The most common form of heat treatment is annealing, followed closely by quenching and tempering. Annealing is widely used because it softens metals, improves ductility, and reduces internal stresses, making it suitable for a variety of applications across industries. Quenching and tempering are often used together to achieve a balance of hardness and toughness in metals. These processes are fundamental in heat treatment due to their versatility and ability to modify material properties such as strength, hardness, and ductility. Other methods like case hardening and normalizing are also common but are typically applied for more specific purposes.
Key Points Explained:
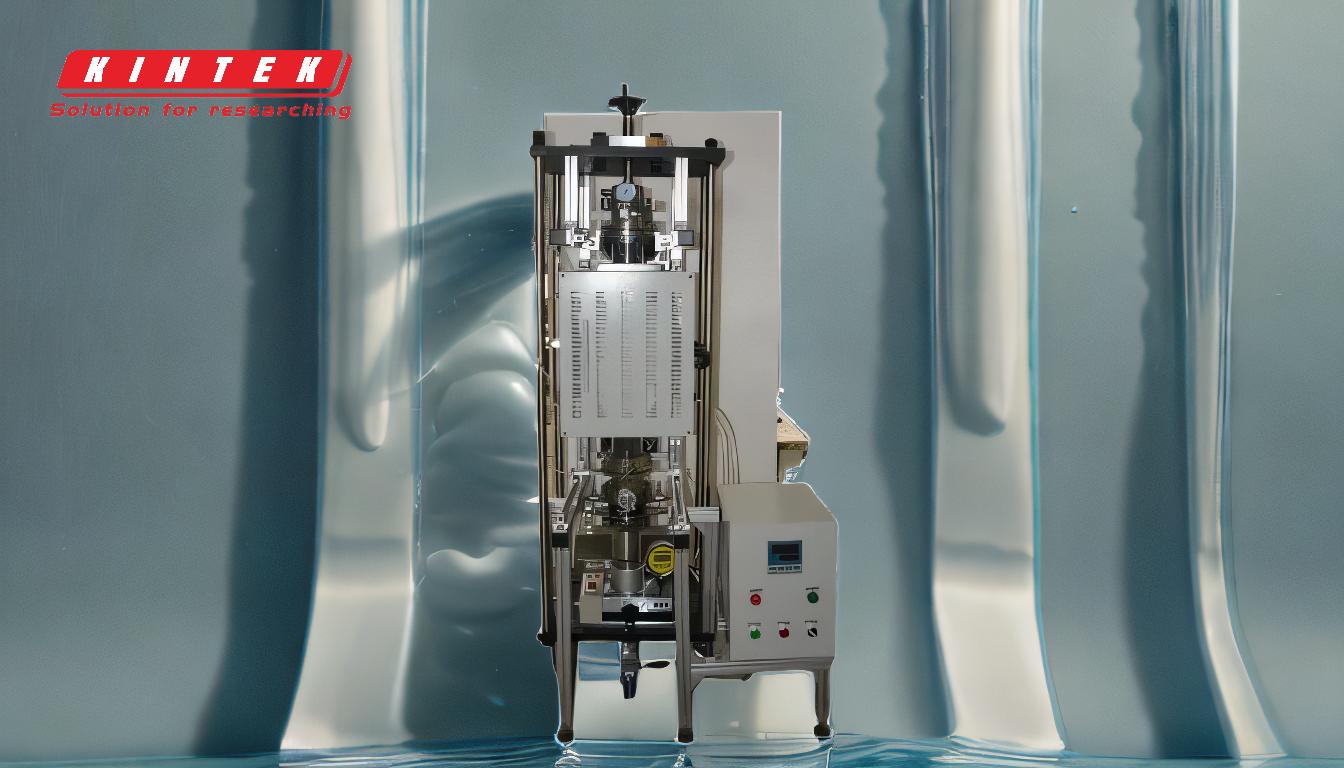
-
Annealing as the Most Common Heat Treatment
- Annealing is the most widely used heat treatment process because it addresses multiple material challenges simultaneously.
- It involves heating the metal to a specific temperature, holding it there for a period, and then slowly cooling it.
- This process softens the metal, improves ductility, and reduces internal stresses, making it easier to machine or form.
- Annealing is commonly applied to steels, aluminum, copper, and other metals in industries like automotive, construction, and manufacturing.
-
Quenching and Tempering
- Quenching involves rapidly cooling a heated metal (usually steel) by immersing it in water, oil, or another medium. This process increases hardness but can make the metal brittle.
- Tempering is often performed after quenching to reduce brittleness and improve toughness. It involves reheating the metal to a lower temperature and then cooling it.
- Together, quenching and tempering are essential for producing materials that require a balance of hardness and durability, such as tools, gears, and structural components.
-
Other Common Heat Treatment Methods
- Case Hardening: Used to create a hard outer surface while maintaining a softer, tougher core. This is ideal for components like gears and bearings.
- Normalizing: Similar to annealing but involves faster cooling. It refines grain structure and improves mechanical properties.
- Precipitation Hardening: Enhances strength in certain alloys, such as aluminum and stainless steel, by forming fine particles within the metal matrix.
-
Why Annealing is the Most Common
- Versatility: Annealing can be applied to a wide range of metals and alloys.
- Problem-Solving: It addresses issues like hardness, stress, and machinability in one process.
- Cost-Effectiveness: The process is relatively simple and does not require highly specialized equipment.
-
Applications of Common Heat Treatments
- Annealing: Used in manufacturing processes like cold working, welding, and casting to restore material properties.
- Quenching and Tempering: Applied in the production of tools, automotive parts, and structural steel.
- Case Hardening: Common in the aerospace and automotive industries for components requiring wear resistance.
-
Factors Influencing the Choice of Heat Treatment
- Material Type: Different metals and alloys respond differently to heat treatment processes.
- Desired Properties: The choice depends on whether the goal is to increase hardness, toughness, or ductility.
- Application Requirements: Components subjected to high stress or wear may require specific treatments like case hardening or tempering.
In conclusion, annealing is the most common heat treatment due to its versatility and effectiveness in improving material properties. However, quenching, tempering, and case hardening are also widely used, depending on the specific requirements of the material and its intended application.
Summary Table:
Heat Treatment | Key Benefits | Applications |
---|---|---|
Annealing | Softens metals, improves ductility, reduces stress | Automotive, construction, manufacturing |
Quenching | Increases hardness, often paired with tempering | Tools, gears, structural components |
Tempering | Reduces brittleness, improves toughness | Tools, automotive parts, structural steel |
Case Hardening | Creates a hard surface with a tough core | Gears, bearings, aerospace components |
Normalizing | Refines grain structure, improves properties | General manufacturing |
Precipitation Hardening | Enhances strength in alloys | Aluminum, stainless steel applications |
Need help choosing the right heat treatment for your materials? Contact our experts today for tailored solutions!