Isostatic pressing, also known as cold isostatic pressing or isopressing, is a manufacturing technique used to compact powdered materials into a desired shape by applying uniform hydrostatic pressure from all directions. This process involves placing the powder in a flexible elastomeric mold, which is then submerged in a pressurized liquid. The pressure is transmitted uniformly through the mold walls, ensuring consistent compaction and density throughout the material. This method is particularly advantageous for producing complex shapes, achieving uniform density, and handling difficult-to-compact materials like superalloys and titanium. Key benefits include minimal internal stresses, low distortion during firing, and the ability to create parts with high length-to-diameter ratios or intricate internal features.
Key Points Explained:
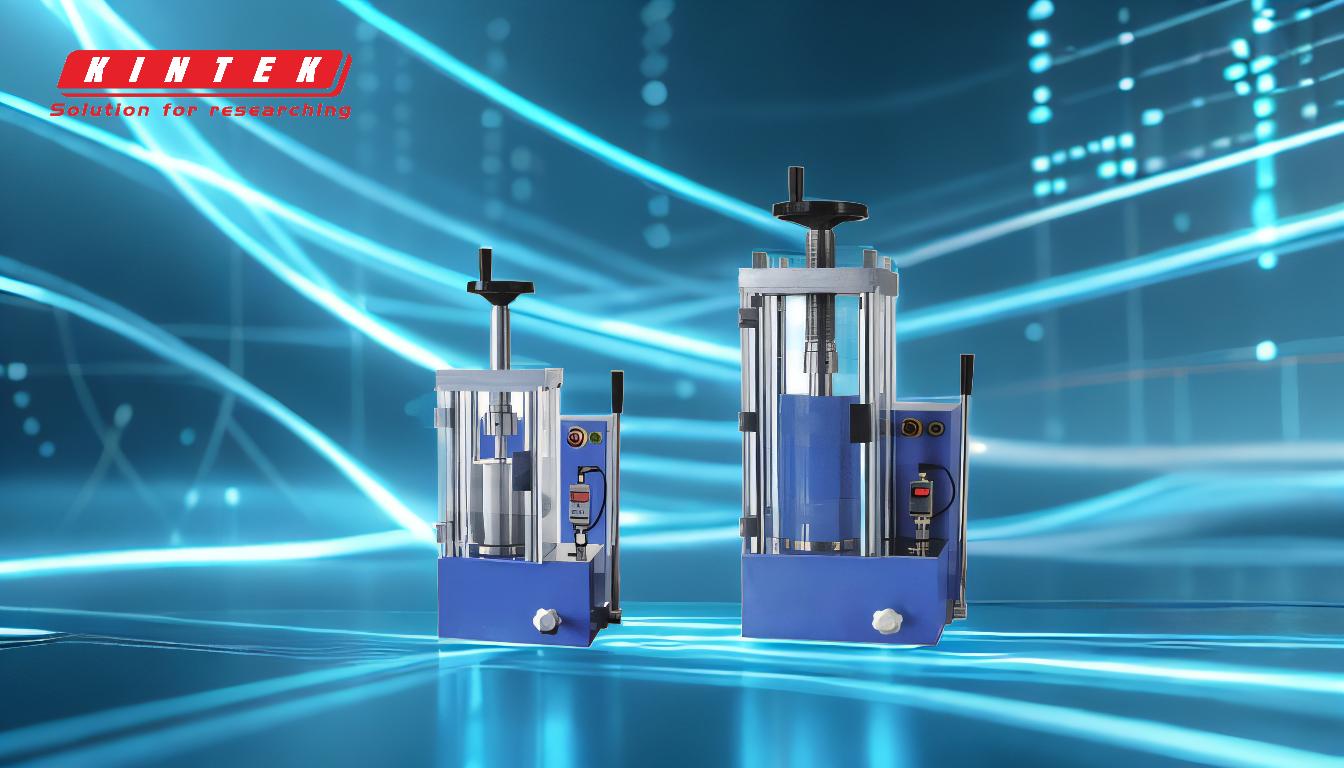
-
Definition and Process of Isostatic Pressing:
- Isostatic pressing involves compacting dry or semi-dry powder in a flexible elastomeric mold submerged in a pressurized liquid.
- A uniform hydrostatic pressure is applied to the powder through the flexible mold, ensuring even compaction.
- This process is also known as cold isostatic pressing or isopressing.
-
Key Variables in Isostatic Pressing:
- The process optimizes three critical variables: time, temperature, and pressure during the isostatic pressing (ISP) cycle.
- These variables influence the uniformity and density of the final compacted product.
-
Advantages of Isostatic Pressing:
- Uniform Density and Strength: Pressure is applied uniformly from all directions, eliminating wall friction and resulting in consistent density and grain structure.
- Shape Flexibility: The method allows for the creation of complex shapes, including internal features like threads, tapers, and thin-walled parts.
- High Length-to-Diameter Ratios: Parts with extreme aspect ratios (e.g., > 200) can be produced.
- Low Distortion and Consistent Shrinkage: Parts exhibit minimal distortion and consistent shrinkage during firing.
- Efficient Material Utilization: Ideal for expensive or difficult-to-compact materials like superalloys, titanium, and tool steels.
- No Need for Lubricants: The process eliminates the need for lubricants, reducing contamination risks.
- Low Tooling Costs: Particularly with the wet bag method, tooling costs are relatively low.
- Ability to Press Weak Powders: Even fragile or weak powders can be compacted effectively.
- Multi-Layer Compaction: Capable of pressing compacts with multiple layers of powders possessing different characteristics.
-
Applications and Material Suitability:
- Isostatic pressing is widely used in industries requiring high-performance materials, such as aerospace, medical, and automotive sectors.
- It is especially suitable for materials like superalloys, titanium, stainless steel, beryllium, and tool steels.
-
Comparison with Mechanical Pressing:
- Isostatic pressing achieves higher density for a given pressure compared to mechanical pressing.
- It removes constraints on part geometry, making it more versatile for complex designs.
-
Wet Bag vs. Dry Bag Methods:
- Wet Bag: The mold is submerged in the pressurized liquid, allowing for the production of very large parts.
- Dry Bag: The mold is fixed within the pressure vessel, suitable for smaller, high-volume production.
-
Environmental and Economic Benefits:
- The process reduces material waste and improves material utilization, making it cost-effective for expensive materials.
- It eliminates the need for drying before firing, saving time and energy.
By leveraging the principles of uniform pressure application and flexible mold design, isostatic pressing offers a robust solution for producing high-quality, complex components with minimal defects and high material efficiency.
Summary Table:
Key Aspect | Details |
---|---|
Process | Compacts powder in a flexible mold using uniform hydrostatic pressure. |
Key Variables | Time, temperature, and pressure optimize compaction and density. |
Advantages | Uniform density, complex shapes, low distortion, and no need for lubricants. |
Applications | Aerospace, medical, automotive industries; ideal for superalloys, titanium. |
Wet Bag vs. Dry Bag | Wet bag for large parts; dry bag for high-volume, smaller parts. |
Environmental Benefits | Reduces waste, improves material utilization, and saves energy. |
Learn how isostatic pressing can enhance your manufacturing process—contact our experts today!