An inert atmosphere in welding refers to the use of non-reactive gases to create a protective environment around the weld area. This prevents contamination from reactive gases in the air, such as oxygen and nitrogen, which can cause defects like porosity, oxidation, or decarburization in the weld. Inert gases like argon and helium are commonly used in processes such as gas tungsten arc welding (GTAW) and vacuum brazing to ensure clean, high-quality welds. The inert atmosphere shields the molten metal, tungsten electrode, and surrounding materials from chemical reactions, preserving the integrity and desired properties of the weld. This controlled environment is essential for achieving precise, durable, and defect-free welds in various industrial applications.
Key Points Explained:
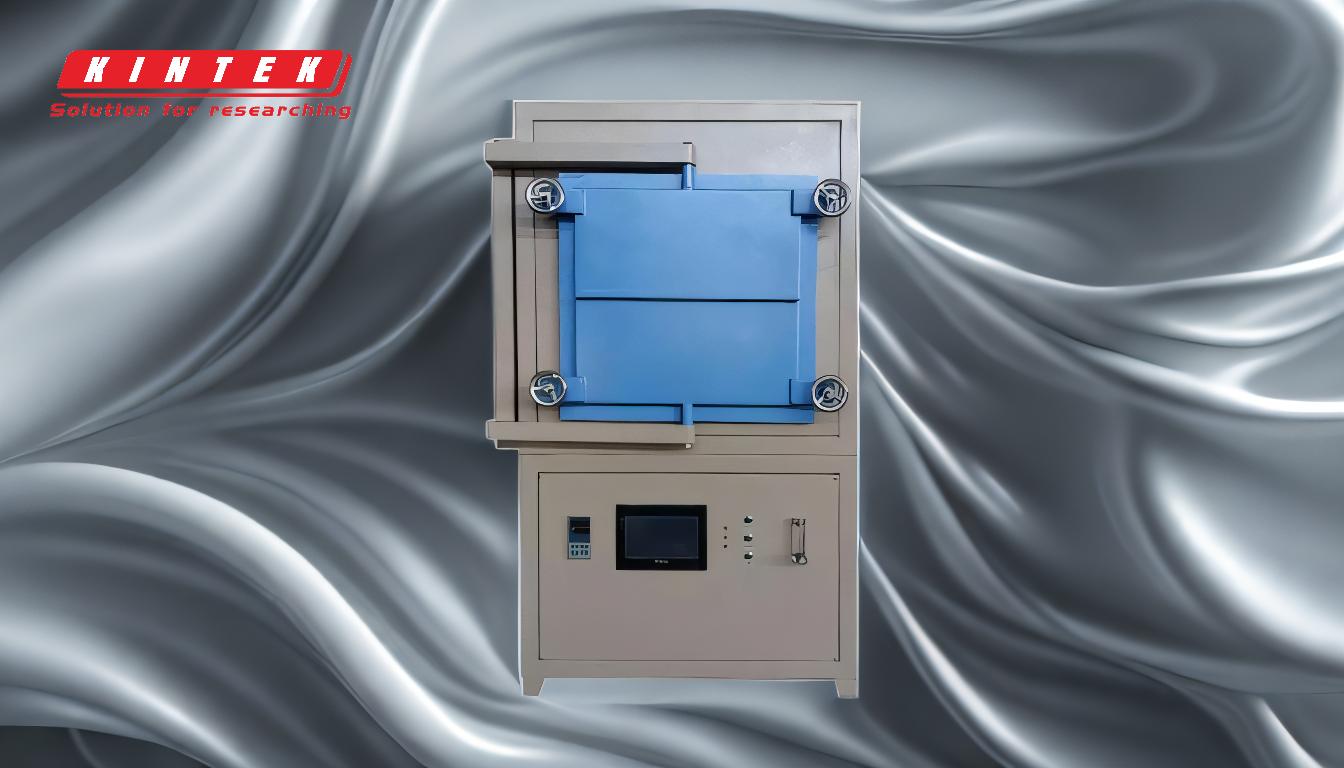
-
Definition of Inert Atmosphere in Welding:
- An inert atmosphere refers to a controlled environment filled with non-reactive gases, such as argon or helium, to protect the welding process from contamination.
- It prevents unwanted chemical reactions, such as oxidation or porosity, which can compromise the quality of the weld.
-
Purpose of Using Inert Gases:
- Shielding the Weld Pool: Inert gases shield the molten metal from reactive gases like oxygen and nitrogen in the air, which can cause defects such as porosity or brittleness in the weld.
- Protecting the Tungsten Electrode: In processes like gas tungsten arc welding (GTAW), inert gases protect the tungsten electrode from contamination, ensuring a stable arc and consistent weld quality.
- Maintaining Material Integrity: The inert atmosphere ensures that the materials being welded retain their desired properties, such as strength and corrosion resistance, by preventing oxidation or decarburization.
-
Common Inert Gases Used in Welding:
- Argon: Widely used due to its high density, which provides excellent coverage and protection for the weld pool. It is also cost-effective and readily available.
- Helium: Often used for welding thicker materials or in applications requiring higher heat input, as it produces a hotter arc compared to argon.
- Nitrogen: Occasionally used in specific applications, but it is less common due to its potential to react with certain materials at high temperatures.
-
Applications of Inert Atmosphere in Welding:
- Gas Tungsten Arc Welding (GTAW): Inert gases are essential for shielding the tungsten electrode and the weld pool, ensuring a clean and precise weld.
- Vacuum Brazing: Inert gases help flush out residual air from capillary paths, ensuring a strong bond between the brazed materials.
- Heat Treatment: Inert atmospheres are used in heat-treating applications to prevent oxidation and contamination, maintaining the material's properties during high-temperature processes.
-
Benefits of Using an Inert Atmosphere:
- Improved Weld Quality: Prevents defects like porosity, oxidation, and contamination, resulting in stronger and more durable welds.
- Enhanced Process Control: Provides a stable and predictable environment for welding, reducing variability and improving consistency.
- Material Preservation: Protects sensitive materials from chemical reactions, ensuring they retain their desired mechanical and chemical properties.
-
Equipment and Setup for Inert Atmosphere Welding:
- Inert Gas Supply: A reliable source of inert gas, such as argon or helium, is required to maintain the protective atmosphere.
- Gas Delivery System: Includes hoses, regulators, and nozzles to deliver the inert gas precisely to the weld area.
- Welding Torch: Designed to direct the inert gas flow around the weld pool and electrode, ensuring effective shielding.
- Monitoring and Control Systems: Advanced systems, such as microprocessor-based controls, ensure optimal gas flow and temperature for consistent results.
-
Challenges and Considerations:
- Cost of Inert Gases: High-purity inert gases can be expensive, especially for large-scale or high-volume welding operations.
- Gas Flow Management: Proper control of gas flow is critical to avoid turbulence, which can introduce air into the weld area and compromise the inert atmosphere.
- Material Compatibility: Not all materials are compatible with every inert gas. For example, nitrogen may react with certain metals at high temperatures, making it unsuitable for some applications.
-
Future Trends in Inert Atmosphere Welding:
- Advanced Gas Mixtures: The development of customized gas mixtures tailored to specific materials and welding processes is becoming more common.
- Automation and Robotics: Increasing use of automated welding systems with integrated inert gas delivery for improved precision and efficiency.
- Sustainability: Efforts to reduce gas consumption and waste through better process control and recycling systems.
By understanding the role of inert atmospheres in welding, manufacturers and welders can make informed decisions to optimize their processes, improve weld quality, and reduce costs. The use of inert gases is a critical factor in achieving high-performance welds in industries ranging from aerospace to automotive and beyond.
Summary Table:
Aspect | Details |
---|---|
Definition | A controlled environment using non-reactive gases to prevent contamination. |
Common Gases | Argon, Helium, Nitrogen (less common). |
Applications | GTAW, Vacuum Brazing, Heat Treatment. |
Benefits | Improved weld quality, enhanced process control, material preservation. |
Challenges | Cost of inert gases, gas flow management, material compatibility. |
Future Trends | Advanced gas mixtures, automation, sustainability. |
Optimize your welding process with inert gases—contact our experts today for tailored solutions!