Physical Vapor Deposition (PVD) is a sophisticated process used to deposit thin films of material onto a substrate. It involves the transformation of a solid material into a vapor phase, which then condenses onto a substrate to form a thin film. This process is conducted in a vacuum chamber, typically at temperatures ranging from 50 to 600 degrees Celsius. The most common methods of PVD include sputtering and evaporation. Sputtering involves ejecting atoms from a target material by bombarding it with high-energy particles, while evaporation involves heating the target material until it vaporizes. The vaporized material then travels through the chamber and condenses onto the substrate, forming a thin film with excellent adhesion and durability. PVD is widely used in various industries due to its ability to produce high-quality, corrosion-resistant, and temperature-tolerant coatings.
Key Points Explained:
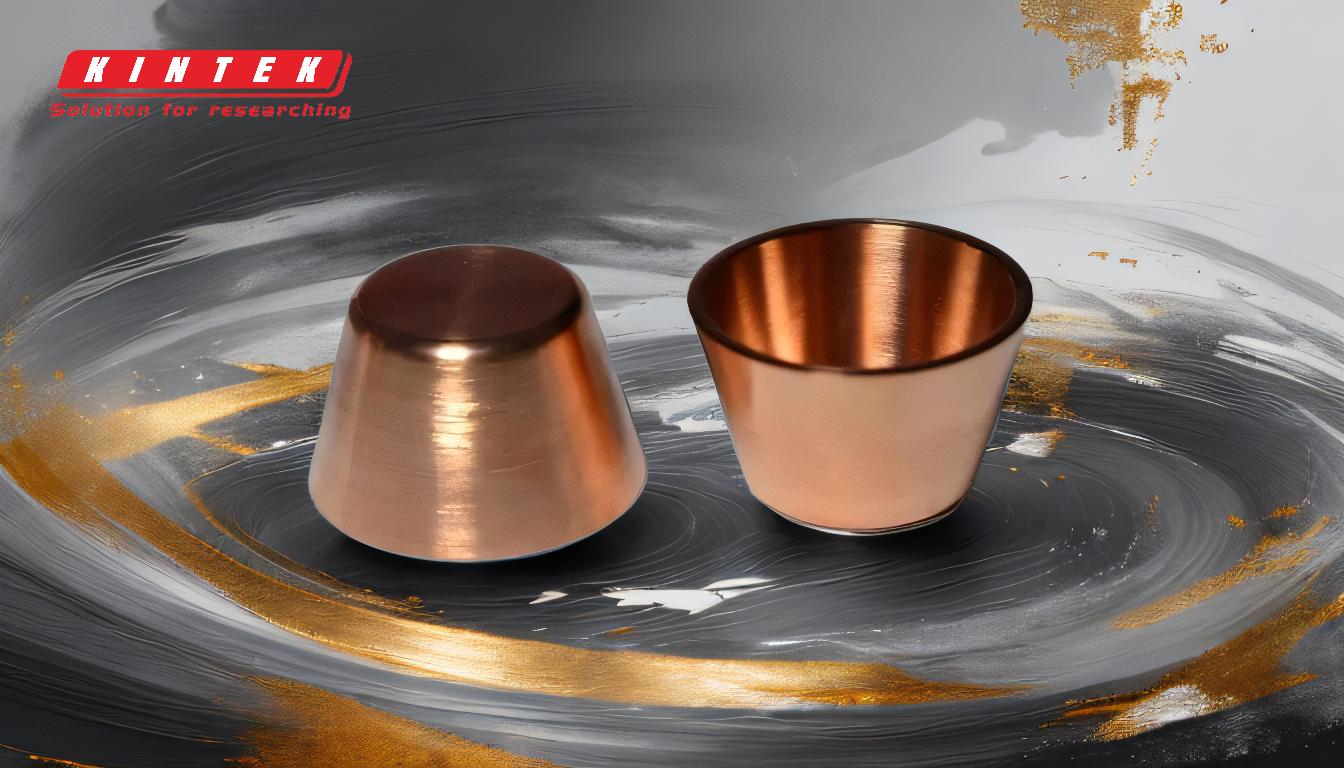
-
Definition and Basic Concept of PVD:
- Physical Vapor Deposition (PVD) is a process where a solid material is transformed into a vapor phase and then condensed onto a substrate to form a thin film.
- This process is carried out in a vacuum chamber to prevent contamination and ensure the purity of the deposited material.
-
Common PVD Methods:
- Sputtering: This method involves bombarding a target material with high-energy particles, causing atoms to be ejected from the target and deposited onto the substrate.
- Evaporation: In this method, the target material is heated until it vaporizes. The vapor then travels through the chamber and condenses onto the substrate.
-
Process Conditions:
- PVD processes are typically conducted in a vacuum chamber to maintain a clean environment and prevent oxidation or contamination.
- The temperature in the chamber usually ranges from 50 to 600 degrees Celsius, depending on the material and the desired properties of the thin film.
-
Material Transformation:
- The target material undergoes a phase transition from solid to vapor, which is then transported through the vacuum chamber.
- The vaporized material condenses onto the substrate, forming a thin film with strong adhesion and uniform thickness.
-
Applications and Advantages:
- PVD is used to create thin films with excellent adhesion, durability, and resistance to corrosion and high temperatures.
- It is widely applied in industries such as electronics, optics, and aerospace for coating components that require high performance and reliability.
-
Technological Variations:
- PVD can be performed using different techniques such as electron beam evaporation, laser beam evaporation, arc discharge, and sputtering.
- Each technique has its own advantages and is chosen based on the specific requirements of the application.
-
Substrate and Coating Interaction:
- The substrate and coating material are placed in the vacuum chamber, and the coating material (target) is evaporated using one of the mentioned methods.
- The evaporated material is accelerated away from the target, diffuses to the substrate, and condenses upon hitting the substrate's surface, forming a coating.
-
Material Handling and Versatility:
- PVD is capable of handling materials with high melting points, making it suitable for a wide range of applications.
- The process can be used to deposit a variety of materials, including metals, alloys, and ceramics, onto different types of substrates.
-
Environmental and Operational Considerations:
- The vacuum environment ensures that the process is clean and free from contaminants, which is crucial for achieving high-quality coatings.
- The 'line-of-sight' method ensures that the atoms of the solid material pass through the chamber and embed themselves into the objects in their path, resulting in precise and controlled deposition.
-
Future Prospects and Innovations:
- Ongoing research and development in PVD technology aim to improve the efficiency, scalability, and cost-effectiveness of the process.
- Innovations in PVD techniques are expected to expand its applications in emerging fields such as nanotechnology and renewable energy.
By understanding these key points, one can appreciate the complexity and versatility of the PVD process, which plays a crucial role in modern manufacturing and material science.
Summary Table:
Aspect | Details |
---|---|
Definition | Transformation of solid material into vapor, condensing onto a substrate. |
Common Methods | Sputtering, Evaporation. |
Process Conditions | Conducted in a vacuum chamber at 50–600°C. |
Material Handling | Metals, alloys, ceramics, high melting points. |
Applications | Electronics, optics, aerospace, and more. |
Advantages | High adhesion, durability, corrosion resistance, and temperature tolerance. |
Discover how PVD can enhance your manufacturing process—contact our experts today!