Heat treatment significantly influences the grain structure of metallic alloys, which in turn affects their mechanical properties such as hardness, strength, toughness, ductility, and elasticity. By controlling the rate of diffusion and cooling, heat treatment can refine or coarsen the grain structure, leading to changes in the material's performance. For instance, processes like annealing can soften the material by creating a more uniform and larger grain structure, while quenching can harden the material by creating a finer grain structure. However, there is often a trade-off between strength and toughness, as increasing hardness may reduce toughness and introduce brittleness. Tempering or drawing back can mitigate brittleness, making the material more ductile and usable. The specific effects of heat treatment on grain structure depend on the process used and the desired mechanical properties.
Key Points Explained:
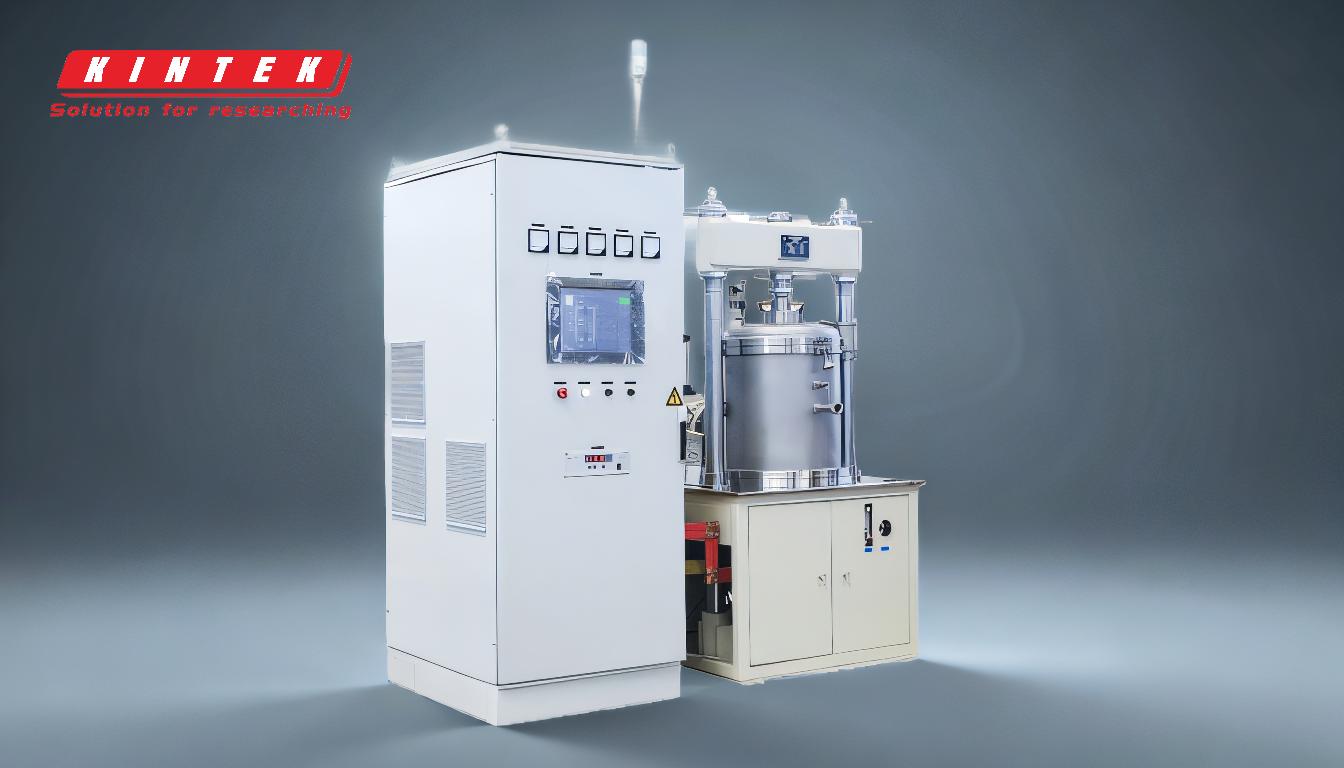
-
Effect of Heat Treatment on Grain Structure:
- Heat treatment alters the grain structure of metallic alloys by controlling the rate of diffusion and cooling.
- Processes like annealing lead to a more uniform and larger grain structure, which softens the material.
- Quenching results in a finer grain structure, increasing hardness but potentially reducing toughness.
-
Trade-off Between Strength and Toughness:
- Increasing strength (measured by hardness) often reduces toughness, making the material more brittle.
- Heat treatment processes such as case hardening or through hardening increase strength but may require tempering to reduce brittleness.
- Tempering or drawing back is used to achieve a balance between strength and toughness, making the material more ductile.
-
Impact on Mechanical Properties:
- Heat treatment can significantly affect yield strength, tensile strength, and fracture toughness.
- The ultimate strength desired in the material determines the amount of tempering required.
- If a material is too brittle as received, it can be heat treated (annealed or re-tempered) to improve its ductility and usability.
-
Specific Heat Treatment Processes:
- Annealing: Softens the material by creating a more uniform and larger grain structure, improving ductility and reducing internal stresses.
- Quenching: Increases hardness by creating a finer grain structure, but may introduce brittleness.
- Tempering: Reduces brittleness and increases toughness by allowing some of the hardness to be sacrificed, making the material more ductile.
-
Practical Considerations for Equipment and Consumable Purchasers:
- Understanding the specific heat treatment processes and their effects on grain structure is crucial for selecting the right material for a given application.
- The trade-off between strength and toughness must be carefully considered, especially for applications requiring high durability and resistance to fracture.
- Heat treatment can be used to modify the properties of materials that are initially too brittle, making them more suitable for practical use.
By carefully selecting and applying the appropriate heat treatment processes, the grain structure of metallic alloys can be optimized to achieve the desired mechanical properties, ensuring the material performs well in its intended application.
Summary Table:
Heat Treatment Process | Effect on Grain Structure | Impact on Mechanical Properties |
---|---|---|
Annealing | Larger, more uniform grains | Softens material, improves ductility |
Quenching | Finer grains | Increases hardness, may reduce toughness |
Tempering | Balances grain structure | Reduces brittleness, increases toughness |
Discover how heat treatment can enhance your material's performance—contact our experts today!