimal contamination. Suitable for materials that do not require rapid densification.
- Limitations: Slower process and requires higher temperatures, which can be energy-intensive.
-
Liquid-Phase Sintering:
- Advantages: Faster densification, lower sintering temperatures, and effective for high-melting-point materials.
- Limitations: Potential for contamination from the liquid phase and may require post-sintering treatments to remove residual liquid.
-
Solid-State Sintering:
In summary, the choice between solid-state sintering and liquid-phase sintering depends on the specific material properties and the desired outcomes of the sintering process. Solid-state sintering is ideal for materials that can be densified through diffusion alone, while liquid-phase sintering is better suited for harder-to-densify materials that benefit from the presence of a liquid phase. Understanding these differences is crucial for selecting the appropriate sintering method for a given application.
Summary Table:
Aspect | Solid-State Sintering | Liquid-Phase Sintering |
---|---|---|
Mechanism | Atomic diffusion without melting | Liquid phase aids particle rearrangement and bonding |
Temperature | Higher temperatures (close to melting point) | Lower temperatures due to liquid phase |
Material Suitability | Zirconia, alumina (lower melting points) | Silicon nitride, silicon carbide (high melting points) |
Densification Rate | Slower (relies on atomic diffusion) | Faster (enhanced by liquid phase) |
Applications | Medical implants, cutting tools, electronic substrates | Aerospace components, wear-resistant parts, cutting tools |
Advantages | High purity, minimal contamination | Faster densification, lower temperatures, effective for high-melting-point materials |
Limitations | Slower process, energy-intensive | Potential contamination, post-sintering treatments may be required |
Need help choosing the right sintering method for your materials? Contact our experts today for tailored solutions!