The hot pressing technique is a specialized manufacturing process used primarily in the production of high-performance materials, such as cemented carbides. It involves the application of heat and pressure simultaneously to achieve high-density products with excellent mechanical properties. This method is particularly advantageous for producing complex and large-shaped products with minimal deformation. However, it comes with limitations, such as low productivity, high costs, and stringent technical requirements. Despite these challenges, hot pressing remains a valuable technique for applications requiring precision and high-quality outputs.
Key Points Explained:
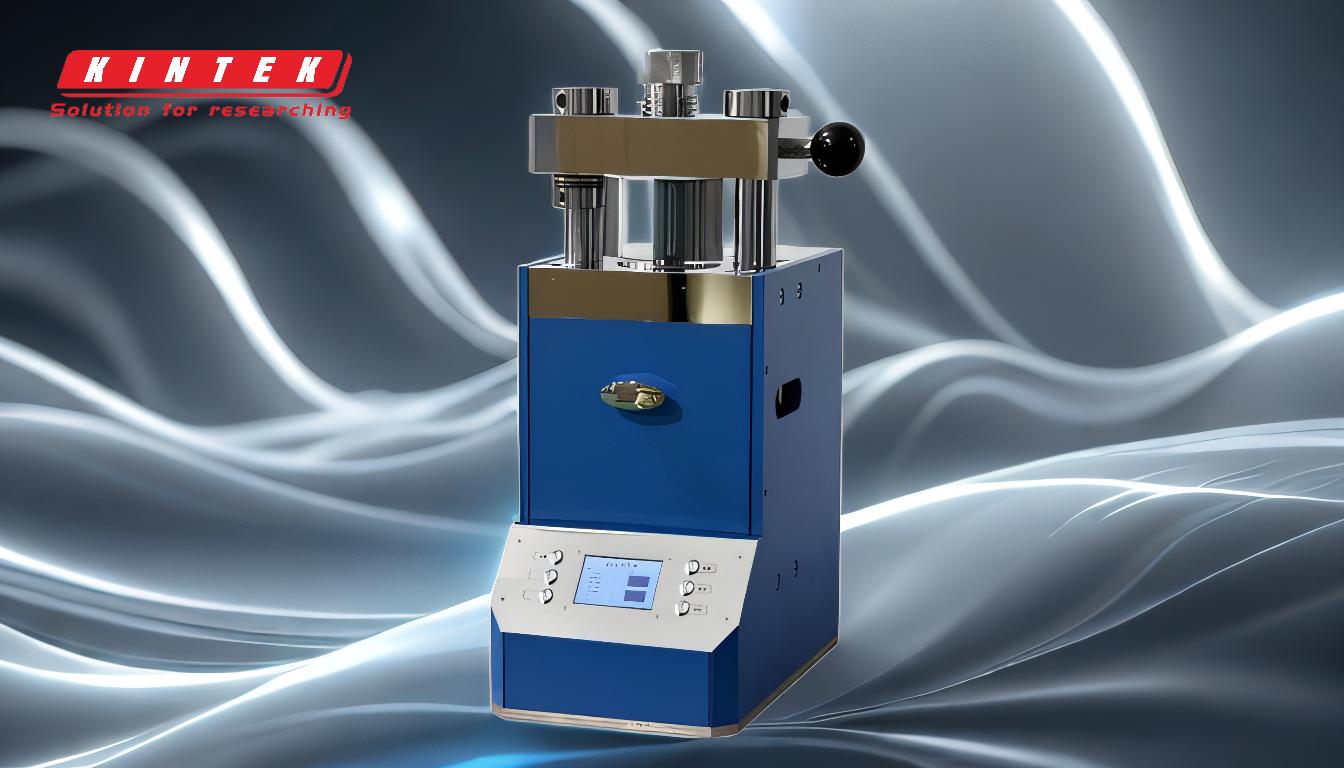
-
Definition and Purpose of Hot Pressing:
- Hot pressing is a process that combines heat and pressure to manufacture materials, particularly cemented carbides. The simultaneous application of these forces ensures high-density products with superior mechanical properties.
-
Advantages of Hot Pressing:
- High Density and Performance: Products manufactured through hot pressing exhibit high density and excellent performance characteristics.
- Small Pressing Pressure: The process requires relatively low pressing pressure, making it feasible to produce large products.
- Complex Shapes: Hot pressing can produce intricately shaped products that might be challenging to achieve with other methods.
- Large, Non-Deformed Products: It is capable of producing large products with minimal deformation.
- Single-Piece Production: Suitable for manufacturing single pieces, which is beneficial for custom or specialized applications.
-
Limitations of Hot Pressing:
- Low Productivity: The process typically allows for the production of only one to a few products at a time, leading to low overall productivity.
- High Costs: The high cost of molds and their short service life contribute to the overall expense of the process.
- Technical Skill Requirements: Managing the combination of temperature and pressure, heating and cooling speeds, and shrinkage control requires high operational technical skills.
-
Comparison with HIP (Hot Isostatic Pressing):
- Shape Retention: Unlike hot pressing, HIP can provide material shapes that are not significantly different from the initial shape after pressure application. This makes HIP suitable for a broader range of applications where shape retention is crucial.
-
Operational Considerations:
- Temperature and Pressure Management: Precise control of temperature and pressure is essential to ensure the quality and performance of the final product.
- Heating and Cooling Speeds: The rates at which the material is heated and cooled must be carefully managed to prevent defects and ensure uniform properties.
- Shrinkage Control: Effective control of shrinkage during the cooling phase is critical to maintaining the dimensional accuracy of the product.
In summary, the hot pressing technique is a highly specialized process that offers significant advantages in terms of product quality and complexity. However, it also presents notable challenges, including high costs and technical demands. Understanding these factors is crucial for equipment and consumable purchasers to make informed decisions about the suitability of hot pressing for their specific applications.
Summary Table:
Aspect | Details |
---|---|
Definition | Combines heat and pressure to produce high-density materials like cemented carbides. |
Advantages | - High density and performance - Small pressing pressure - Complex shapes - Large, non-deformed products - Single-piece production |
Limitations | - Low productivity - High costs - High technical skill requirements |
Comparison with HIP | HIP offers better shape retention, making it suitable for broader applications. |
Operational Considerations | - Precise temperature/pressure control - Managed heating/cooling speeds - Shrinkage control |
Interested in leveraging the hot pressing technique for your applications? Contact our experts today to learn more!