The evaporation method in Physical Vapor Deposition (PVD) is a widely used technique for depositing thin films of material onto a substrate. This method involves heating the material until it evaporates, forming a vapor that then condenses onto the substrate to form a thin film. The process is highly controllable and can produce films with excellent purity, uniformity, and adhesion. Common techniques within the evaporation method include thermal evaporation and electron beam evaporation, each utilizing different heating mechanisms to achieve the desired vaporization of the material.
Key Points Explained:
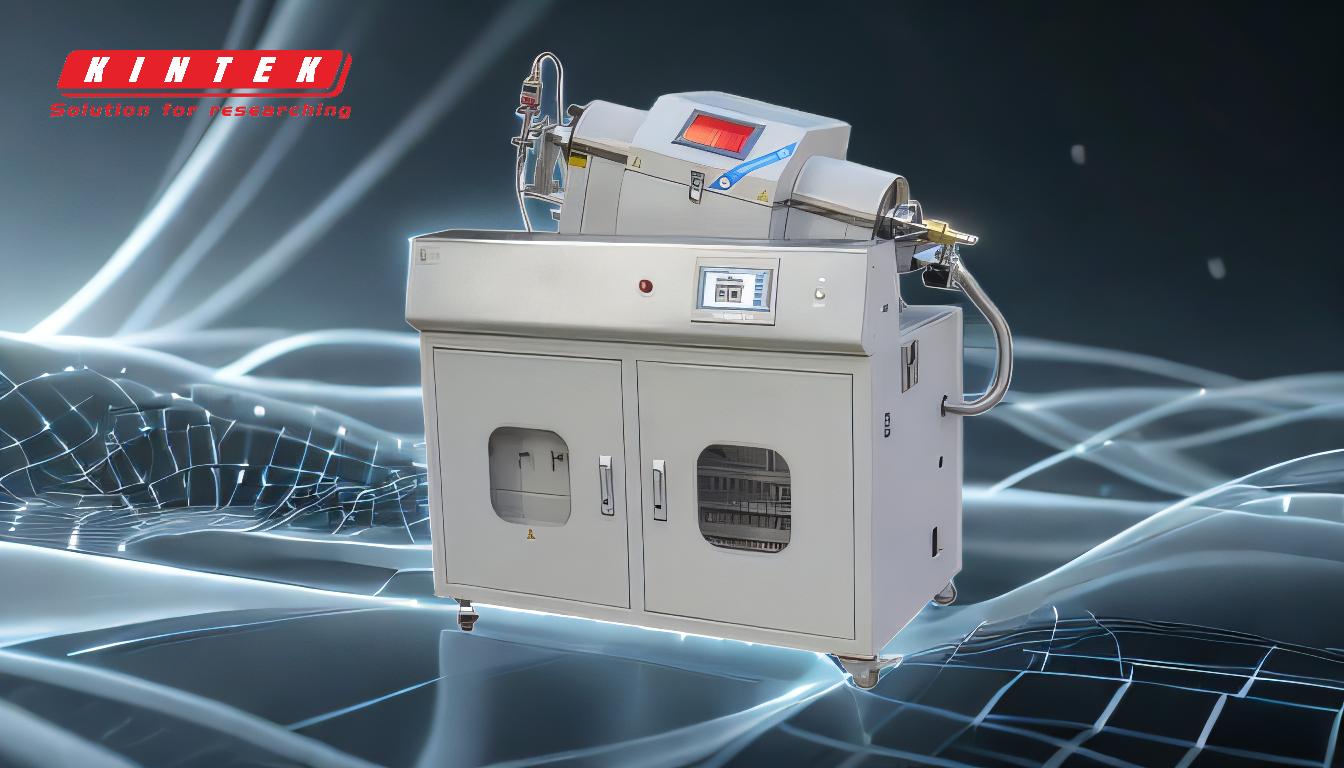
-
Thermal Evaporation Deposition:
- In thermal evaporation, the material to be deposited is placed in a resistance boat or coil, which is typically made of a broad metal ribbon with a large dimple. Material pellets are placed in the dimple, and an electric current is passed through the ribbon to heat it. This heating causes the pellets to melt and eventually evaporate. The vapor then travels through the vacuum and deposits onto the substrate, forming a thin film.
- This method is particularly useful for materials that can be easily vaporized at relatively low temperatures. It is a straightforward and cost-effective technique, making it popular in various applications, including the production of optical coatings and electronic devices.
-
Electron Beam Evaporation:
- Electron beam evaporation is a more advanced technique where an electron beam is used to heat the material. The electron beam is focused onto the material, causing it to heat up rapidly and evaporate. The vapor then deposits onto the substrate, forming a thin film.
- This method is particularly useful for materials that require high temperatures to evaporate, as the electron beam can provide a concentrated heat source. It is often used in applications requiring high-purity films, such as in the semiconductor industry. The films produced by electron beam evaporation typically have excellent reflectivity properties, making them suitable for optical applications.
-
Advantages of the Evaporation Method:
- High Purity: The evaporation method can produce films with extremely high purity, as the process occurs in a vacuum, minimizing contamination.
- Uniformity: The films produced are highly uniform, which is crucial for applications requiring precise thickness control.
- Adhesion: The films adhere well to the substrate, ensuring durability and longevity.
- Versatility: The method can be used with a wide range of materials, including metals, semiconductors, and insulators.
-
Comparison with Other PVD Methods:
- Thermal Vapor Deposition: Similar to thermal evaporation, but typically involves heating the material using an electric heater until it enters the gas phase. This method is also used to produce pure and uniform films.
- Molecular Beam Epitaxy (MBE): A more specialized form of PVD used for growing high-quality crystalline films. It involves the use of molecular beams in an ultra-high vacuum environment.
- Ion Beam Sputtering Deposition: Involves bombarding a target material with ions to eject atoms, which then deposit onto the substrate. This method is known for producing films with excellent adhesion and density.
-
Applications of the Evaporation Method:
- Optical Coatings: Used to create reflective and anti-reflective coatings on lenses and mirrors.
- Electronics: Essential for depositing thin films in the fabrication of semiconductors and other electronic components.
- Decorative Coatings: Used to apply thin films for aesthetic purposes, such as on jewelry or automotive parts.
- Barrier Layers: Applied in packaging to create barrier layers that protect products from moisture and oxygen.
In summary, the evaporation method in PVD is a versatile and effective technique for depositing thin films with high purity, uniformity, and adhesion. It includes both thermal evaporation and electron beam evaporation, each suited to different materials and applications. The method is widely used in industries ranging from electronics to optics, making it a cornerstone of modern thin-film technology.
Summary Table:
Aspect | Details |
---|---|
Techniques | Thermal Evaporation, Electron Beam Evaporation |
Advantages | High Purity, Uniformity, Adhesion, Versatility |
Applications | Optical Coatings, Electronics, Decorative Coatings, Barrier Layers |
Comparison with PVD | Thermal Vapor Deposition, Molecular Beam Epitaxy, Ion Beam Sputtering |
Discover how the evaporation method can enhance your thin-film processes—contact our experts today!