Isostatic pressing is a manufacturing process that applies uniform pressure from all directions to compact powders or materials into a desired shape. Specifically, cold isostatic pressing (CIP) is performed at ambient temperatures and is widely used for materials that require uniform density and minimal defects. This method is particularly beneficial for large or complex parts, as it ensures even compaction without the need for high precision in the sintered state. CIP is utilized across various industries, including aerospace, automotive, medical, and energy storage, for producing advanced ceramics, metal components, and other high-performance materials. The process involves placing powder in a flexible mold, which is then pressurized using a liquid medium, typically an oil-water mixture, to achieve compaction.
Key Points Explained:
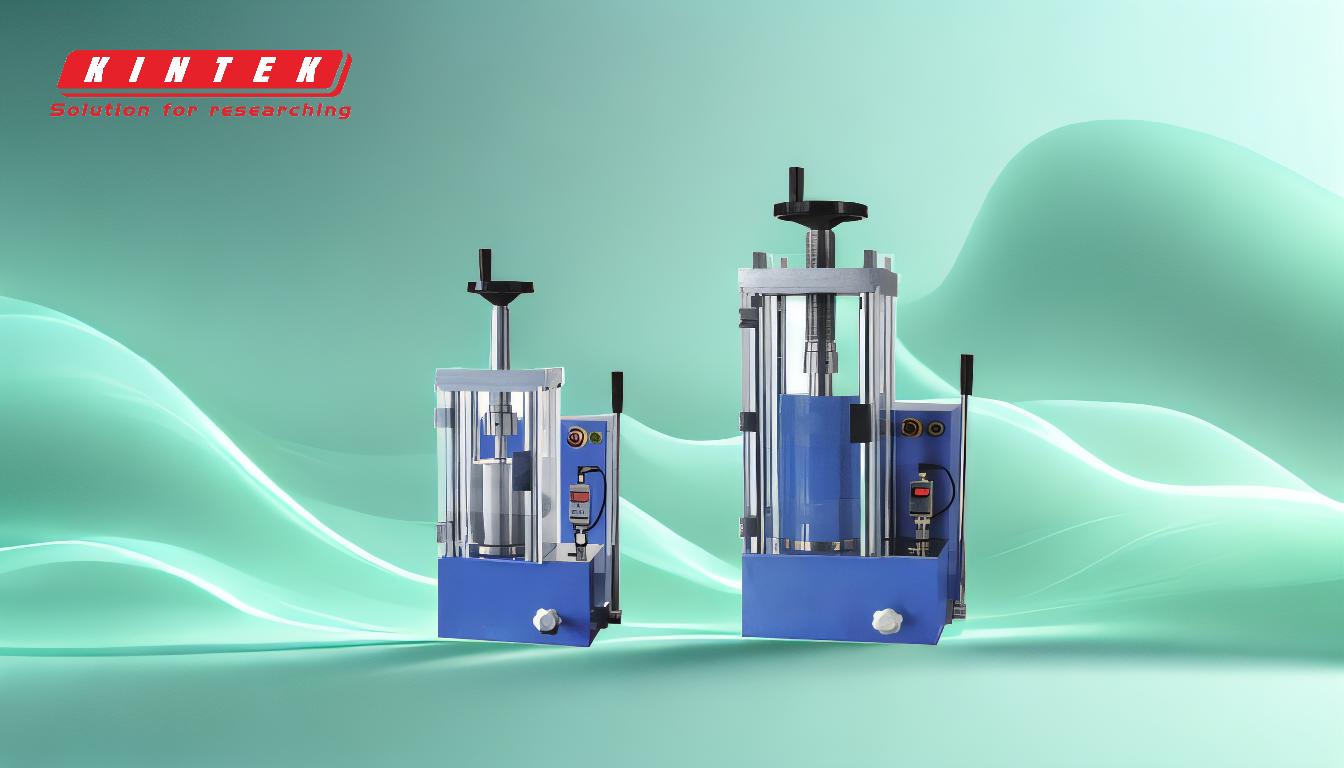
-
Definition of Isostatic Pressing:
- Isostatic pressing is a technique that uses uniform hydrostatic pressure to compact materials from all directions. This ensures even density and minimizes defects in the final product.
- It is particularly useful for materials that are difficult to shape using traditional methods, such as ceramics, metals, and composites.
-
Cold Isostatic Pressing (CIP):
- CIP is a subtype of isostatic pressing performed at ambient temperatures. It is ideal for materials that cannot withstand high temperatures during compaction.
- The process involves placing powder in a flexible rubber or plastic mold, which is then pressurized using a liquid medium, such as an oil-water mixture. The pressure can reach up to 100,000 psi, ensuring uniform compaction.
-
Applications of CIP:
- CIP is widely used in industries such as aerospace, automotive, medical, and energy storage. For example, it is used to manufacture advanced ceramics for aerospace components, high-performance parts for the oil and gas industry, and medical devices.
- It is also applied in energy storage technologies, including the production of lithium-ion batteries and fuel cells.
-
Advantages of CIP:
- CIP allows for the production of large or complex parts that cannot be easily pressed using uniaxial methods.
- It ensures uniform density and minimal defects, making it suitable for high-performance applications.
- The process is versatile and can be used with a wide range of materials, including ceramics, metals, composites, and plastics.
-
Process Details:
- In CIP, the powder material is placed in a flexible mold and then into a processing chamber. A liquid medium is pumped in and pressurized uniformly on all sides.
- The flexible mold ensures that the pressure is evenly distributed, resulting in a compacted product with uniform density.
-
Industry-Specific Uses:
- CIP is commonly used for the consolidation of ceramic powders, graphite, refractories, and electrical insulators.
- It is also employed in the production of fine ceramics for dental and medical applications, where precision and uniformity are critical.
-
Research and Development:
- Laboratory or developmental CIP services are often used to study process parameters or produce powder samples for research purposes. This helps in optimizing the process for specific materials and applications.
-
Equipment:
- The cold isostatic pressing machine is a key piece of equipment in this process. It is designed to handle the high pressures required for uniform compaction and is essential for achieving the desired material properties.
By understanding the principles and applications of isostatic pressing, particularly CIP, manufacturers can leverage this technology to produce high-quality components for a wide range of industries. The versatility and uniformity of the process make it an invaluable tool in modern manufacturing.
Summary Table:
Aspect | Details |
---|---|
Definition | A process using uniform hydrostatic pressure to compact materials from all directions. |
Cold Isostatic Pressing (CIP) | Performed at ambient temperatures, ideal for materials requiring uniform density and minimal defects. |
Applications | Aerospace, automotive, medical, energy storage, and more. |
Advantages | Produces large/complex parts, ensures uniform density, and works with various materials. |
Process | Powder in a flexible mold is pressurized using a liquid medium (e.g., oil-water mixture). |
Industries | Aerospace components, medical devices, lithium-ion batteries, and ceramics. |
Equipment | Cold isostatic pressing machines handle high pressures for uniform compaction. |
Discover how isostatic pressing can enhance your manufacturing process—contact us today for expert guidance!