The maximum service temperature for brazing depends on several factors, including the type of filler metal used, the base materials being joined, and the specific application requirements. Generally, brazing temperatures range from 450°C to 1200°C, but the service temperature of the brazed joint after the process is typically lower. For high-temperature applications, specialized filler metals like nickel-based or gold-based alloys can be used, which can withstand temperatures up to 1000°C or higher. However, the base material's thermal stability and the joint design also play a critical role in determining the maximum service temperature. Proper selection of filler metals and brazing parameters ensures the joint's integrity and performance under high-temperature conditions.
Key Points Explained:
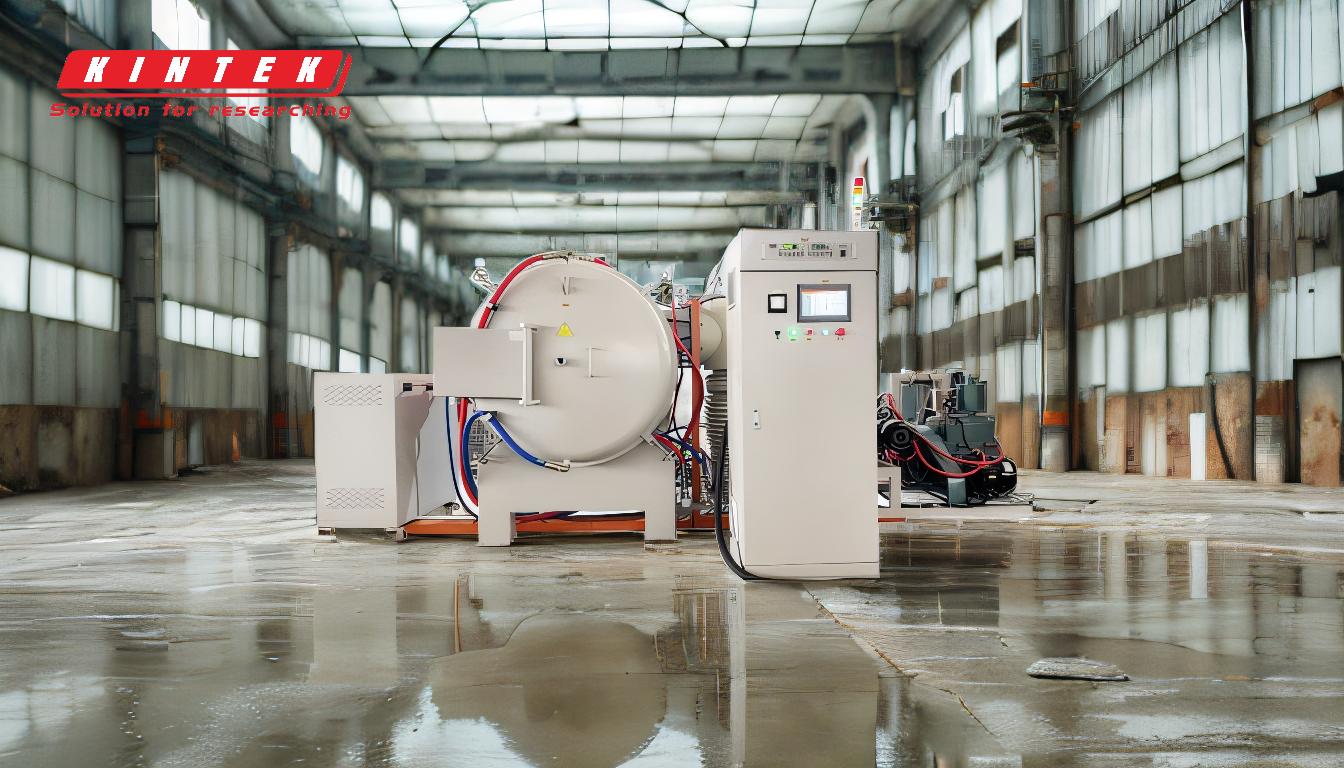
-
Brazing Temperature Range:
- Brazing typically occurs at temperatures between 450°C and 1200°C, depending on the filler metal and base materials.
- The brazing temperature is chosen to melt the filler metal without melting the base materials, ensuring a strong bond.
-
Service Temperature vs. Brazing Temperature:
- The service temperature of a brazed joint is the maximum temperature it can withstand during operation, which is usually lower than the brazing temperature.
- For example, a joint brazed at 800°C might have a service temperature of only 600°C due to material limitations.
-
Filler Metal Selection:
- The choice of filler metal significantly impacts the maximum service temperature. Common filler metals include:
- Silver-based alloys: Suitable for lower-temperature applications, typically up to 400°C.
- Copper-based alloys: Used for medium-temperature applications, up to 600°C.
- Nickel-based alloys: Ideal for high-temperature applications, capable of withstanding temperatures up to 1000°C or higher.
- Gold-based alloys: Used in specialized applications requiring high thermal and chemical stability.
- The choice of filler metal significantly impacts the maximum service temperature. Common filler metals include:
-
Base Material Considerations:
- The thermal stability of the base materials limits the maximum service temperature. For instance, aluminum alloys have lower thermal stability compared to stainless steel or nickel-based superalloys.
- The joint design must account for thermal expansion differences between the base materials and the filler metal to prevent cracking or failure at high temperatures.
-
Application-Specific Requirements:
- In aerospace or power generation industries, brazed joints may need to withstand extreme temperatures and stresses. Specialized alloys and advanced brazing techniques are employed to meet these demands.
- For example, nickel-based filler metals are often used in gas turbine components due to their high-temperature strength and oxidation resistance.
-
Factors Affecting Maximum Service Temperature:
- Oxidation resistance: Filler metals with high oxidation resistance can maintain joint integrity at elevated temperatures.
- Creep resistance: The ability of the joint to resist deformation under prolonged exposure to high temperatures.
- Thermal cycling: Repeated heating and cooling can affect the joint's performance, so materials must be chosen to withstand such conditions.
-
Testing and Validation:
- Brazed joints intended for high-temperature service are often subjected to rigorous testing, including thermal cycling, tensile strength tests, and metallurgical analysis, to ensure they meet performance requirements.
By carefully selecting the appropriate filler metal, base materials, and brazing parameters, it is possible to create brazed joints that perform reliably at high temperatures, even in demanding applications.
Summary Table:
Factor | Details |
---|---|
Brazing Temperature | 450°C to 1200°C, depending on filler metal and base materials |
Service Temperature | Typically lower than brazing temperature (e.g., 600°C for 800°C brazing) |
Filler Metals | Silver-based (up to 400°C), Copper-based (up to 600°C), Nickel-based (1000°C+), Gold-based (specialized) |
Base Materials | Thermal stability varies (e.g., aluminum alloys vs. stainless steel) |
Application Needs | Aerospace, power generation, and other high-temperature environments |
Key Considerations | Oxidation resistance, creep resistance, thermal cycling, and joint design |
Need help selecting the right brazing solution for your high-temperature application? Contact our experts today!