Physical Vapor Deposition (PVD) is a process used to create thin film coatings by transitioning solid materials into a vapor phase and then condensing them onto a substrate. This method involves placing the substrate and coating material in a vacuum chamber, where the coating material (target) is vaporized using techniques like sputtering, thermal evaporation, or electron beam evaporation. The vaporized material then travels through the chamber and deposits onto the substrate, forming a durable, high-quality thin film. PVD is known for its ability to produce coatings with excellent adhesion, high melting point tolerance, and resistance to corrosion and high temperatures. The process operates in a "line-of-sight" manner, meaning the vaporized atoms travel directly to the substrate, ensuring precise and controlled deposition.
Key Points Explained:
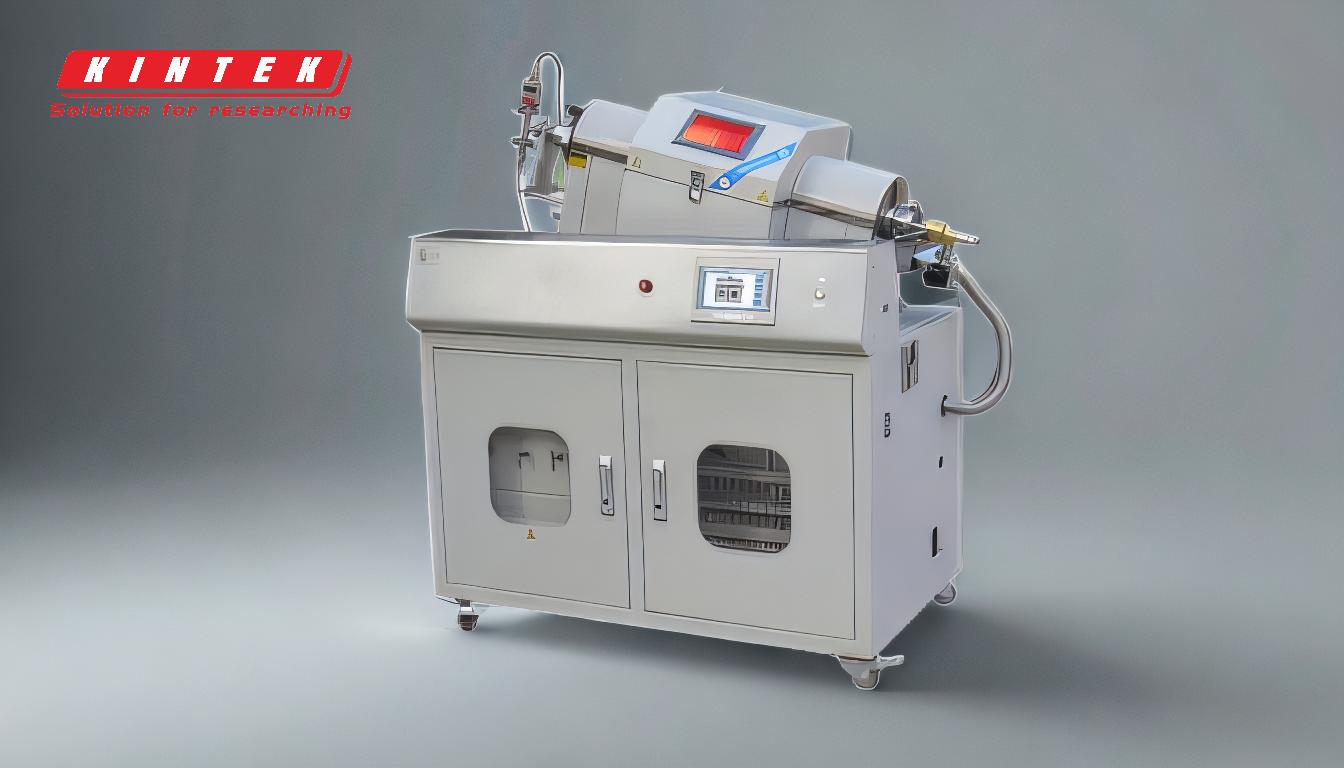
-
Definition of PVD
- Physical Vapor Deposition (PVD) is a coating process where solid materials are vaporized in a vacuum environment and then condensed onto a substrate to form a thin film.
- The process involves transitioning the material from a solid to a vapor phase and then back to a solid phase on the substrate.
-
Key Components of PVD
- Vacuum Chamber: The process takes place in a low-pressure environment to prevent contamination and ensure controlled deposition.
- Target Material: The solid material (e.g., metals, ceramics) that is vaporized to form the coating.
- Substrate: The object or surface onto which the vaporized material is deposited.
- Energy Source: Methods like sputtering, electron beam, laser beam, or arc discharge are used to vaporize the target material.
-
Stages of the PVD Process
- Vaporization: The target material is converted from a solid to a vapor phase using high-energy methods.
- Transport: The vaporized atoms travel through the vacuum chamber in a "line-of-sight" manner.
- Deposition: The vaporized atoms condense onto the substrate, forming a thin film.
-
Methods of PVD
- Sputtering: High-energy ions bombard the target material, ejecting atoms that then deposit onto the substrate.
- Thermal Evaporation: The target material is heated until it evaporates, and the vapor condenses onto the substrate.
- Electron Beam Evaporation: An electron beam is used to heat and vaporize the target material.
- Arc Discharge: An electric arc vaporizes the target material, which then deposits onto the substrate.
-
Advantages of PVD
- High-Quality Coatings: PVD produces thin films with excellent adhesion, uniformity, and durability.
- Material Versatility: It can handle materials with high melting points, such as titanium and ceramics.
- Corrosion and Temperature Resistance: PVD coatings are highly resistant to corrosion and can withstand high temperatures.
- Precision: The "line-of-sight" nature of PVD allows for precise control over the deposition process.
-
Applications of PVD
- Industrial Tools: PVD is used to coat cutting tools, molds, and dies to enhance their hardness and wear resistance.
- Electronics: It is employed in the production of semiconductors, solar panels, and optical coatings.
- Decorative Coatings: PVD is used to create durable, scratch-resistant finishes on jewelry, watches, and consumer electronics.
- Medical Devices: PVD coatings improve the biocompatibility and wear resistance of medical implants and instruments.
-
Challenges and Considerations
- Cost: PVD equipment and processes can be expensive due to the need for vacuum environments and high-energy sources.
- Complexity: The process requires precise control over parameters like temperature, pressure, and energy input.
- Substrate Limitations: The "line-of-sight" nature of PVD can make it difficult to coat complex geometries or internal surfaces.
-
Future Trends in PVD
- Nanotechnology: PVD is being used to create nanostructured coatings with unique properties, such as enhanced electrical conductivity or antibacterial effects.
- Hybrid Processes: Combining PVD with other techniques, like Chemical Vapor Deposition (CVD), to achieve multifunctional coatings.
- Sustainability: Developing more energy-efficient PVD processes and using environmentally friendly materials.
By understanding the theory and mechanics of PVD, equipment and consumable purchasers can make informed decisions about its application in various industries. The process's ability to produce high-performance coatings makes it a valuable tool for enhancing the durability and functionality of a wide range of products.
Summary Table:
Aspect | Details |
---|---|
Definition | Coating process where solid materials are vaporized and condensed on a substrate. |
Key Components | Vacuum chamber, target material, substrate, energy source. |
Process Stages | Vaporization, transport, deposition. |
Methods | Sputtering, thermal evaporation, electron beam evaporation, arc discharge. |
Advantages | High-quality coatings, material versatility, corrosion resistance, precision. |
Applications | Industrial tools, electronics, decorative coatings, medical devices. |
Challenges | High cost, process complexity, substrate limitations. |
Future Trends | Nanotechnology, hybrid processes, sustainability. |
Ready to enhance your products with PVD coatings? Contact us today to learn more!