Hydraulic systems are essential in various industries, but they are prone to damage due to several factors. The most common cause of hydraulic system damage is contamination, which includes the presence of particles, water, air, and other foreign substances in the hydraulic fluid. Contamination can lead to wear and tear of components, reduced efficiency, and eventual system failure. Other causes include improper maintenance, overheating, and using incorrect or low-quality hydraulic fluids. Addressing these issues through regular maintenance, proper filtration, and using high-quality fluids can significantly extend the lifespan of hydraulic systems.
Key Points Explained:
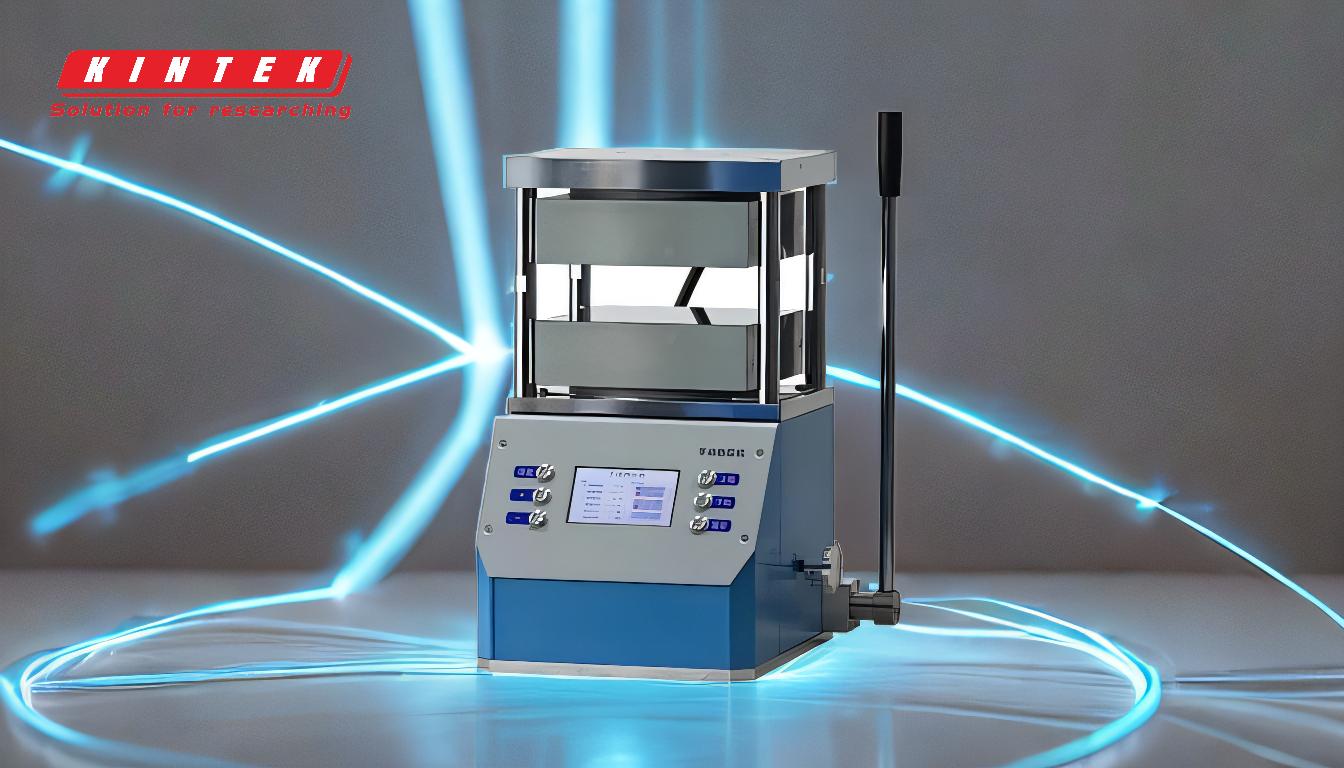
-
Contamination as the Primary Cause:
- Particles: Dirt, metal shavings, and other particulate matter can enter the hydraulic system through seals, breathers, or during maintenance. These particles can cause abrasion and wear on moving parts, leading to system failure.
- Water: Water contamination can lead to corrosion of metal components and degradation of the hydraulic fluid, reducing its lubricating properties and leading to increased wear.
- Air: Air entrapment in the hydraulic fluid can cause cavitation, which leads to pitting and erosion of components, reducing their lifespan.
-
Improper Maintenance:
- Neglecting Regular Checks: Failing to perform regular inspections and maintenance can allow small issues to escalate into major problems.
- Incorrect Procedures: Using improper maintenance techniques or tools can introduce contaminants or damage components.
-
Overheating:
- Excessive Heat: High temperatures can degrade hydraulic fluid, reducing its viscosity and lubricating properties. This can lead to increased friction and wear on system components.
- Inadequate Cooling: Insufficient cooling systems can cause the hydraulic fluid to overheat, leading to thermal breakdown and reduced system efficiency.
-
Use of Incorrect or Low-Quality Hydraulic Fluids:
- Incorrect Viscosity: Using hydraulic fluid with the wrong viscosity can lead to improper lubrication, increased wear, and potential system failure.
- Low-Quality Fluids: Inferior quality fluids may contain impurities or lack necessary additives, leading to reduced performance and increased wear.
-
Preventive Measures:
- Regular Maintenance: Implementing a routine maintenance schedule to check and replace hydraulic fluids, filters, and seals can prevent contamination and wear.
- Proper Filtration: Using high-quality filters and ensuring they are regularly replaced can significantly reduce the risk of contamination.
- Quality Fluids: Using high-quality hydraulic fluids that meet the system's specifications can enhance performance and extend the system's lifespan.
- Temperature Control: Ensuring adequate cooling and monitoring system temperatures can prevent overheating and fluid degradation.
By understanding these key points and implementing appropriate preventive measures, the risk of hydraulic system damage can be significantly reduced, ensuring reliable and efficient operation.
Summary Table:
Cause of Damage | Impact | Preventive Measures |
---|---|---|
Contamination | Particles, water, and air cause wear, corrosion, and cavitation. | Use high-quality filters, replace fluids regularly, and ensure proper system sealing. |
Improper Maintenance | Neglecting checks or using incorrect procedures leads to component damage. | Implement routine inspections and follow proper maintenance protocols. |
Overheating | High temperatures degrade fluid viscosity and increase friction. | Monitor system temperature and ensure adequate cooling systems are in place. |
Incorrect/Low-Quality Fluids | Wrong viscosity or impurities reduce performance and increase wear. | Use high-quality hydraulic fluids that meet system specifications. |
Protect your hydraulic systems from damage—contact our experts today for tailored solutions and advice!