A forging press operates on the principle of applying compressive force to shape or deform metal into desired forms. This process is typically achieved using hydraulic systems, which leverage fluid pressure to generate the necessary force. The key components of a hydraulic forging press work together to ensure precise control, safety, and efficiency during the forging process. Below, we will explore the principle of forging presses and the role of their key components in detail.
Key Points Explained:
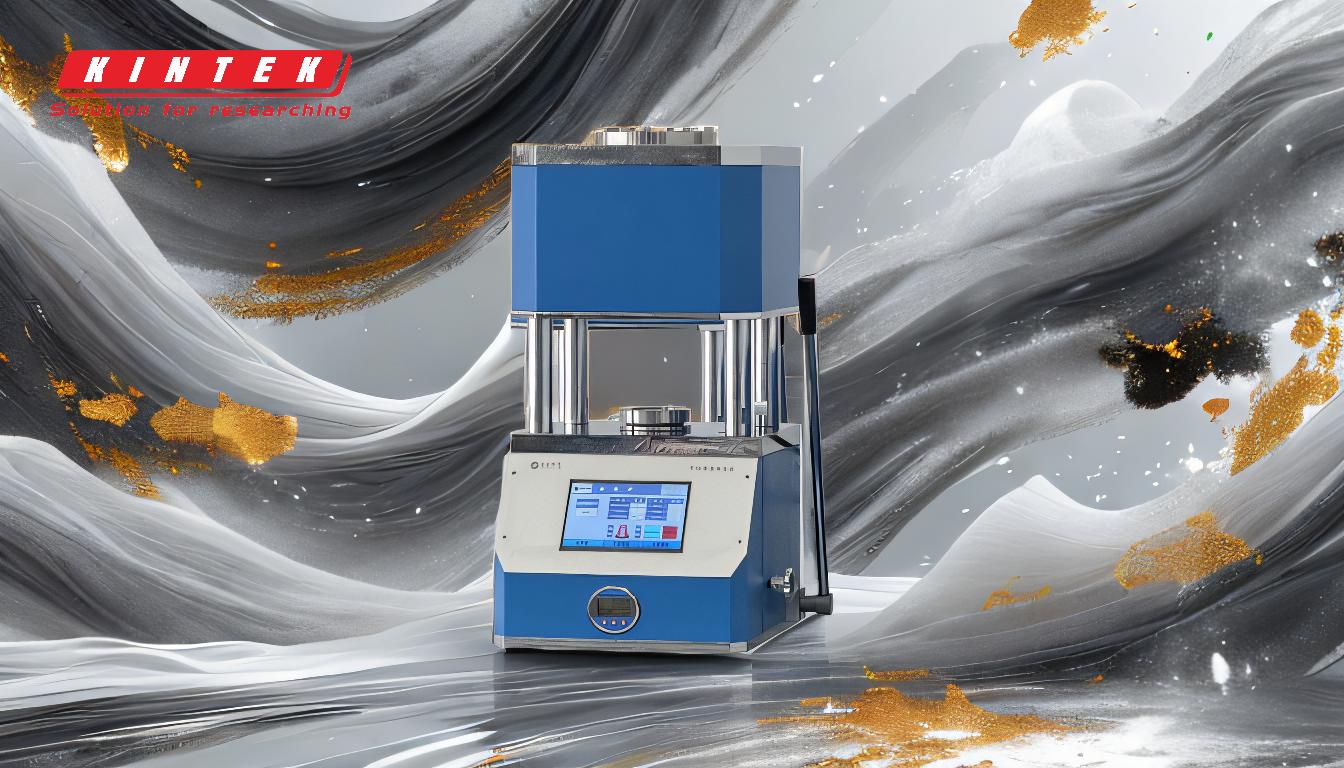
-
Principle of Forging Press Operation:
- A forging press uses compressive force to shape metal. This force is generated either mechanically, hydraulically, or pneumatically, with hydraulic systems being the most common due to their ability to deliver high, consistent pressure.
- The hydraulic system operates based on Pascal's Law, which states that pressure applied to a confined fluid is transmitted equally in all directions. This principle allows the hydraulic cylinder to amplify the force applied to the metal workpiece.
-
Key Components and Their Functions:
- Hydraulic Cylinder: The core component that generates the forging force. It converts hydraulic pressure into linear motion, driving the pressing plate to apply force to the workpiece.
- Oil Tank: Stores the hydraulic fluid, which is essential for transmitting pressure within the system. The fluid must be clean and free of contaminants to ensure smooth operation.
- Pressure Gauge: Monitors the hydraulic pressure, allowing operators to ensure that the system is operating within safe and optimal parameters.
- Relief Valve: Protects the system from overpressure by releasing excess hydraulic fluid back into the oil tank, preventing damage to the components.
- Manual Control Valve: Enables operators to regulate the flow of hydraulic fluid, controlling the speed and force of the pressing action.
- Limit Switch: Ensures precise movement of the pressing plate by stopping the hydraulic cylinder at predetermined positions, enhancing accuracy and safety.
- Safety Door: Provides a physical barrier to protect operators from moving parts and high-pressure systems during operation.
- Pressing Plate: The component that directly contacts the workpiece, applying the compressive force to shape or deform the metal.
-
Advantages of Hydraulic Forging Presses:
- High Force Output: Hydraulic systems can generate immense force, making them suitable for forging large or dense metal components.
- Precision Control: The ability to finely adjust pressure and speed ensures consistent results and minimizes material waste.
- Versatility: Hydraulic forging presses can handle a wide range of materials and shapes, from simple to complex geometries.
- Safety Features: Components like the safety door and relief valve enhance operator safety and protect the equipment from damage.
-
Applications of Forging Presses:
- Forging presses are widely used in industries such as automotive, aerospace, and manufacturing to produce components like gears, crankshafts, and turbine blades.
- They are also employed in the production of tools, machinery parts, and structural components that require high strength and durability.
By understanding the principle of forging presses and the role of their key components, operators and purchasers can make informed decisions about equipment selection, maintenance, and operation. This knowledge ensures optimal performance, safety, and efficiency in forging processes.
Summary Table:
Key Component | Function |
---|---|
Hydraulic Cylinder | Converts hydraulic pressure into linear motion to apply forging force. |
Oil Tank | Stores clean hydraulic fluid for pressure transmission. |
Pressure Gauge | Monitors hydraulic pressure to ensure safe and optimal operation. |
Relief Valve | Releases excess fluid to prevent overpressure and protect components. |
Manual Control Valve | Regulates fluid flow to control speed and force of pressing action. |
Limit Switch | Ensures precise movement by stopping the cylinder at predetermined positions. |
Safety Door | Protects operators from moving parts and high-pressure systems. |
Pressing Plate | Directly applies compressive force to shape or deform metal workpieces. |
Ready to enhance your metal shaping process? Contact us today to learn more about forging presses!