Heat treatment, while essential for enhancing the properties of metals, carries several hazards if not properly controlled. The primary risks include compromised material quality, financial losses, wasted time, and potential safety hazards for both employees and end-users. Improperly controlled atmospheres during heat treatment can lead to chemical reactions on the metal surface, resulting in rejected parts and damaged equipment. Additionally, there is a risk of injury to employees and long-term repercussions for customers who may unknowingly use defective parts. These hazards underscore the importance of precise control and monitoring during the heat treatment process.
Key Points Explained:
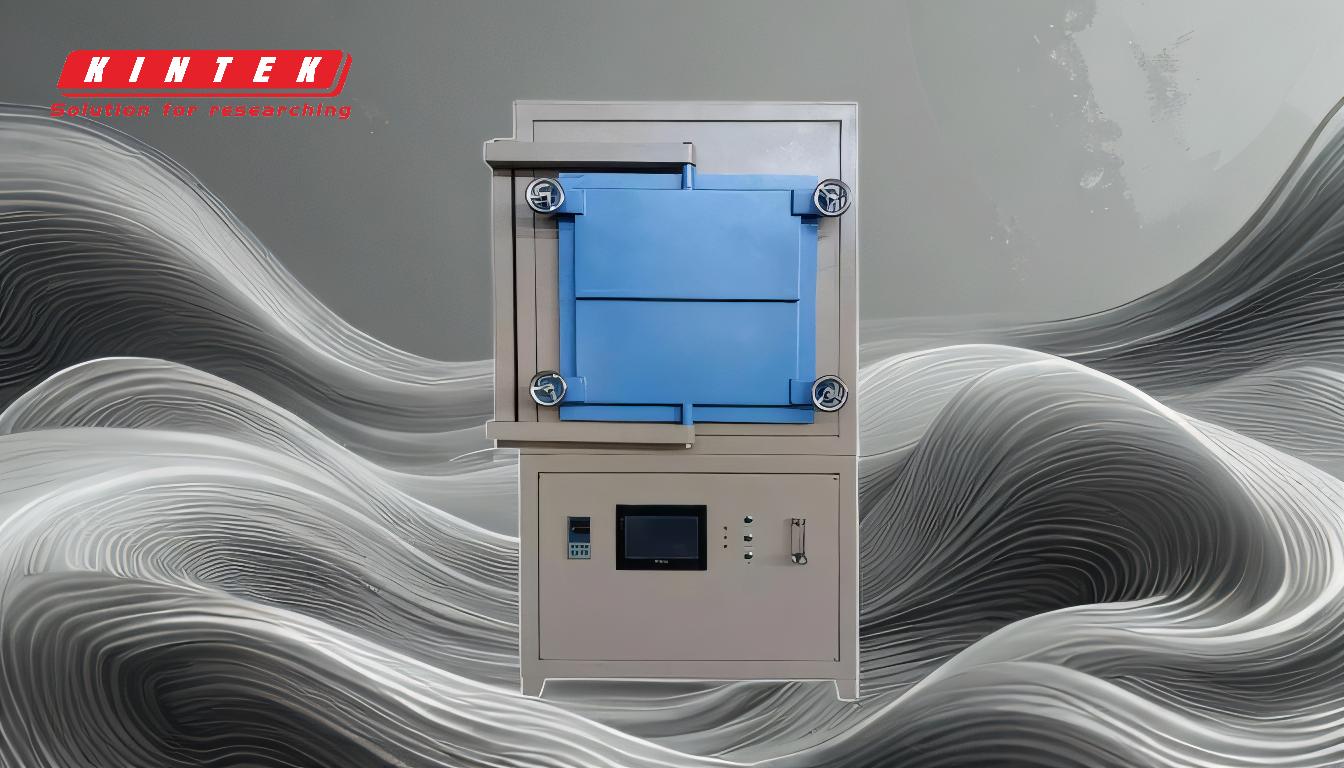
-
Compromised Material Quality
- Chemical Reactions on Metal Surface: An improperly controlled atmosphere during heat treatment can cause unwanted chemical reactions, such as oxidation or decarburization, on the surface of the metal alloy. These reactions degrade the material's mechanical properties, such as hardness, strength, and fatigue resistance.
- Impact on Performance: Compromised material quality can lead to parts that fail to meet specifications, resulting in reduced performance or premature failure in their intended applications.
-
Financial Losses
- Rejected Parts: Parts that do not meet quality standards due to improper heat treatment must be scrapped or reworked, leading to significant material and labor costs.
- Wasted Time: The time invested in processing defective parts is lost, delaying production schedules and increasing operational costs.
- Damage to Equipment: Improper heat treatment can also damage furnaces or other equipment, necessitating costly repairs or replacements.
-
Safety Hazards
- Employee Injuries: Heat treatment processes often involve high temperatures and hazardous chemicals. Improper handling or equipment failure can lead to burns, exposure to toxic fumes, or other workplace injuries.
- End-User Risks: If defective parts are not detected and make their way to customers, they can fail during use, potentially causing accidents or injuries. This not only endangers users but also exposes the manufacturer to legal liabilities and reputational damage.
-
Long-Term Repercussions
- Customer Trust: Delivering defective parts can erode customer trust and damage long-term business relationships.
- Regulatory Non-Compliance: Failure to meet quality standards may result in violations of industry regulations, leading to fines or other penalties.
-
Preventive Measures
- Controlled Atmosphere: Maintaining a precisely controlled atmosphere during heat treatment is critical to preventing unwanted chemical reactions. This includes monitoring and regulating temperature, gas composition, and pressure.
- Quality Control: Implementing rigorous quality control measures, such as regular inspections and testing, can help identify and address issues before parts are shipped to customers.
- Employee Training: Proper training for employees on heat treatment processes and safety protocols can reduce the risk of accidents and ensure consistent quality.
By understanding and addressing these hazards, manufacturers can minimize risks, improve product quality, and ensure the safety of both employees and end-users.
Summary Table:
Hazard | Description |
---|---|
Compromised Material Quality | Chemical reactions like oxidation degrade mechanical properties, leading to part failure. |
Financial Losses | Rejected parts, wasted time, and equipment damage increase costs. |
Safety Hazards | High temperatures and chemicals pose risks of employee injuries and end-user accidents. |
Long-Term Repercussions | Eroded customer trust, regulatory fines, and reputational damage. |
Preventive Measures | Controlled atmosphere, quality control, and employee training minimize risks. |
Ensure safe and effective heat treatment processes—contact our experts today for guidance!