E-beam evaporation is a highly precise thin-film deposition technique used in various industries, including semiconductors, optics, and coatings. It involves using a high-energy electron beam to heat and evaporate a source material in a vacuum chamber. The evaporated particles then condense onto a substrate, forming a thin, high-purity film. This method is particularly effective for materials with high melting points and allows for precise control over film thickness, typically ranging from 5 to 250 nanometers. The process ensures minimal contamination and excellent adhesion, making it ideal for applications requiring high-quality coatings.
Key Points Explained:
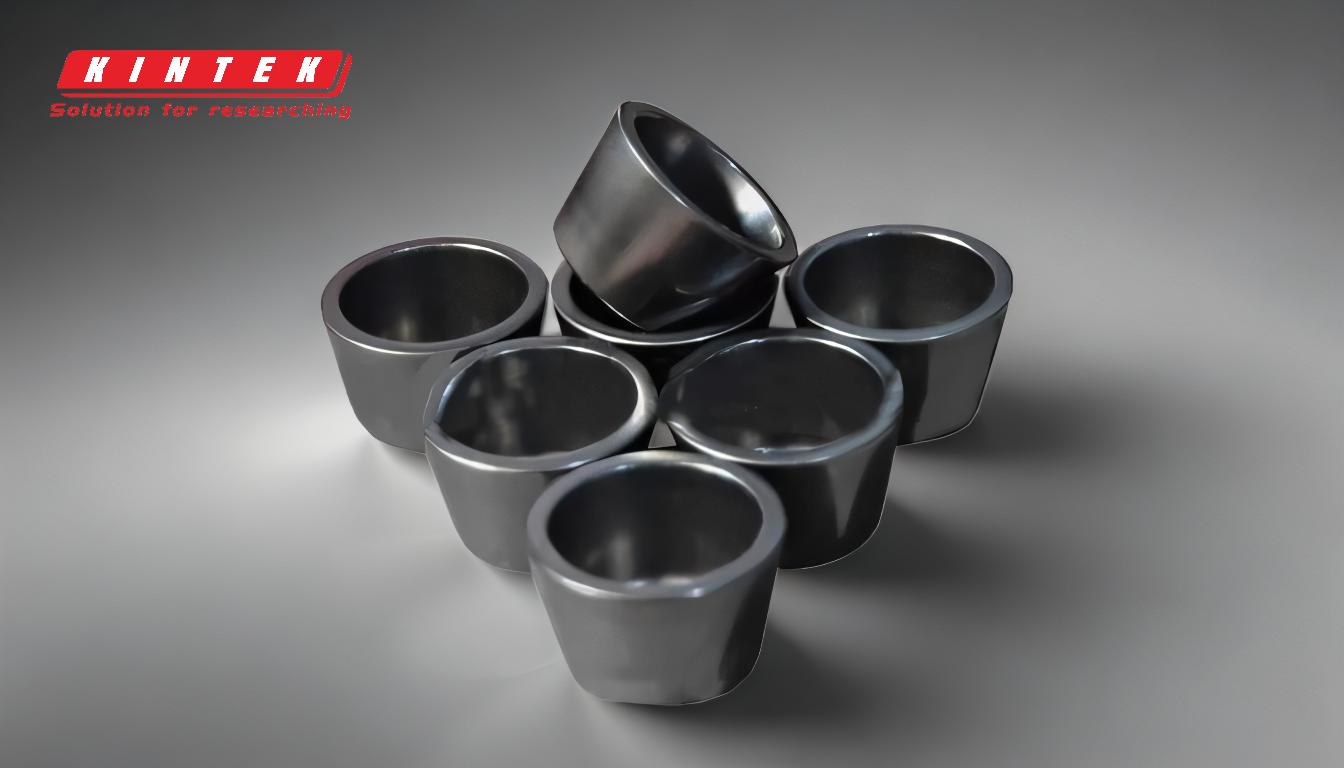
1. Overview of E-Beam Evaporation
- E-beam evaporation is a type of Physical Vapor Deposition (PVD) process.
- It uses a high-energy electron beam to heat and vaporize a source material.
- The vaporized material condenses onto a substrate, forming a thin film.
- This technique is widely used for depositing metals, alloys, and other materials with high melting points.
2. Key Components of the Process
- Electron Beam Gun: Generates and directs a high-energy electron beam toward the source material.
- Crucible or Water-Cooled Copper Hearth: Holds the source material and is designed to withstand high temperatures.
- Vacuum Chamber: Ensures a contamination-free environment and allows the evaporated particles to travel unimpeded to the substrate.
- Substrate: The surface onto which the thin film is deposited.
- Quartz Crystal Microbalances: Used to monitor and control the deposition rate and film thickness.
3. Step-by-Step Process
- Electron Beam Generation: High-voltage electrons are accelerated and focused into a beam using an electron gun.
- Heating and Evaporation: The electron beam strikes the source material in the crucible, generating intense heat that melts and evaporates the material.
- Vapor Flow: The evaporated particles travel upward in the vacuum chamber due to the low-pressure environment.
- Deposition: The vaporized material condenses onto the substrate, forming a thin, uniform film.
- Cooling and Monitoring: The crucible is often water-cooled to prevent contamination, and quartz crystal microbalances ensure precise control over the deposition process.
4. Advantages of E-Beam Evaporation
- High Purity: The vacuum environment minimizes contamination, resulting in high-purity films.
- Precision Control: Allows for precise control over film thickness, typically ranging from 5 to 250 nanometers.
- Versatility: Suitable for depositing a wide range of materials, including those with high melting points (e.g., gold, tungsten).
- Excellent Adhesion: Produces films with strong adhesion to the substrate.
- Dimensional Accuracy: Does not alter the substrate's dimensional properties.
5. Applications of E-Beam Evaporation
- Semiconductors: Used for depositing conductive and dielectric layers in microelectronics.
- Optics: Applied in the production of anti-reflective coatings, mirrors, and filters.
- Decorative Coatings: Used for creating durable and aesthetically pleasing finishes.
- Research and Development: Ideal for prototyping and testing new materials and coatings.
6. Comparison with Other Deposition Techniques
- Thermal Evaporation: E-beam evaporation allows for higher energy transfer, making it suitable for materials with higher melting points.
- Sputtering: E-beam evaporation typically provides better purity and adhesion but may require more complex equipment.
- Chemical Vapor Deposition (CVD): E-beam evaporation is a purely physical process, avoiding chemical reactions that can introduce impurities.
7. Challenges and Considerations
- Equipment Cost: E-beam evaporation systems can be expensive due to the need for high-vacuum environments and precision components.
- Material Compatibility: Not all materials are suitable for e-beam evaporation; some may decompose or react under high-energy conditions.
- Uniformity: Achieving uniform coatings over large or complex substrates can be challenging and may require advanced deposition control systems.
By understanding the principles, components, and advantages of e-beam evaporation, users can effectively leverage this technique for high-quality thin-film deposition in various applications.
Summary Table:
Aspect | Details |
---|---|
Process Type | Physical Vapor Deposition (PVD) |
Key Components | Electron Beam Gun, Crucible, Vacuum Chamber, Substrate, Quartz Microbalance |
Film Thickness Range | 5 to 250 nanometers |
Advantages | High purity, precise control, versatility, excellent adhesion |
Applications | Semiconductors, optics, decorative coatings, R&D |
Challenges | High equipment cost, material compatibility, uniformity issues |
Ready to explore e-beam evaporation for your project? Contact our experts today to get started!