Lamination is a manufacturing process that involves bonding multiple layers of materials together to create a composite material with enhanced properties such as strength, stability, sound insulation, and appearance. This technique is widely used in various industries, including electronics, construction, and packaging, to improve the functionality and durability of products. By combining different materials, lamination allows for the creation of products that leverage the unique properties of each layer, resulting in a final product that is more robust and versatile than its individual components.
Key Points Explained:
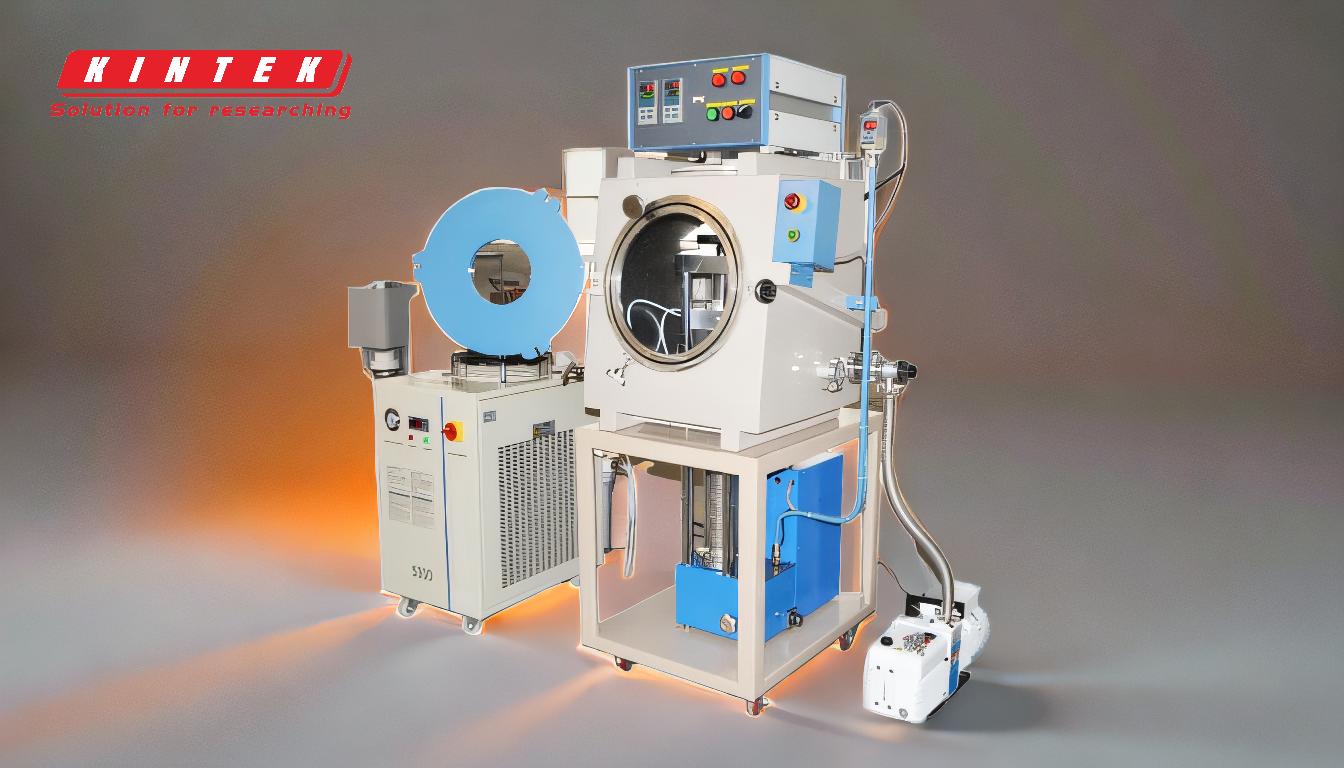
-
Definition of Lamination:
- Lamination is the process of manufacturing a material by bonding multiple layers together. This technique is used to create composite materials that have improved properties compared to single-layer materials.
-
Purpose of Lamination:
- Enhanced Strength: By combining layers of different materials, lamination can significantly increase the strength and durability of the final product.
- Improved Stability: Laminated materials are often more stable and resistant to environmental factors such as moisture, temperature changes, and mechanical stress.
- Sound Insulation: Lamination can be used to create materials that provide better sound insulation, making them ideal for use in construction and automotive industries.
- Aesthetic Appeal: Lamination can enhance the appearance of a material, providing a smooth, polished finish that is both attractive and functional.
-
Materials Used in Lamination:
- Plastics: Commonly used in lamination due to their versatility, durability, and ease of bonding with other materials.
- Electronic Components: Lamination is used in the production of electronic components such as Multi-Layer Ceramic Capacitors (MLCCs), hybrid chips, and ceramics, where it helps in creating compact, high-performance devices.
- Other Materials: Lamination can also involve materials like wood, metal, and paper, depending on the desired properties of the final product.
-
Applications of Lamination:
- Electronics: Lamination is crucial in the manufacturing of electronic components, where it helps in creating multi-layer structures that enhance performance and reliability.
- Construction: In the construction industry, laminated materials are used for flooring, countertops, and wall panels, providing both aesthetic and functional benefits.
- Packaging: Lamination is widely used in the packaging industry to create durable, moisture-resistant, and visually appealing packaging materials.
-
Lamination Process:
- Layer Preparation: The first step involves preparing the individual layers of material that will be bonded together. This may include cutting, shaping, and treating the materials to ensure proper adhesion.
- Bonding: The layers are then bonded together using adhesives, heat, pressure, or a combination of these methods. The choice of bonding technique depends on the materials being used and the desired properties of the final product.
- Finishing: After bonding, the laminated material may undergo additional processing steps such as trimming, polishing, or coating to achieve the desired finish and properties.
-
Advantages of Lamination:
- Customizability: Lamination allows for the customization of material properties by selecting specific layers and bonding techniques.
- Cost-Effectiveness: By combining different materials, lamination can create high-performance products at a lower cost compared to using a single, high-performance material.
- Versatility: Lamination can be applied to a wide range of materials and products, making it a versatile manufacturing technique.
-
Challenges in Lamination:
- Adhesion Issues: Ensuring proper adhesion between layers can be challenging, especially when bonding dissimilar materials.
- Environmental Impact: The use of adhesives and other chemicals in the lamination process can have environmental implications, requiring careful consideration of sustainability practices.
- Quality Control: Maintaining consistent quality in laminated products requires precise control over the lamination process, including temperature, pressure, and bonding time.
In summary, lamination is a versatile and widely used manufacturing process that enhances the properties of materials by combining multiple layers. Its applications span across various industries, offering benefits such as increased strength, stability, and aesthetic appeal. However, it also presents challenges that require careful management to ensure high-quality, sustainable products.
Summary Table:
Aspect | Details |
---|---|
Definition | Bonding multiple layers to create composite materials with enhanced properties. |
Purpose | Enhanced strength, improved stability, sound insulation, and aesthetic appeal. |
Materials Used | Plastics, electronic components, wood, metal, and paper. |
Applications | Electronics, construction, and packaging. |
Process | Layer preparation, bonding (adhesives, heat, pressure), and finishing. |
Advantages | Customizability, cost-effectiveness, and versatility. |
Challenges | Adhesion issues, environmental impact, and quality control. |
Learn how lamination can transform your products—contact us today for expert advice!