Sintering is a manufacturing process that transforms powdery or granular materials into a solid, dense mass by applying heat and pressure, typically below the material's melting point. This process allows particles to bond at the atomic level, creating a cohesive structure without liquefying the material. Commonly used in industries like powder metallurgy, ceramics, and plastics, sintering enhances material properties such as strength, durability, and density. The term originates from the German word "sinter," meaning cinder, and has been used since the 18th century. It is a versatile technique for producing complex shapes and high-performance materials, making it essential in modern manufacturing.
Key Points Explained:
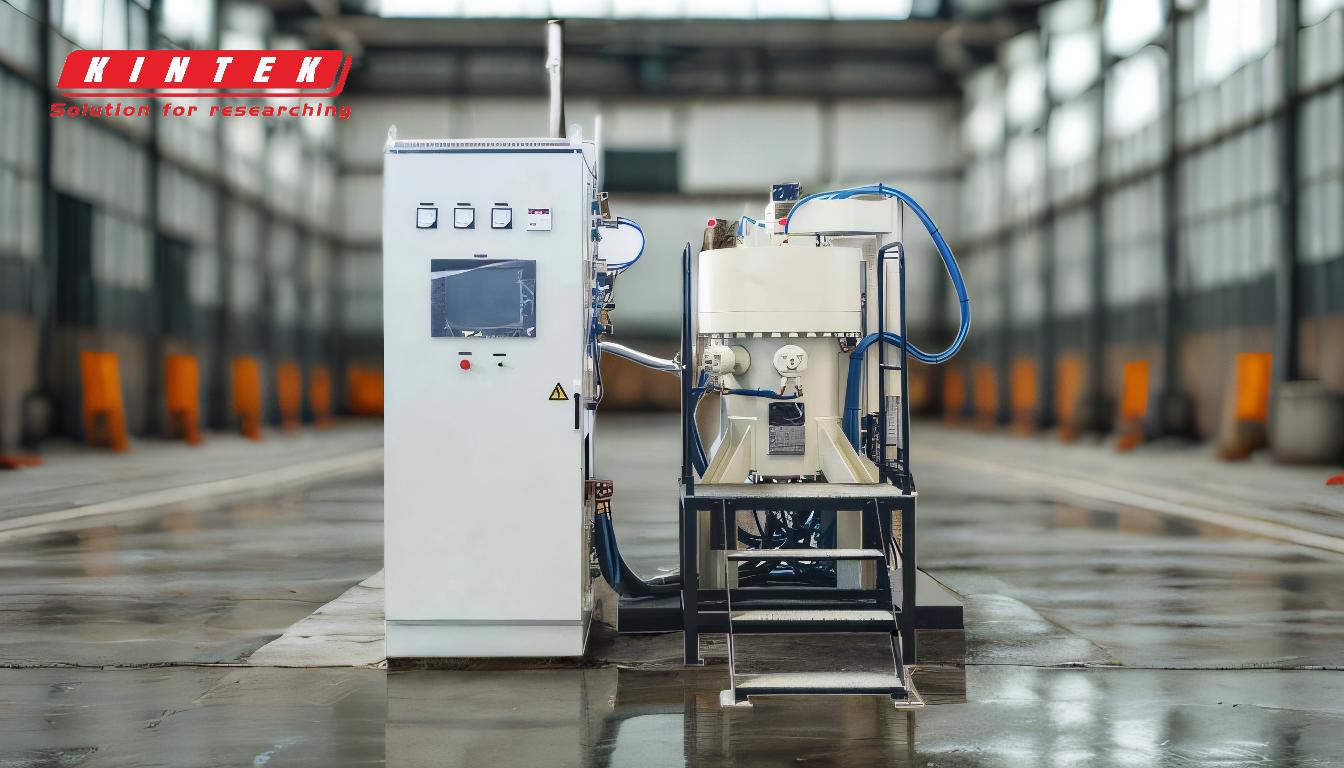
-
Definition of Sintering:
- Sintering is a process that combines small particles into a solid mass without melting the material. It involves applying heat and pressure to bond adjacent particles, resulting in a dense and cohesive structure.
- This process is used for materials like metals, ceramics, plastics, and other powdery substances.
-
How Sintering Works:
- Heat and pressure are applied to the material at a temperature below its melting point.
- The atoms in the particles diffuse across their boundaries, fusing them together.
- This atomic diffusion creates strong bonds, transforming loose particles into a solid mass.
-
Applications of Sintering:
- Powder Metallurgy: Used to produce metal parts with complex shapes and high strength, such as gears, bearings, and automotive components.
- Ceramics: Sintering is essential in creating durable ceramic products like tiles, insulators, and advanced materials for electronics.
- Plastics: Used to create porous or structured plastic components.
- High-Melting-Point Materials: Ideal for materials like tungsten and molybdenum, which are difficult to process using traditional melting methods.
-
Benefits of Sintering:
- Enhanced Material Properties: Sintered materials often exhibit improved strength, hardness, and durability.
- Cost-Effectiveness: The process minimizes material waste and allows for the production of complex shapes without extensive machining.
- Versatility: Applicable to a wide range of materials, including metals, ceramics, and plastics.
-
Historical and Linguistic Context:
- The term "sintered" originates from the German word "sinter," which means cinder. It entered the English language in the late 18th century.
- This historical context reflects the process's association with heat treatment and the transformation of loose materials into solid forms.
-
Key Characteristics of Sintered Materials:
- Density: Sintered materials are denser than their powdered counterparts due to the compression and bonding of particles.
- Porosity: Depending on the process parameters, sintered materials can have controlled porosity, which is useful in applications like filters or catalysts.
- Shape Retention: Sintering allows for the creation of precise and intricate shapes, making it ideal for manufacturing components with tight tolerances.
-
Comparison to Other Processes:
- Unlike melting, sintering does not liquefy the material, preserving its original properties while enhancing its structural integrity.
- It is distinct from processes like casting or forging, which involve melting or deforming materials at higher temperatures.
-
Industrial Importance:
- Sintering is a cornerstone of modern manufacturing, enabling the production of high-performance materials and components.
- It is widely used in industries such as automotive, aerospace, electronics, and construction due to its efficiency and versatility.
By understanding sintering, manufacturers and purchasers can make informed decisions about material selection and production methods, ensuring optimal performance and cost-effectiveness for their applications.
Summary Table:
Aspect | Details |
---|---|
Definition | Combines particles into a solid mass without melting, using heat and pressure. |
How It Works | Atoms diffuse across boundaries, bonding particles into a dense structure. |
Applications | Powder metallurgy, ceramics, plastics, and high-melting-point materials. |
Benefits | Enhanced strength, cost-effectiveness, and versatility. |
Key Characteristics | High density, controlled porosity, and precise shape retention. |
Industrial Importance | Essential in automotive, aerospace, electronics, and construction industries. |
Learn how sintering can optimize your manufacturing process—contact our experts today!