The bell annealing furnace process involves heating materials to high temperatures to alter their mechanical properties, such as strength, hardness, and ductility. The process begins by stacking parts on a base plate and lowering the bell furnace over them. The trapped air is purged with nitrogen to reduce oxygen levels, followed by introducing a hydrogen/nitrogen atmosphere. The furnace heats the material above its recrystallization temperature, holds it at this temperature for a specific duration, and then cools it gradually. This process includes three main stages: recovery, recrystallization, and grain growth, which collectively improve the material's workability and reduce internal stresses.
Key Points Explained:
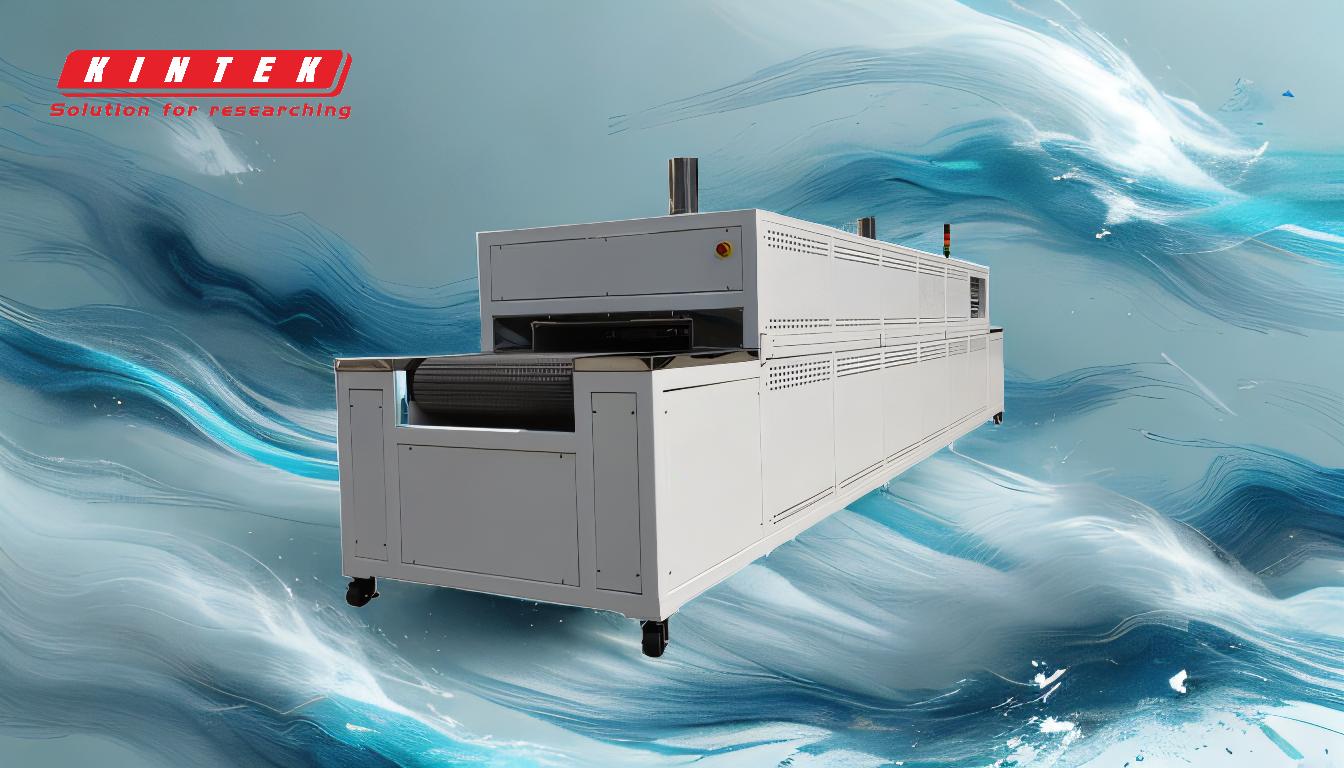
-
Preparation of Parts and Furnace Setup:
- Parts are stacked on a base plate, and the bell furnace is lowered over them.
- This setup ensures uniform heating and treatment of the stacked parts.
-
Purging Air with Nitrogen:
- The trapped air inside the furnace is purged with nitrogen until the oxygen concentration is reduced below a specific limit.
- This step is crucial to prevent oxidation and ensure a controlled atmosphere for annealing.
-
Introduction of Hydrogen/Nitrogen Atmosphere:
- After purging, the furnace is filled with a hydrogen/nitrogen mixture.
- This atmosphere helps in achieving the desired material properties by preventing oxidation and facilitating the annealing process.
-
Heating Above Recrystallization Temperature:
- The furnace heats the material above its recrystallization temperature but below its melting point.
- This heating is essential to make the material more ductile and ready for further processing.
-
Holding at Desired Temperature:
- The material is held at the elevated temperature for a specific time interval.
- This duration allows for the necessary microstructural changes, such as stress relief and grain formation.
-
Cooling Process:
- After the holding period, the material is cooled at a steady rate.
- Controlled cooling is vital to achieve the desired grain structure and mechanical properties.
-
Three Stages of Annealing:
- Recovery: The initial heating stage where internal stresses are relieved.
- Recrystallization: The material is heated above the recrystallization temperature, allowing new grains to form.
- Grain Growth: During cooling, new grains grow, making the material more pliable and reducing internal stresses.
-
Benefits of Bell Annealing Furnace:
- Improved Ductility: The process makes the material more ductile, enhancing its workability.
- Stress Relief: Internal stresses are relieved, reducing the risk of material failure.
- Enhanced Mechanical Properties: The material's strength and hardness are altered to meet specific requirements.
By following these steps, the bell annealing furnace effectively modifies the material's properties, making it suitable for various industrial applications. The controlled environment and precise temperature management ensure consistent and high-quality results.
Summary Table:
Stage | Description |
---|---|
Preparation | Parts are stacked on a base plate, and the bell furnace is lowered over them. |
Purging with Nitrogen | Trapped air is purged with nitrogen to reduce oxygen levels and prevent oxidation. |
Hydrogen/Nitrogen Atmosphere | A hydrogen/nitrogen mixture is introduced to facilitate annealing. |
Heating | Material is heated above recrystallization temperature for ductility. |
Holding | Material is held at the desired temperature for microstructural changes. |
Cooling | Controlled cooling ensures desired grain structure and mechanical properties. |
Three Stages | Recovery, recrystallization, and grain growth improve material workability. |
Benefits | Improved ductility, stress relief, and enhanced mechanical properties. |
Discover how the bell annealing furnace can optimize your material properties—contact us today for expert guidance!