Diamond-like carbon (DLC) coatings are known for their exceptional properties, including high hardness, low friction, and chemical resistance. However, their performance at high temperatures is a critical consideration for applications involving thermal stress. The high-temperature stability of DLC coatings depends on factors such as the bonding structure (sp3 vs. sp2), hydrogen content, and deposition method. Generally, DLC coatings can withstand temperatures up to 300–400°C before significant degradation occurs, such as graphitization or hydrogen loss. For higher-temperature applications, specialized DLC variants or alternative coatings may be required.
Key Points Explained:
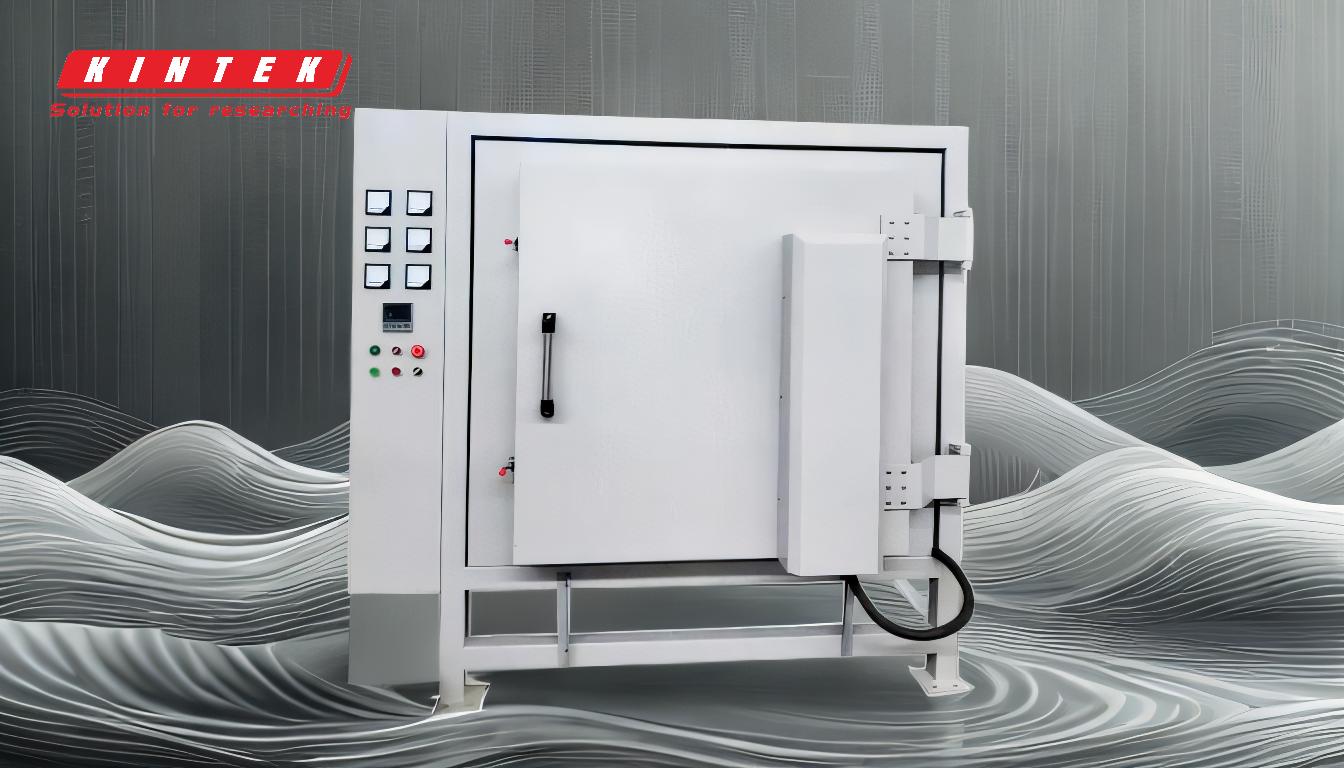
-
DLC Coating Composition and Bonding Structure:
- DLC coatings consist of a mix of sp3 (diamond-like) and sp2 (graphite-like) carbon bonds.
- The sp3 bonds contribute to high hardness and wear resistance, while sp2 bonds influence friction and thermal stability.
- Hydrogenated DLC (a-C:H) contains hydrogen, which affects its thermal properties.
-
Temperature Limits of DLC Coatings:
- Standard DLC coatings typically degrade at temperatures between 300°C and 400°C.
- At higher temperatures, sp3 bonds convert to sp2 bonds (graphitization), reducing hardness and wear resistance.
- Hydrogenated DLC coatings may lose hydrogen at elevated temperatures, further compromising their properties.
-
Factors Influencing High-Temperature Performance:
- Hydrogen Content: Hydrogenated DLC (a-C:H) is less thermally stable than hydrogen-free DLC (ta-C).
- Deposition Method: Techniques like PACVD (Plasma-Assisted Chemical Vapor Deposition) can influence the coating's thermal stability.
- Substrate Material: The thermal expansion mismatch between the coating and substrate can affect performance at high temperatures.
-
Applications and Limitations:
- DLC coatings are ideal for applications below 300°C, such as automotive components, cutting tools, and biomedical devices.
- For high-temperature environments (e.g., aerospace or industrial machinery), alternative coatings like diamond, silicon carbide, or ceramic coatings may be more suitable.
-
Enhancing High-Temperature Stability:
- Doping: Adding elements like silicon or tungsten can improve thermal stability.
- Multilayer Structures: Combining DLC with other materials can enhance performance under thermal stress.
- Post-Treatment: Annealing or laser treatment can modify the coating's structure for better high-temperature resistance.
-
Practical Considerations for Equipment and Consumable Purchasers:
- Evaluate the operating temperature range of the application before selecting a DLC coating.
- Consider the trade-offs between cost, performance, and thermal stability.
- Consult with coating suppliers to identify the best DLC variant or alternative for high-temperature use.
In summary, while DLC coatings offer excellent properties for many applications, their high-temperature performance is limited to around 300–400°C. For higher-temperature environments, alternative solutions or specialized DLC variants should be considered.
Summary Table:
Aspect | Details |
---|---|
Temperature Limit | 300–400°C before degradation (graphitization or hydrogen loss) |
Key Factors | Bonding structure (sp3 vs. sp2), hydrogen content, deposition method |
Applications | Automotive, cutting tools, biomedical devices (below 300°C) |
High-Temperature Solutions | Doping, multilayer structures, post-treatment, or alternative coatings |
Need a coating solution for high-temperature applications? Contact our experts today to find the best fit for your needs!