The electron beam physical vapor deposition (EB-PVD) process is a sophisticated technique used to create thin, durable, and high-performance coatings on substrates. It involves vaporizing a source material using an electron beam in a vacuum chamber, which then condenses onto a substrate to form a thin film. This process is highly controlled, allowing for precise thickness and uniformity of the coating. EB-PVD is particularly valued for its ability to produce coatings with excellent adhesion, density, and thermal stability, making it ideal for applications in optics, aerospace, and high-temperature environments. The process can be further enhanced with ion beam assistance to improve coating properties such as density and stress resistance.
Key Points Explained:
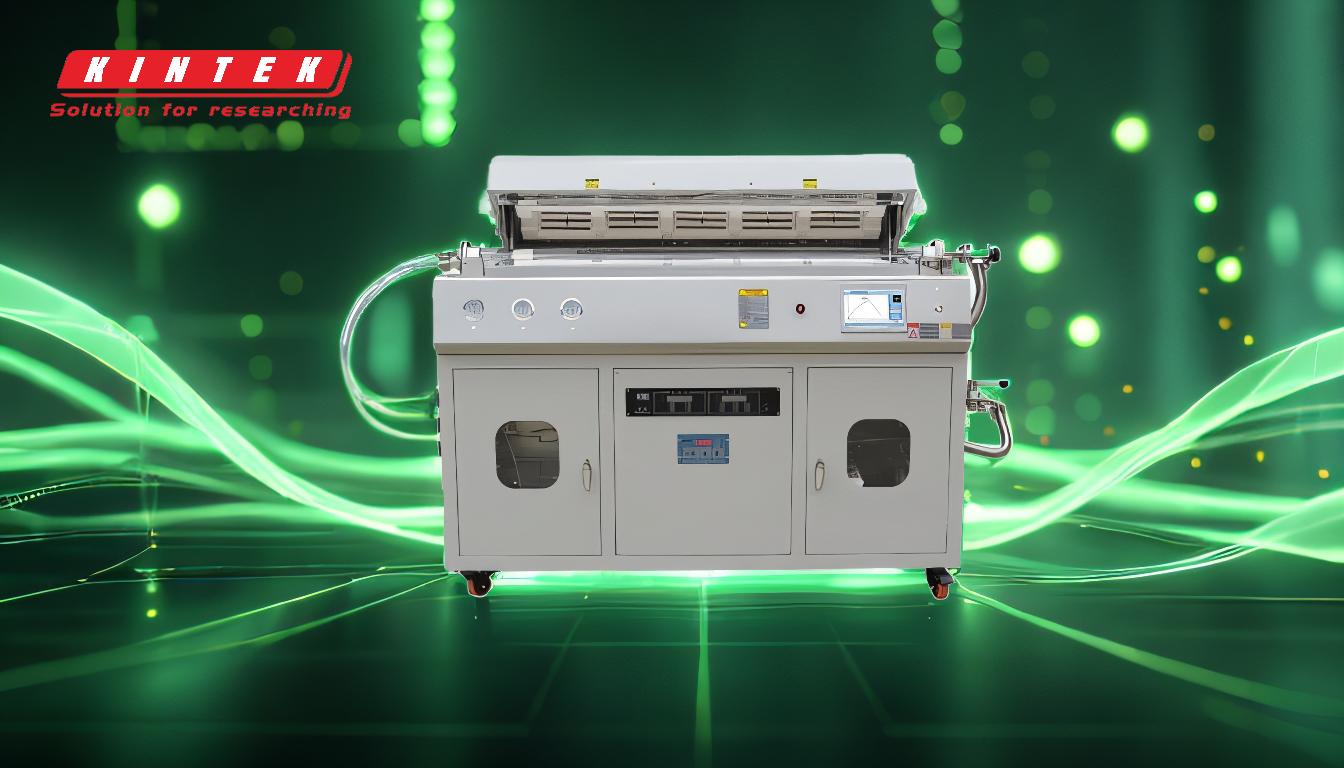
-
Vaporization of Source Material:
- In EB-PVD, the source material (often in powder or granular form) is vaporized using an electron beam. This beam provides intense localized heating, which efficiently converts the solid material into a vapor phase.
- The vaporization occurs in a vacuum chamber to minimize contamination and ensure that the vaporized atoms travel directly to the substrate without interference from gas molecules.
-
Condensation and Deposition:
- The vaporized material condenses onto the substrate, forming a thin film. This process is highly controlled, with parameters such as vacuum levels, substrate position, and rotation being precisely managed to achieve the desired coating thickness and uniformity.
- The condensation process ensures that the coating is conformal, meaning it evenly covers the substrate, even on complex geometries.
-
Enhancement with Ion Beam:
- The EB-PVD process can be enhanced by using an ion beam, which bombards the substrate during deposition. This ion beam assistance increases the adhesion energy between the coating and the substrate, resulting in denser and more robust coatings.
- Ion beam assistance also helps to reduce internal stresses within the coating, which can improve the coating's durability and performance under thermal and mechanical stress.
-
Applications and Advantages:
- EB-PVD is widely used in industries that require high-performance coatings, such as aerospace (for turbine blades), optics (for anti-reflective coatings), and electronics (for thin-film circuits).
- The process offers several advantages, including the ability to deposit a wide range of materials, excellent control over coating thickness and uniformity, and the production of coatings with superior adhesion and thermal stability.
-
Comparison with Other PVD Techniques:
- Unlike other physical vapor deposition (PVD) methods, such as sputtering or thermal evaporation, EB-PVD uses an electron beam for vaporization, which allows for higher energy input and more efficient material utilization.
- EB-PVD is particularly advantageous for depositing materials with high melting points, as the electron beam can achieve the necessary temperatures more effectively than other methods.
-
Process Control and Precision:
- The EB-PVD process is highly automated, with computer-controlled systems managing the electron beam, vacuum levels, and substrate movement. This precision ensures consistent quality and repeatability in the coatings produced.
- The ability to control the deposition rate and substrate conditions allows for the creation of coatings with specific properties, such as graded compositions or multilayered structures.
In summary, the electron beam physical vapor deposition process is a highly advanced and precise method for creating thin, durable coatings on various substrates. Its ability to produce coatings with excellent adhesion, density, and thermal stability makes it a preferred choice for demanding applications in industries such as aerospace, optics, and electronics. The process can be further enhanced with ion beam assistance, resulting in even more robust and high-performance coatings.
Summary Table:
Key Aspect | Details |
---|---|
Process Overview | Vaporizes source material using an electron beam in a vacuum chamber. |
Key Features | Precise thickness, uniformity, excellent adhesion, and thermal stability. |
Enhancements | Ion beam assistance improves density and stress resistance. |
Applications | Aerospace, optics, electronics, and high-temperature environments. |
Advantages | Superior adhesion, conformal coatings, and high material utilization. |
Comparison with Other PVD | Higher energy input, efficient for high-melting-point materials. |
Interested in advanced coating solutions? Contact us today to learn more about EB-PVD technology!