The heating rate for alumina tubes is a critical factor to ensure their longevity and prevent damage due to thermal shock. Based on the references, the recommended heating rate typically ranges between 5°C/min to 10°C/min, with a preference for slower rates to minimize stress on the material. For the initial heating phase, a slower rate of 150-300°C per hour (2.5-5°C/min) is advised for the first 1-1.5 hours to reduce thermal shock. Additionally, the heating rate should be adjusted based on the temperature range: below 500°C, it should be ≤5°C/min; between 500-800°C, ≤10°C/min; between 800-1000°C, ≤5°C/min; between 1000-1400°C, ≤3°C/min; and between 1400-1600°C, ≤2°C/min. Gradual temperature changes are essential to avoid cracking or breakage.
Key Points Explained:
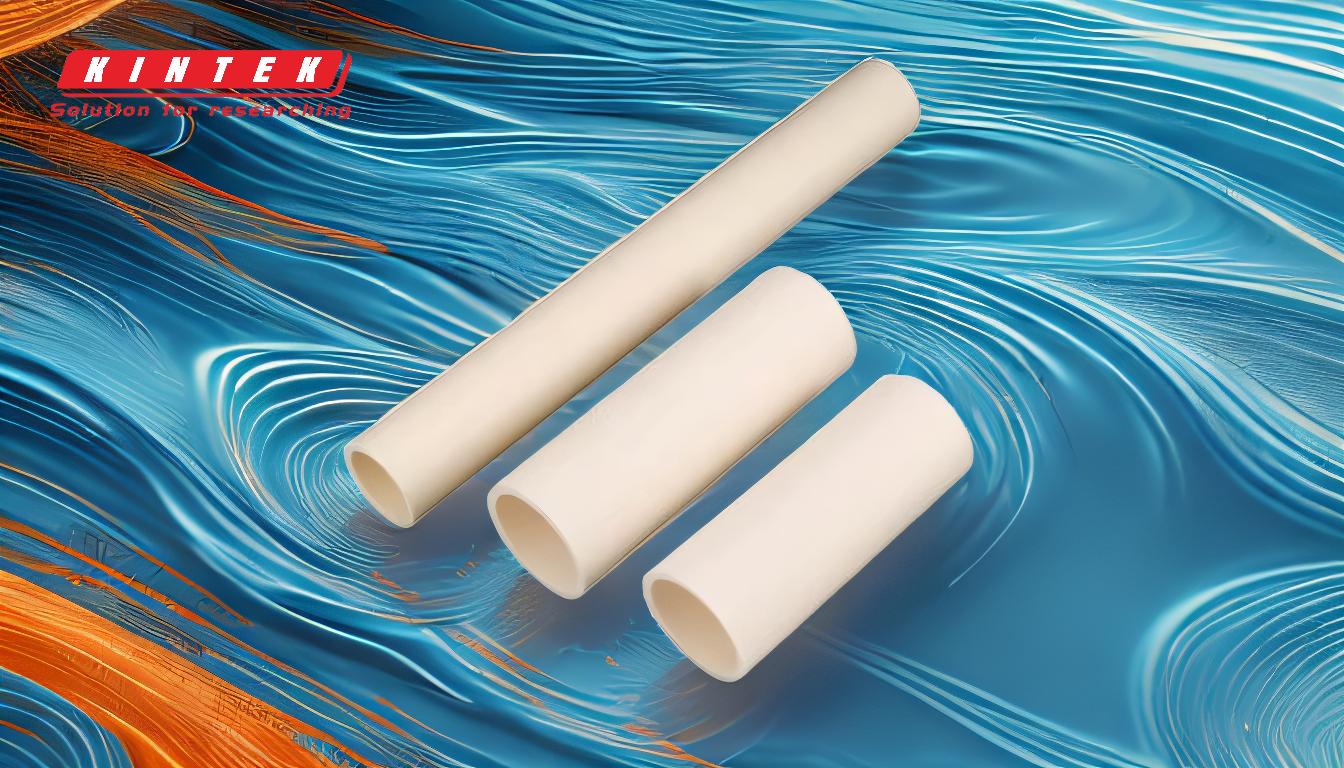
-
General Heating Rate Recommendation:
- The standard heating rate for alumina tubes is 5-10°C/min, with a preference for 5°C/min to minimize thermal stress.
- Slower heating rates are generally better to prevent thermal shock and ensure the material's integrity.
-
Initial Heating Phase:
- During the first 1-1.5 hours of heating, a slower rate of 150-300°C per hour (2.5-5°C/min) is recommended to reduce the risk of thermal shock.
- This gradual approach helps the alumina tube adjust to temperature changes without cracking.
-
Temperature-Specific Heating Rates:
- Below 500°C: Heating rate should be ≤5°C/min.
- 500-800°C: Heating rate can be increased to ≤10°C/min.
- 800-1000°C: Heating rate should be reduced back to ≤5°C/min.
- 1000-1400°C: Heating rate should be further reduced to ≤3°C/min.
- 1400-1600°C: Heating rate should be the slowest at ≤2°C/min.
- These adjustments ensure that the alumina tube is not subjected to rapid temperature changes at critical points in the heating process.
-
Cooling Rate:
- The cooling rate should be ≤10°C/min, with a preference for 5°C/min.
- Natural cooling is discouraged as it can cause rapid temperature drops, leading to breakage.
- Ideally, the cooling rate should be half of the heating rate, typically 75-150°C per hour.
-
Importance of Gradual Temperature Changes:
- Alumina is highly sensitive to thermal shock, so gradual heating and cooling are crucial to avoid damage.
- Rapid temperature changes can lead to cracking or breakage, reducing the lifespan of the alumina tube.
-
Material Properties and Thermal Shock Resistance:
- Alumina tubes have excellent thermal shock resistance, but this property is only effective if the heating and cooling rates are carefully controlled.
- High density, good acid and alkali resistance, and erosion resistance make alumina tubes durable, but improper heating or cooling can negate these benefits.
By adhering to these guidelines, users can ensure the safe and effective use of alumina tubes, maximizing their service life and performance.
Summary Table:
Temperature Range | Recommended Heating Rate |
---|---|
Below 500°C | ≤5°C/min |
500-800°C | ≤10°C/min |
800-1000°C | ≤5°C/min |
1000-1400°C | ≤3°C/min |
1400-1600°C | ≤2°C/min |
Cooling Rate | ≤10°C/min (preferably 5°C/min) |
Ensure your alumina tubes last longer—contact our experts today for personalized guidance!