Calcination temperature significantly influences the properties of nanoparticles, including their size, morphology, crystallinity, and surface characteristics. Higher calcination temperatures generally lead to increased crystallinity and reduced surface area due to particle agglomeration and sintering. However, excessive temperatures can cause undesirable phase transformations or degradation. Optimal calcination temperatures are crucial for achieving desired properties, such as enhanced catalytic activity or improved mechanical strength, depending on the application. Understanding the relationship between calcination temperature and nanoparticle properties is essential for tailoring materials for specific uses.
Key Points Explained:
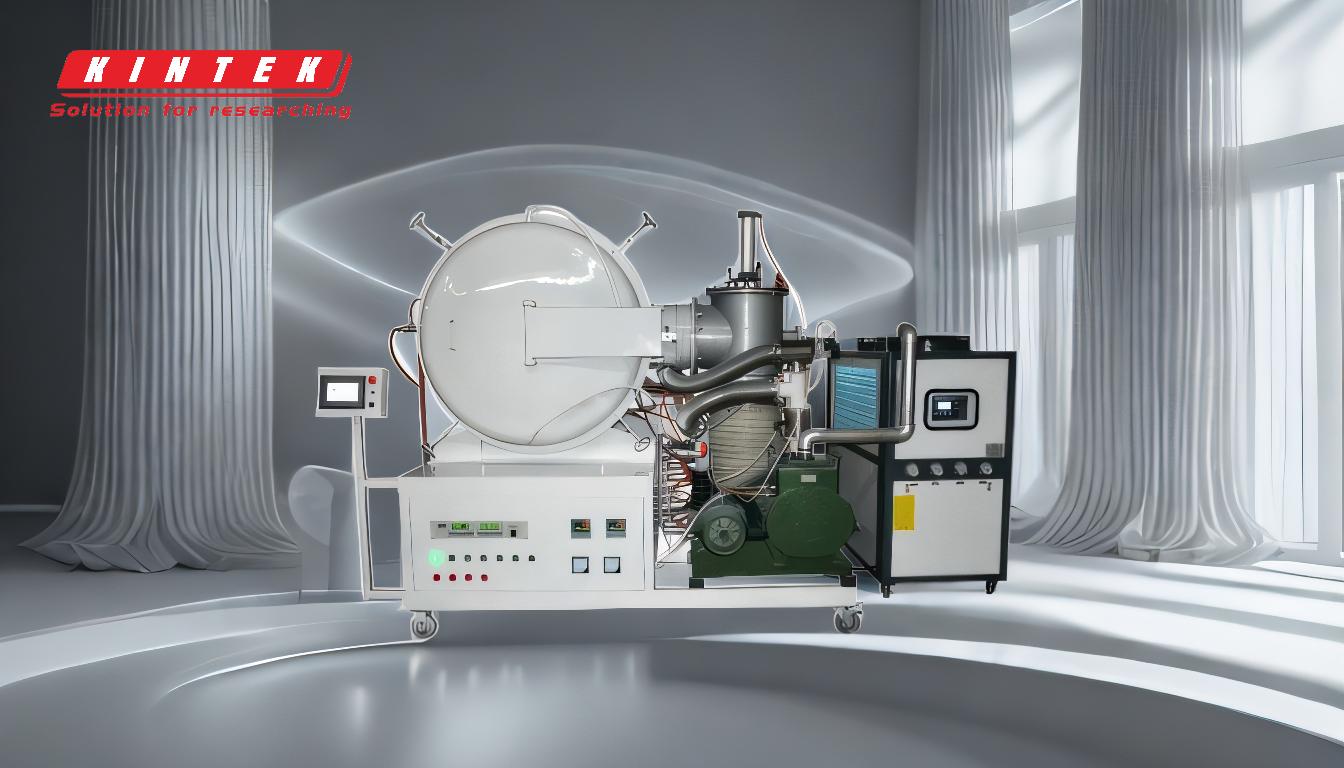
-
Effect on Particle Size and Agglomeration:
- Higher calcination temperatures often result in larger particle sizes due to increased agglomeration and sintering.
- As temperature rises, nanoparticles tend to fuse together, reducing surface area and increasing particle size.
- This can be detrimental for applications requiring high surface area, such as catalysis or adsorption.
-
Impact on Crystallinity:
- Calcination promotes crystallization by providing the energy needed for atoms to rearrange into ordered structures.
- Higher temperatures enhance crystallinity, leading to more defined crystal structures and improved mechanical properties.
- However, excessive temperatures can cause phase transformations or degradation, altering the material's intended properties.
-
Surface Area and Porosity:
- Surface area typically decreases with increasing calcination temperature due to particle densification and pore collapse.
- Lower surface areas may reduce reactivity in catalytic applications but can improve stability in high-temperature environments.
- Optimizing calcination temperature is essential to balance surface area and structural integrity.
-
Phase Stability and Transformation:
- Calcination temperature can induce phase transformations, such as converting amorphous materials to crystalline phases or altering crystal structures.
- For example, in metal oxides, higher temperatures may lead to the formation of stable phases like rutile from anatase in TiO₂.
- Understanding these transformations is critical for applications requiring specific phase properties.
-
Thermal and Mechanical Properties:
- Higher calcination temperatures generally improve thermal stability and mechanical strength due to enhanced crystallinity and reduced defects.
- However, excessive temperatures can lead to brittleness or cracking, compromising mechanical performance.
- Tailoring calcination conditions is vital for achieving the desired balance between strength and flexibility.
-
Application-Specific Considerations:
- Catalysis: Lower calcination temperatures are often preferred to maintain high surface area and reactivity.
- Structural Materials: Higher temperatures may be necessary to achieve sufficient mechanical strength and thermal stability.
- Optical and Electronic Applications: Precise control of calcination temperature is required to optimize properties like bandgap and conductivity.
-
Experimental Optimization:
- Researchers often use techniques like thermogravimetric analysis (TGA) and X-ray diffraction (XRD) to determine the optimal calcination temperature for a specific material.
- Systematic studies are conducted to evaluate the effects of temperature on properties like crystallinity, surface area, and phase composition.
In summary, calcination temperature is a critical parameter in nanoparticle synthesis, influencing size, crystallinity, surface area, and phase stability. By carefully controlling this variable, researchers can tailor nanoparticles for specific applications, balancing properties like reactivity, strength, and thermal stability.
Summary Table:
Property | Effect of Higher Calcination Temperature | Application Implications |
---|---|---|
Particle Size | Increases due to agglomeration and sintering. | Detrimental for high surface area needs like catalysis. |
Crystallinity | Enhances crystallinity, improving mechanical properties. | Beneficial for structural materials but may cause phase degradation if excessive. |
Surface Area & Porosity | Decreases due to densification and pore collapse. | Reduces reactivity but improves stability in high-temperature environments. |
Phase Stability | Induces phase transformations (e.g., amorphous to crystalline). | Critical for applications requiring specific phase properties. |
Thermal & Mechanical | Improves thermal stability and strength but may cause brittleness at excessive temperatures. | Tailor conditions to balance strength and flexibility. |
Application-Specific | Varies: lower temps for catalysis, higher for structural materials, precise control for optical/electronic. | Optimize for reactivity, strength, or conductivity based on application needs. |
Need help optimizing calcination temperatures for your nanoparticle synthesis? Contact our experts today!