Physical Vapor Deposition (PVD) is a process used to deposit thin films of material onto a substrate by converting a solid target material into a vapor phase, which then condenses onto the substrate. This method is widely used in industries for creating durable, corrosion-resistant, and high-temperature-tolerant coatings. PVD involves several techniques, including thermal evaporation, sputtering, and arc discharge, all conducted in a vacuum or low-pressure environment. The process is characterized by its ability to produce thin films with excellent adhesion and uniformity, making it suitable for applications requiring precise material properties.
Key Points Explained:
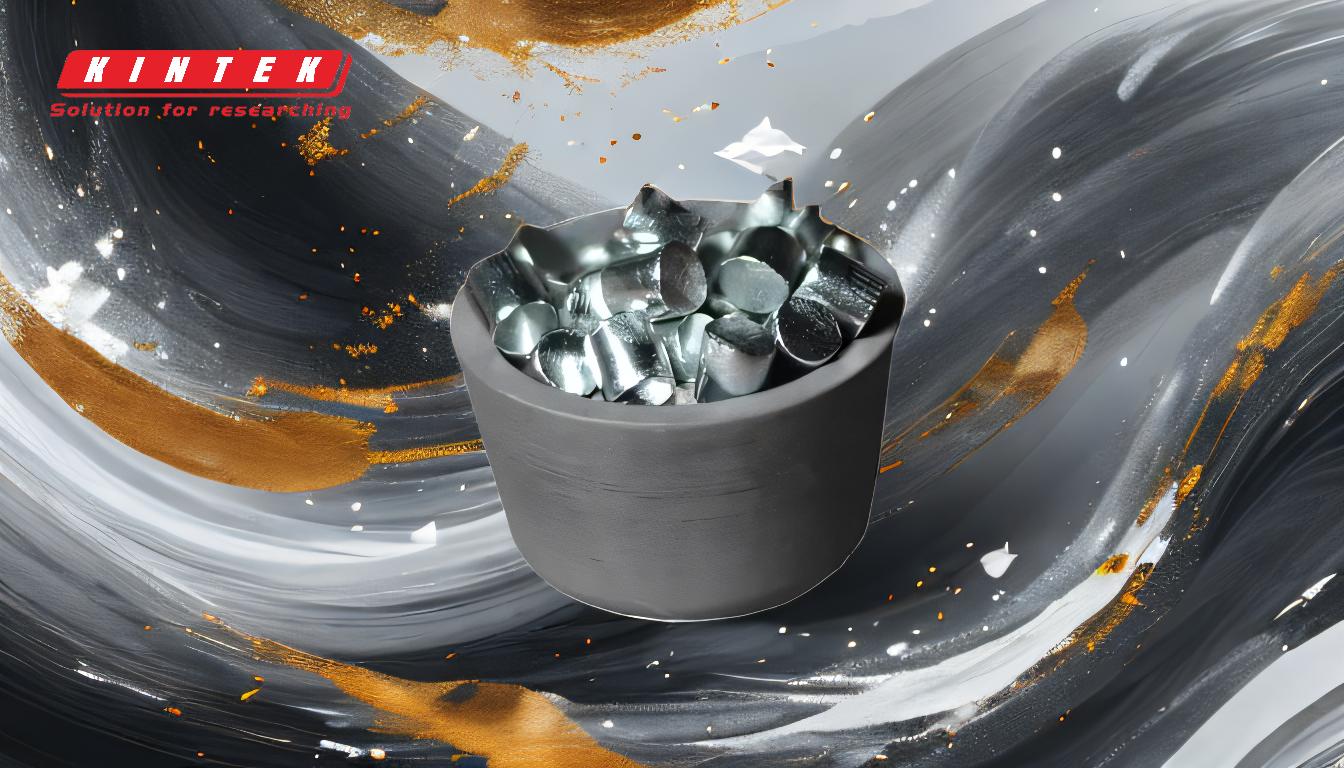
-
Conversion of Solid to Vapor Phase:
- The core principle of PVD involves transforming a solid target material into a vapor phase. This is achieved through various methods such as thermal evaporation, sputtering, or arc discharge.
- The target material is subjected to high-energy sources like electron beams, laser beams, or electrical discharges, causing it to vaporize.
- The vaporized material then travels through a vacuum or low-pressure chamber towards the substrate.
-
Deposition onto the Substrate:
- Once the target material is in the vapor phase, it moves through the reaction chamber and condenses onto the substrate.
- This condensation process forms a thin film on the substrate's surface. The film's properties, such as thickness, adhesion, and uniformity, are controlled by adjusting parameters like temperature, pressure, and deposition rate.
- The deposition occurs in a "line-of-sight" manner, meaning the vaporized atoms travel directly from the target to the substrate, embedding themselves onto the surface.
-
Techniques Involved in PVD:
- Thermal Evaporation: The target material is heated to its evaporation point using resistive heating or electron beams. The evaporated atoms then travel to the substrate and condense.
- Sputtering: High-energy ions bombard the target material, dislodging atoms from its surface. These atoms then deposit onto the substrate.
- Arc Discharge: An electric arc is used to vaporize the target material, which then deposits onto the substrate.
- Each technique has its advantages and is chosen based on the desired film properties and the materials involved.
-
Vacuum or Low-Pressure Environment:
- PVD processes are typically conducted in a vacuum or low-pressure chamber to minimize contamination and ensure a controlled environment.
- The absence of air or other gases prevents oxidation and other unwanted chemical reactions, ensuring the purity and quality of the deposited film.
- The vacuum environment also allows for better control over the deposition process, enabling precise adjustments to film thickness and composition.
-
Advantages of PVD:
- High-Quality Thin Films: PVD produces thin films with excellent adhesion, uniformity, and density, making them suitable for demanding applications.
- Material Versatility: PVD can handle a wide range of materials, including those with high melting points, which are difficult to process using other methods.
- Durability and Resistance: Films produced by PVD are highly durable, corrosion-resistant, and capable of withstanding high temperatures, making them ideal for protective coatings.
- Environmental Benefits: PVD is a clean process that produces minimal waste, making it environmentally friendly compared to other coating methods.
-
Applications of PVD:
- Electronics: PVD is used to deposit thin films in the manufacturing of semiconductors, solar cells, and displays.
- Optics: It is employed to create anti-reflective, reflective, and protective coatings on lenses and mirrors.
- Automotive: PVD coatings are applied to engine components, cutting tools, and decorative finishes to enhance durability and performance.
- Medical Devices: PVD is used to coat medical instruments and implants with biocompatible and wear-resistant materials.
In summary, Physical Vapor Deposition is a versatile and precise method for depositing thin films of material onto substrates. By converting a solid target material into a vapor phase and then condensing it onto a substrate, PVD produces high-quality coatings with excellent adhesion, durability, and resistance to environmental factors. The process is conducted in a controlled vacuum or low-pressure environment, ensuring the purity and consistency of the deposited films. With its wide range of applications and numerous advantages, PVD is a critical technology in various industries.
Summary Table:
Key Aspect | Details |
---|---|
Process | Converts solid target material into vapor, condensing it onto a substrate. |
Techniques | Thermal evaporation, sputtering, arc discharge. |
Environment | Conducted in a vacuum or low-pressure chamber. |
Advantages | High-quality films, material versatility, durability, eco-friendly. |
Applications | Electronics, optics, automotive, medical devices. |
Interested in PVD solutions for your industry? Contact us today to learn more!