The effect of the substrate on thin films is profound and multifaceted, influencing the film's adhesion, microstructure, optical properties, and overall performance. The substrate's properties, such as temperature, surface energy, and composition, play a critical role in determining the quality and functionality of the thin film. Factors like deposition techniques, film thickness, and substrate temperature further modulate these effects. For instance, heating the substrate can enhance adhesion and uniformity, while the substrate's nature and residual gas composition in the deposition environment can alter the film's structural and optical properties. Understanding these interactions is essential for optimizing thin film manufacturing to meet specific performance criteria.
Key Points Explained:
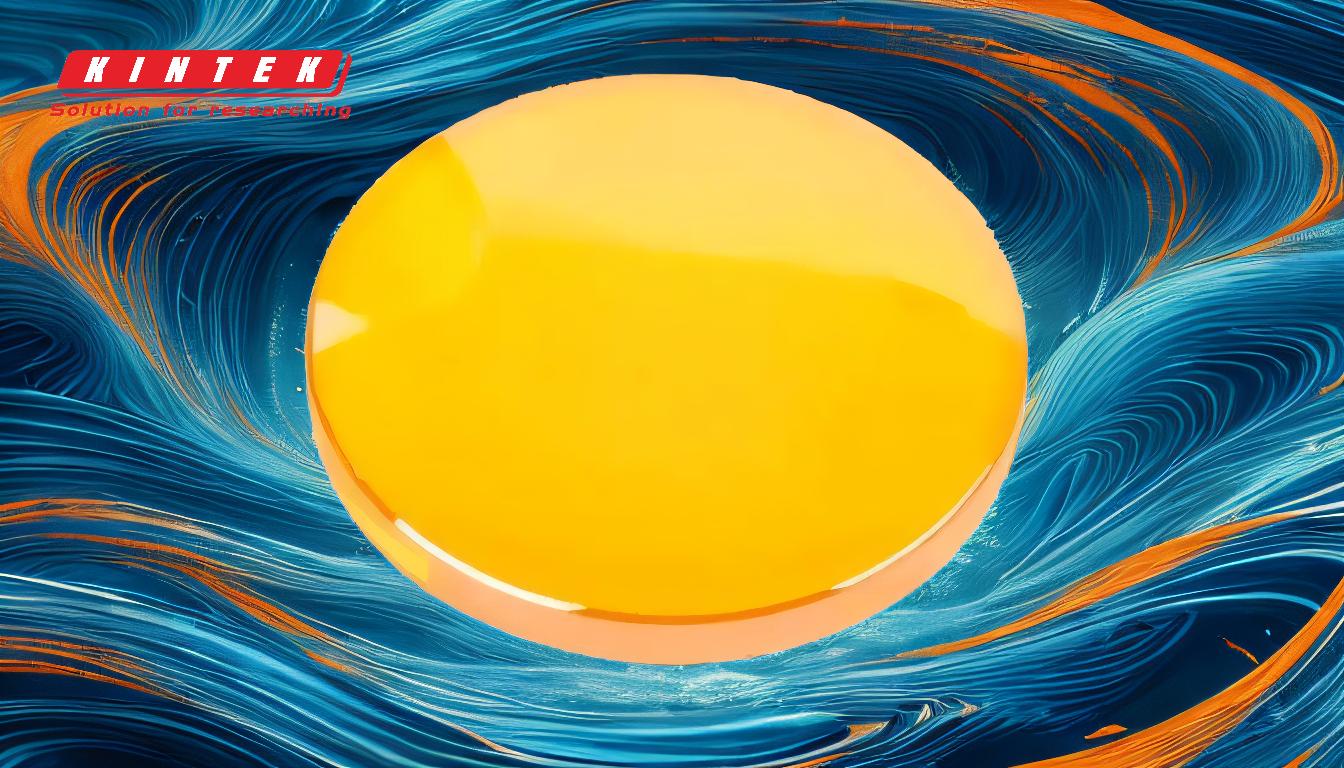
-
Substrate Temperature and Adhesion:
- Heating the substrate above 150 °C improves the mobility of evaporated atoms, allowing them to form a more uniform and adherent film. This is particularly important in vacuum deposition processes, where proper adhesion ensures the film's durability and functionality.
-
Influence of Substrate Properties:
- The substrate's inherent properties, such as surface energy, composition, and microstructure, significantly affect the thin film's characteristics. For example, a smooth substrate can reduce defects in the film, while a rough substrate may lead to uneven deposition and poor adhesion.
-
Deposition Techniques and Film Thickness:
- Different deposition techniques (e.g., CVD, PVD) and film thicknesses can drastically alter the film's properties. The energy of incoming adatoms, their surface mobility, and processes like re-sputtering and ion implantation are influenced by the substrate, leading to variations in film microstructure and performance.
-
Optical Properties:
- The substrate's influence extends to the optical properties of thin films. Factors such as film roughness, thickness, and structural defects (e.g., voids, oxide bonds) are modulated by the substrate, affecting the film's transmission and reflection coefficients.
-
Environmental Factors:
- The residual gas composition in the deposition chamber and the deposition rate are also influenced by the substrate. These factors can alter the film's chemical composition and structural integrity, impacting its overall quality.
-
Quality Control and Manufacturing Considerations:
- When manufacturing thin films, the substrate's properties must be carefully considered alongside quality control measures, client specifications, cost, and efficiency. Ensuring compatibility between the substrate and the deposition process is crucial for producing high-quality films that meet performance requirements.
In summary, the substrate plays a pivotal role in shaping the properties and performance of thin films. By understanding and optimizing the interactions between the substrate and the deposition process, manufacturers can produce thin films with tailored characteristics for specific applications.
Summary Table:
Factor | Impact on Thin Films |
---|---|
Substrate Temperature | Enhances adhesion and uniformity when heated above 150 °C. |
Surface Energy & Composition | Affects film characteristics; smooth substrates reduce defects, rough ones cause issues. |
Deposition Techniques | Techniques like CVD and PVD alter film properties based on substrate interaction. |
Film Thickness | Influences microstructure and performance, modulated by substrate properties. |
Optical Properties | Substrate affects film roughness, thickness, and defects, altering optical performance. |
Environmental Factors | Residual gas composition and deposition rate impact film quality and structural integrity. |
Optimize your thin film manufacturing process—contact our experts today for tailored solutions!