Physical vapor deposition (PVD) is a sophisticated thin-film deposition technique used to create coatings on various substrates. It involves the physical transformation of a solid or liquid material into a vapor phase, which then condenses onto a substrate to form a thin film. This process occurs under vacuum or low-pressure conditions, often with the aid of plasma activation. PVD is widely used in industries such as electronics, optics, and manufacturing to enhance the properties of materials, including hardness, durability, and resistance to corrosion and oxidation. The process is atomistic, meaning it operates at the atomic or molecular level, ensuring precise control over film thickness and composition.
Key Points Explained:
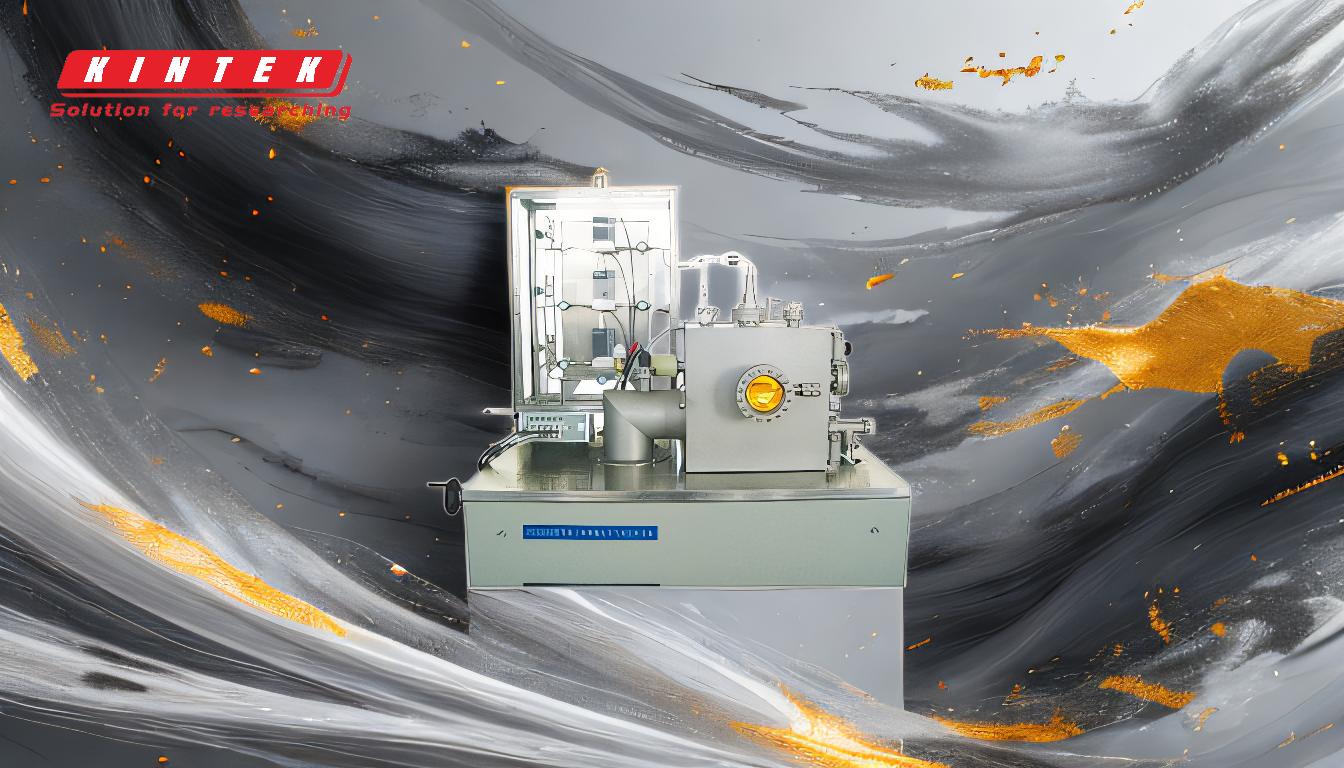
-
Definition of Physical Vapor Deposition (PVD):
- PVD is a thin-film deposition process that involves the physical transformation of a material from a solid or liquid state into a vapor phase.
- The vaporized material is then transferred through a low-pressure or vacuum environment and condenses onto a substrate to form a thin film.
- This process is atomistic, meaning it operates at the atomic or molecular level, allowing for precise control over the film's properties.
-
Key Components of the PVD Process:
- Source Material: The material to be deposited (target) is typically in solid or liquid form. Common materials include metals, ceramics, and alloys.
- Vaporization: The source material is vaporized using physical methods such as evaporation, sputtering, or arc vaporization. This converts the material into a gaseous state.
- Transport: The vaporized atoms or molecules travel through a low-pressure or vacuum environment to the substrate.
- Condensation: The vapor condenses onto the substrate surface, forming a thin film through nucleation and growth processes.
-
Types of PVD Techniques:
- Evaporation: The source material is heated until it evaporates, and the vapor is then deposited onto the substrate. This method is commonly used for metals and simple compounds.
- Sputtering: High-energy ions bombard the target material, dislodging atoms or molecules that are then deposited onto the substrate. This technique is versatile and can be used for a wide range of materials.
- Arc Vaporization: An electric arc is used to vaporize the target material, creating a plasma that deposits onto the substrate. This method is particularly effective for hard coatings.
-
Applications of PVD:
- Electronics: PVD is used to deposit thin films in semiconductor devices, solar panels, and displays.
- Optics: It is employed to create anti-reflective, reflective, and protective coatings on lenses and mirrors.
- Manufacturing: PVD coatings enhance the hardness, wear resistance, and corrosion resistance of tools, molds, and mechanical components.
- Decorative Coatings: PVD is used to apply durable and aesthetically pleasing coatings on jewelry, watches, and consumer electronics.
-
Advantages of PVD:
- Precision: PVD allows for precise control over film thickness and composition, making it ideal for applications requiring high accuracy.
- Durability: PVD coatings are highly durable, offering excellent resistance to wear, corrosion, and oxidation.
- Versatility: The process can be used with a wide range of materials, including metals, ceramics, and alloys.
- Environmental Friendliness: PVD is a clean process that produces minimal waste and does not involve harmful chemicals.
-
Challenges and Considerations:
- Cost: PVD equipment and processes can be expensive, particularly for large-scale applications.
- Complexity: The process requires precise control of parameters such as temperature, pressure, and deposition rate.
- Substrate Compatibility: Not all materials are suitable for PVD, and the process may require additional surface preparation to ensure proper adhesion.
In summary, physical vapor deposition is a highly versatile and precise method for depositing thin films with enhanced properties. Its applications span across various industries, offering solutions for improving material performance and durability. Despite its challenges, PVD remains a critical technology in modern manufacturing and materials science.
Summary Table:
Aspect | Details |
---|---|
Definition | Thin-film deposition process involving vaporization and condensation. |
Key Components | Source material, vaporization, transport, condensation. |
Techniques | Evaporation, sputtering, arc vaporization. |
Applications | Electronics, optics, manufacturing, decorative coatings. |
Advantages | Precision, durability, versatility, environmental friendliness. |
Challenges | Cost, complexity, substrate compatibility. |
Ready to explore how PVD can enhance your materials? Contact our experts today for tailored solutions!