Physical Vapor Deposition (PVD) is a vacuum-based coating process used to deposit thin films of material onto a substrate. The process involves converting a solid material into a vapor phase through methods such as thermal evaporation, sputtering, or ion bombardment, and then condensing the vapor onto a substrate to form a thin, uniform layer. PVD is widely used in industries requiring durable, high-performance coatings, such as electronics, optics, and tool manufacturing. The process is characterized by its ability to produce coatings with excellent adhesion, high purity, and precise control over thickness, making it suitable for applications requiring corrosion resistance, wear resistance, or thermal stability.
Key Points Explained:
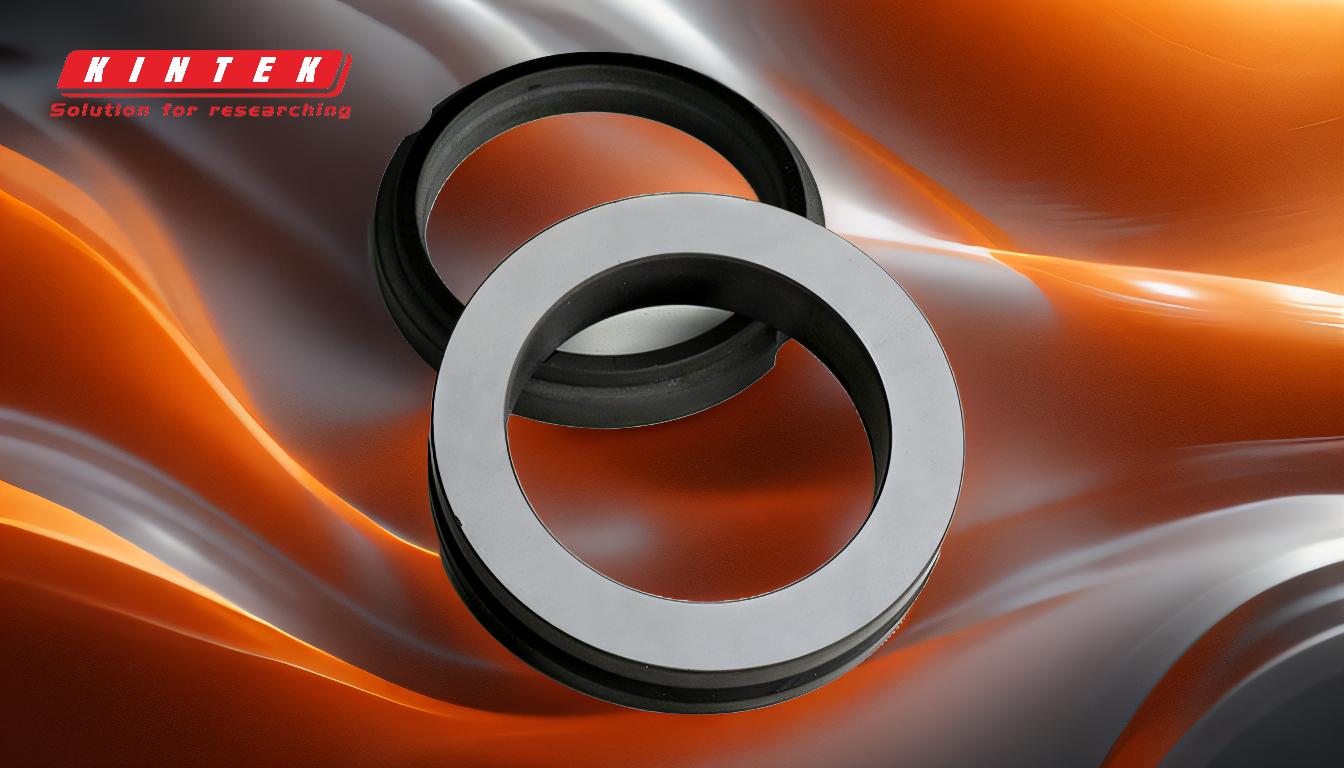
-
Vacuum Environment:
- PVD is conducted in a vacuum chamber to minimize contamination from background gases and ensure a clean deposition process.
- Lowering the pressure in the chamber reduces the likelihood of chemical reactions between the background gases and the deposited material, which could compromise the quality of the coating.
-
Vaporization of the Source Material:
- The solid precursor material (target) is converted into a vapor phase using one of several methods:
- Thermal Evaporation: The target material is heated until it evaporates. This can be achieved through resistance heating or electron beam heating.
- Sputtering: High-energy ions bombard the target material, knocking atoms off its surface and into the vapor phase.
- Ion Plating: Combines sputtering and evaporation, where the target material is vaporized and ionized before deposition.
- The solid precursor material (target) is converted into a vapor phase using one of several methods:
-
Transport of Vaporized Material:
- The vaporized atoms or molecules travel through the vacuum chamber toward the substrate.
- The vacuum environment ensures that the vaporized particles move in a straight line, allowing for precise control over the deposition process.
-
Condensation on the Substrate:
- The vaporized material condenses onto the substrate, forming a thin, uniform film.
- The adhesion of the film to the substrate is typically strong, resulting in durable coatings.
-
Control of Film Thickness and Rate:
- A quartz crystal rate monitor is often used to measure and control the rate of deposition and the thickness of the film.
- This ensures that the coating meets the desired specifications for the application.
-
Sub-Methods of PVD:
- Thermal Evaporation: Suitable for materials with lower melting points. The target material is heated until it evaporates, and the vapor condenses on the substrate.
- Sputtering: Ideal for materials with higher melting points. High-energy ions bombard the target, ejecting atoms that then deposit onto the substrate.
- Ion Plating: Combines evaporation and ionization to enhance adhesion and film density.
-
Applications and Benefits:
- PVD coatings are used in a wide range of industries, including electronics (for semiconductor devices), optics (for anti-reflective coatings), and manufacturing (for wear-resistant tools).
- The process produces coatings with excellent adhesion, high purity, and precise control over thickness, making it suitable for applications requiring durability, corrosion resistance, or thermal stability.
-
Advantages of PVD:
- High Adhesion: The coatings adhere strongly to the substrate, ensuring long-lasting performance.
- High Purity: The vacuum environment minimizes contamination, resulting in high-purity coatings.
- Precision: The process allows for precise control over film thickness and composition.
- Versatility: PVD can be used with a wide range of materials, including metals, ceramics, and composites.
-
Challenges and Considerations:
- Cost: PVD equipment and processes can be expensive, particularly for large-scale applications.
- Complexity: The process requires specialized equipment and expertise to achieve optimal results.
- Material Limitations: Some materials may not be suitable for certain PVD methods due to their physical properties (e.g., melting point, vapor pressure).
In summary, PVD is a versatile and precise method for depositing thin films with excellent properties. Its ability to produce high-quality coatings in a controlled environment makes it a valuable process for a wide range of industrial applications.
Summary Table:
Aspect | Details |
---|---|
Process | Converts solid material into vapor, then condenses onto a substrate to form a thin film. |
Key Methods | Thermal Evaporation, Sputtering, Ion Plating |
Applications | Electronics, Optics, Tool Manufacturing |
Advantages | High adhesion, high purity, precise thickness control, versatility |
Challenges | High cost, complexity, material limitations |
Discover how PVD can enhance your industrial applications—contact us today for expert guidance!