Spark Plasma Sintering (SPS), also known as Field Assisted Sintering Technique (FAST) or Direct Current Sintering (DCS), is an advanced sintering process that combines pressure and an electric field to achieve rapid densification of ceramic and metallic powders. The process involves applying a pulsed direct current (DC) to the powder or green compact, which generates plasma, Joule heating, and electromigration effects. These effects lead to localized high temperatures, surface activation, and rapid particle bonding, resulting in high-density materials in a short time. Despite its name, research indicates that plasma generation may not be the primary mechanism, but the process still offers advantages such as lower sintering temperatures, shorter processing times, and energy efficiency.
Key Points Explained:
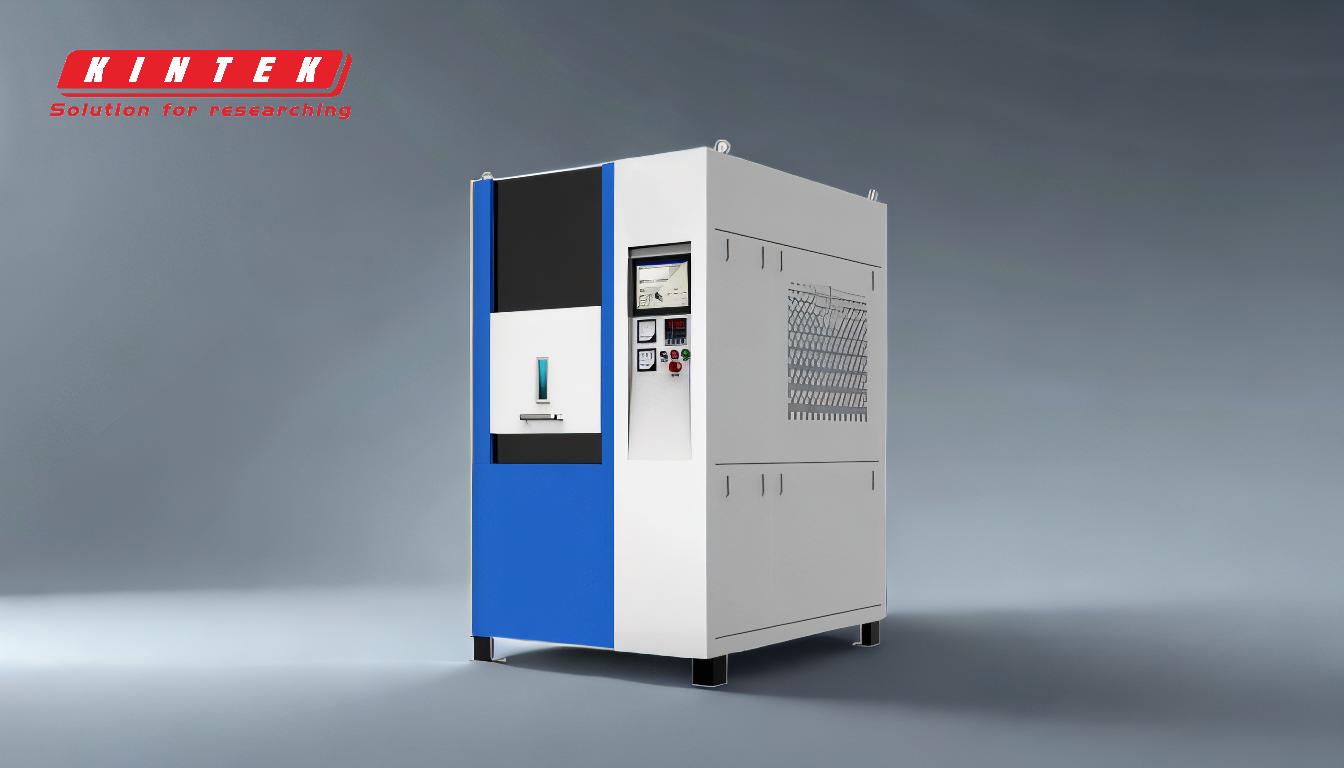
-
Application of Pulsed Direct Current (DC):
- SPS utilizes a pulsed DC current applied directly to the powder or green compact. This current generates localized high temperatures and plasma between particles, which facilitates rapid sintering.
- The pulsed nature of the current allows for precise control of the heating and cooling rates, enabling the process to achieve high densification in a short time.
-
Generation of Plasma and Joule Heating:
- The pulsed current creates a spark plasma between particles, reaching temperatures as high as 10,000°C (18,032°F). This high temperature causes surface activation, melting, and bonding of particles.
- Joule heating, caused by the resistance of the material to the electric current, further contributes to the rapid heating and densification of the powder.
-
Surface Activation and Particle Bonding:
- The high temperatures generated by the pulsed current cause the surfaces of the particles to melt and form necks, which are initial bonds between particles. Over time, these necks develop into more solid connections, increasing the overall density of the material.
- The process also helps in the removal of surface contaminants through oxidation or evaporation, leading to cleaner and stronger particle bonds.
-
Integration of Pressure and Electric Field:
- SPS combines the application of mechanical pressure with the electric field generated by the pulsed current. This combination enhances the densification process by reducing particle gaps and promoting surface diffusion.
- The pressure applied during sintering helps in consolidating the particles, while the electric field aids in the rapid heating and activation of particle surfaces.
-
Advantages of SPS:
- Lower Sintering Temperatures: SPS allows for sintering at temperatures several hundred degrees lower than conventional sintering methods, reducing energy consumption and minimizing thermal stress on the material.
- Short Processing Time: The rapid heating and cooling rates, along with short holding times, enable the process to be completed in a fraction of the time required by traditional sintering methods.
- High Densification: SPS can achieve material densities of over 99%, making it suitable for producing high-performance ceramics and metals.
- Energy Efficiency and Environmental Friendliness: The process is more energy-efficient compared to conventional sintering, and it produces less waste, making it an environmentally friendly option.
-
Mechanisms of Densification:
- Discharge Impact Pressure: The pulsed current generates discharge impact pressure, which helps in reducing the gaps between particles and promoting densification.
- Electromigration and Electroplasticity: These effects, caused by the electric field, enhance the mobility of atoms and defects, facilitating faster diffusion and bonding of particles.
- Surface Diffusion and Boundary Defect Diffusion: The high temperatures and electric field promote surface diffusion and the movement of defects at particle boundaries, leading to rapid densification.
-
Misconceptions and Alternative Names:
- Despite its name, research has shown that the generation of plasma may not be the primary mechanism in SPS. This has led to the adoption of alternative names such as Field Assisted Sintering Technique (FAST), Electric Field Assisted Sintering (EFAS), and Direct Current Sintering (DCS).
- The process is more accurately described as a combination of electric field-assisted sintering and hot pressing, where the electric field enhances the sintering process without necessarily generating plasma.
-
Applications of SPS:
- SPS is widely used in the production of advanced ceramics, metals, and composites. It is particularly useful for materials that require high density, fine grain structure, and enhanced mechanical properties.
- The process is also employed in the development of nanomaterials, where precise control over sintering conditions is crucial for achieving the desired material properties.
In summary, Spark Plasma Sintering is a highly efficient and versatile sintering technique that leverages the combined effects of pulsed electric current, pressure, and Joule heating to achieve rapid densification of materials. Its ability to produce high-density materials at lower temperatures and in shorter times makes it a valuable tool in the development of advanced materials.
Summary Table:
Key Aspects | Details |
---|---|
Process | Combines pulsed DC current, pressure, and electric fields for sintering. |
Temperature Range | Up to 10,000°C (18,032°F) for localized heating. |
Densification | Achieves over 99% material density. |
Advantages | Lower sintering temperatures, short processing times, energy efficiency. |
Applications | Advanced ceramics, metals, composites, and nanomaterials. |
Learn how Spark Plasma Sintering can revolutionize your material production—contact our experts today!