Flash sintering is an innovative method in ceramics consolidation that significantly reduces both the time and temperature required for densification. This technique opens up new possibilities for processing materials that are metastable, out-of-equilibrium, or contain volatile components. It is known for its simplicity, low technical requirements, and rapid sintering speed, making it a highly efficient alternative to traditional sintering methods.
Key Points Explained:
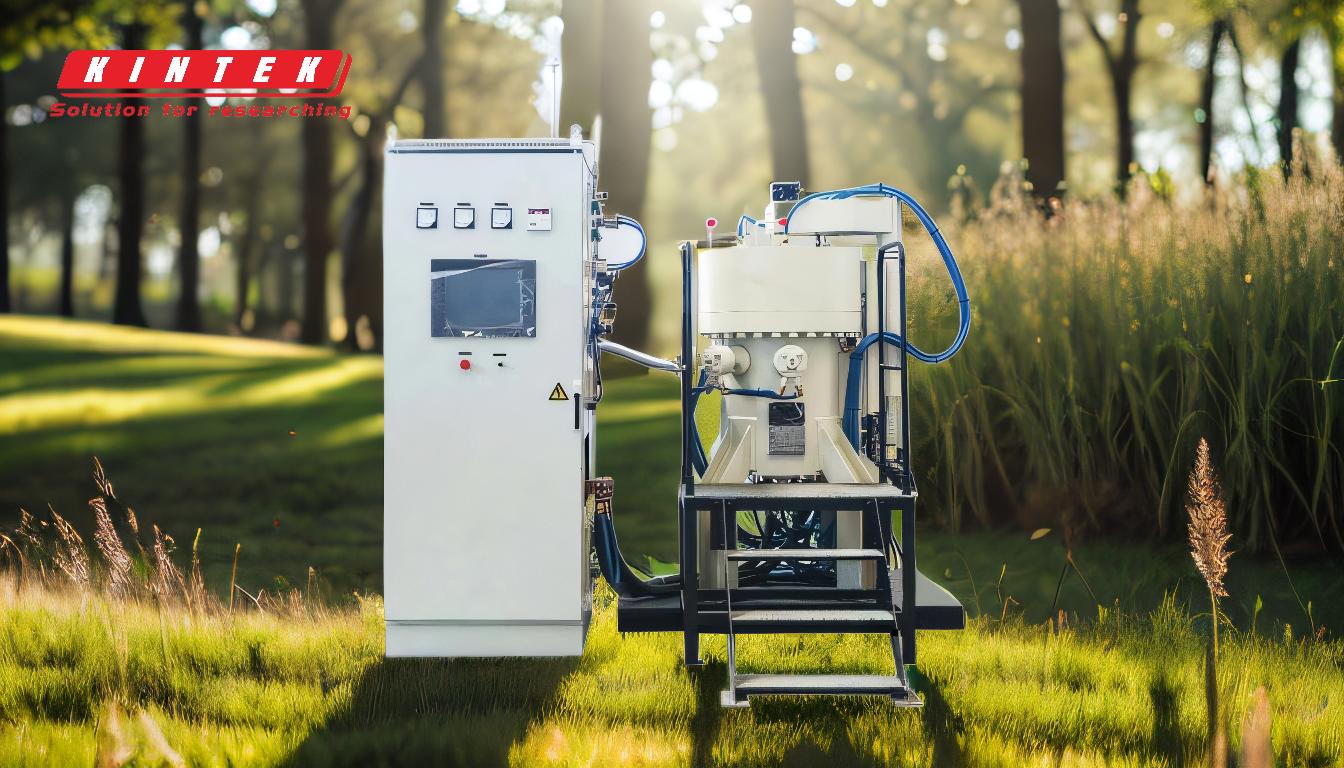
-
Definition and Overview of Flash Sintering:
- Flash sintering is a novel technique in the field of ceramics that enables the densification of materials at lower temperatures and in shorter times compared to conventional sintering methods. This process involves applying an electric field to the material while it is heated, which induces rapid densification.
-
Reduction in Densification Time and Temperature:
- One of the standout features of flash sintering is its ability to significantly reduce the time and temperature required for densification. Traditional sintering processes can take hours and require high temperatures, but flash sintering can achieve similar or even better results in a matter of minutes and at much lower temperatures.
-
Processing of Special Materials:
- Flash sintering is particularly advantageous for processing materials that are difficult to densify using conventional methods. This includes metastable materials, which are not in their most stable state, and out-of-equilibrium materials, which are not in thermodynamic equilibrium. Additionally, it is effective for materials that contain volatile components, which might otherwise be lost or degraded during traditional sintering.
-
Advantages of Flash Sintering:
- Simple Operation: The process is straightforward and does not require complex machinery or setups.
- Low Technical Requirements: It can be performed with relatively basic equipment, making it accessible for a wide range of applications.
- Fast Sintering Speed: The rapid nature of the process allows for quick turnaround times, which is beneficial for both research and industrial applications.
-
Potential Applications and Future Directions:
- The ability to process a wide range of materials quickly and at lower temperatures makes flash sintering a promising technique for various applications, including advanced ceramics, electronic components, and energy storage materials. Ongoing research is likely to expand its applicability and optimize the process further.
In summary, flash sintering represents a significant advancement in ceramics processing, offering a faster, more efficient, and versatile alternative to traditional methods. Its ability to handle challenging materials and its operational simplicity make it a valuable tool in both research and industry.
Summary Table:
Aspect | Details |
---|---|
Definition | A novel ceramics densification method using electric fields and lower heat. |
Key Benefit | Reduces densification time and temperature significantly. |
Materials Processed | Metastable, out-of-equilibrium, and volatile-component materials. |
Advantages | Simple operation, low technical requirements, and fast sintering speed. |
Applications | Advanced ceramics, electronic components, and energy storage materials. |
Interested in flash sintering for your ceramics processing? Contact our experts today to learn more!