The heating rate during sintering significantly impacts the final material properties, including densification, uniformity, and crystallinity. A high heating rate can lead to insufficient sintering inside the material, causing uneven densification and high-temperature melting peaks. Conversely, controlled heating rates, such as those achieved in Spark Plasma Sintering (SPS) or microwave heating, can enhance densification and reduce sintering time. Factors like temperature, particle size, and material composition also interact with the heating rate to influence sintering behavior. Balancing these factors is crucial to achieving optimal material properties.
Key Points Explained:
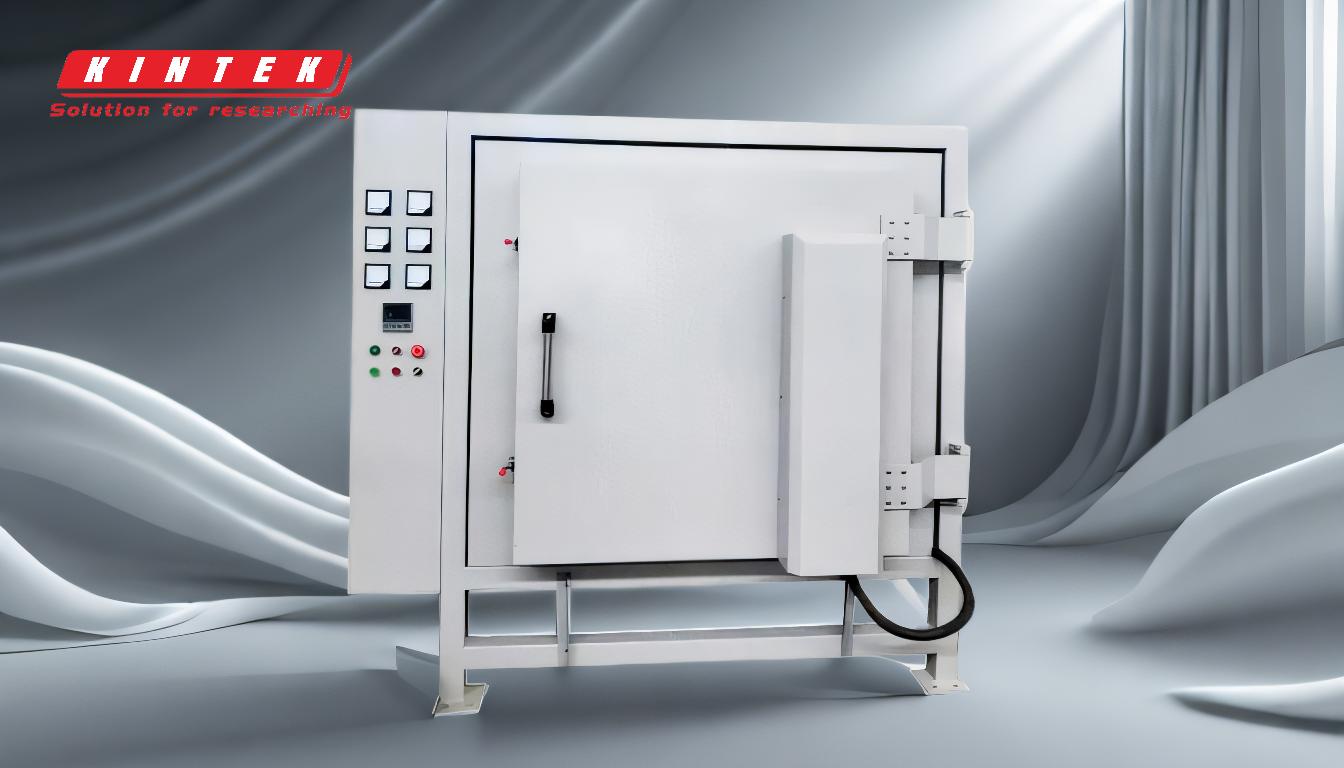
-
Effect of High Heating Rates:
- Insufficient Sintering: High heating rates can lead to insufficient sintering inside the material, particularly in thicker or denser regions. This occurs because the outer layers may sinter quickly while the inner regions remain under-sintered.
- Uneven Densification: Rapid heating can cause significant differences in sintering degree across different areas of the material, leading to non-uniform densification and potential structural weaknesses.
- High-Temperature Melting Peaks: Excessive heating rates can result in localized high-temperature melting peaks, which may lead to undesirable crystallinity and material defects.
-
Advantages of Controlled Heating Rates:
- Uniform Heating: Techniques like microwave heating offer rapid and uniform heating, which can shorten sintering time and improve material uniformity.
- Enhanced Densification: Controlled heating rates allow for better particle rearrangement and porosity elimination, leading to higher densification and improved material properties.
-
Comparison of Heating Rates in Different Sintering Methods:
- Conventional Sintering: Typically achieves heating rates of 5 to 10°C/min, requiring longer sintering times (2 to 4 hours or more) to reach high temperatures.
- Spark Plasma Sintering (SPS): Achieves much higher heating rates (exceeding 300°C/min), allowing rapid temperature increases (e.g., reaching 1200°C in just 4 minutes). This reduces sintering time and can enhance material properties.
-
Interaction with Other Sintering Factors:
- Temperature: Temperature control is critical as it directly affects grain boundary and bulk diffusion, which are essential for densification.
- Particle Size and Composition: Smaller particles and homogeneous compositions promote better densification, but their effectiveness can be influenced by the heating rate.
- Pressure: Applied pressure enhances particle rearrangement and porosity elimination, complementing the effects of controlled heating rates.
-
Practical Implications for Material Design:
- Optimizing Heating Rates: For materials requiring high uniformity and density, moderate heating rates are often preferable to avoid defects associated with rapid heating.
- Tailoring Sintering Methods: Selecting the appropriate sintering method (e.g., SPS for rapid sintering or conventional methods for slower, controlled processes) can help achieve desired material properties.
- Balancing Factors: Achieving optimal sintering outcomes requires balancing heating rates with other factors like temperature, pressure, and material composition.
In summary, the heating rate is a critical parameter in sintering, influencing densification, uniformity, and material properties. While high heating rates can lead to defects, controlled rates can enhance sintering efficiency and material quality. Understanding the interplay between heating rates and other sintering factors is essential for optimizing material design and performance.
Summary Table:
Aspect | High Heating Rates | Controlled Heating Rates |
---|---|---|
Sintering Quality | Insufficient sintering, uneven densification, high-temperature melting peaks | Uniform heating, enhanced densification, reduced sintering time |
Heating Rate Range | Rapid heating (e.g., >300°C/min in SPS) | Moderate heating (e.g., 5–10°C/min in conventional sintering) |
Impact on Material | Potential defects, non-uniformity, and structural weaknesses | Improved material properties, higher density, and uniformity |
Sintering Methods | Spark Plasma Sintering (SPS), microwave heating | Conventional sintering, tailored methods for specific material needs |
Key Factors | Temperature, particle size, material composition, pressure | Temperature, particle size, material composition, pressure |
Optimize your sintering process for superior material properties—contact our experts today!