Increasing the pressure during sintering has several significant effects on the material being processed. Primarily, it enhances the densification process by providing an additional driving force for particle fusion, which is particularly beneficial for materials that are difficult to sinter. This results in reduced porosity and improved mechanical properties such as strength, hardness, and wear resistance. Additionally, applying pressure can decrease the sintering time, making the process more efficient. The microstructure of the material, including grain size and grain boundary distribution, is also positively influenced, leading to better overall material performance.
Key Points Explained:
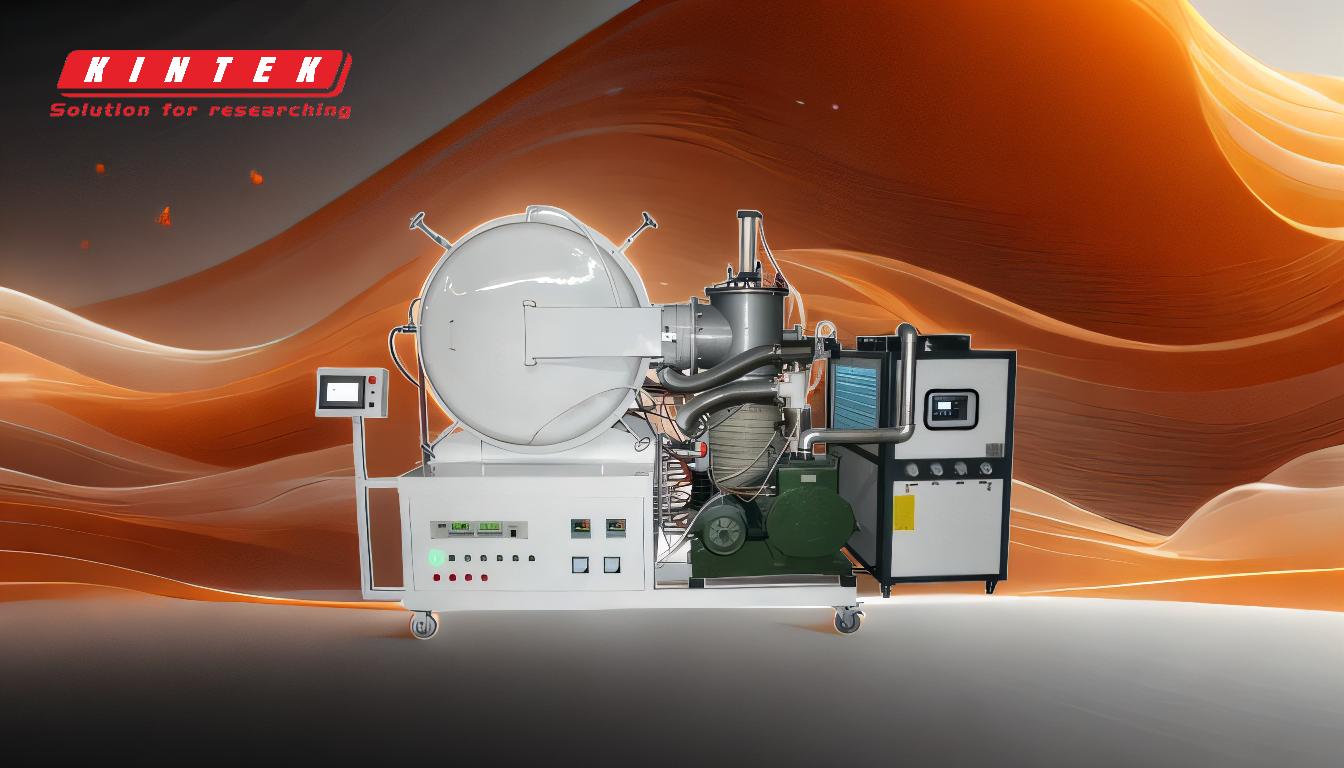
-
Enhanced Densification:
- Driving Force for Fusion: Applying pressure during sintering introduces an additional driving force that helps particles fuse together more effectively. This is especially useful for materials that are otherwise challenging to sinter.
- Reduced Porosity: The increased pressure helps to minimize the porosity of the sintered material, leading to a denser and more cohesive structure.
-
Improved Mechanical Properties:
- Strength and Hardness: The densification process results in materials with superior mechanical properties. The bonds between particles become stronger, enhancing the overall strength and hardness of the material.
- Wear Resistance: A denser structure with fewer pores also improves the wear resistance of the material, making it more durable under mechanical stress.
-
Reduced Sintering Time:
- Efficiency: Applying pressure can significantly reduce the time required for sintering. This makes the process more efficient and can lead to cost savings in industrial applications.
- Consistency: Shorter sintering times can also contribute to more consistent material properties, as the risk of over-sintering or uneven sintering is reduced.
-
Microstructural Benefits:
- Grain Size and Distribution: Pressure during sintering affects the grain size and the distribution of grain boundaries in the material. This can lead to a more uniform microstructure, which is beneficial for the material's mechanical properties.
- Grain Boundary Shape: The shape and distribution of grain boundaries are also influenced, which can further enhance the material's strength and durability.
-
Application in Hot Pressing:
- Technique: Hot pressing is a specific sintering technique where pressure and heat are applied simultaneously. This method is particularly effective for materials that are difficult to sinter using conventional methods.
- Material Suitability: Hot pressing is suitable for a wide range of materials, including ceramics and metals, and can produce components with exceptional mechanical properties.
In summary, increasing the pressure during sintering offers multiple benefits, including enhanced densification, improved mechanical properties, reduced sintering time, and favorable microstructural changes. These effects make pressure-assisted sintering a valuable technique in the production of high-performance materials.
Summary Table:
Effect | Description |
---|---|
Enhanced Densification | Pressure improves particle fusion, reducing porosity and creating denser materials. |
Improved Mechanical Properties | Increases strength, hardness, and wear resistance due to stronger particle bonds. |
Reduced Sintering Time | Shortens sintering time, improving efficiency and consistency in material properties. |
Microstructural Benefits | Optimizes grain size, distribution, and boundary shape for better performance. |
Hot Pressing Application | Combines heat and pressure for challenging materials, producing high-performance components. |
Unlock the potential of pressure-assisted sintering for your materials—contact us today to learn more!