Bio-oil, also known as pyrolysis oil, is a dark brown organic liquid produced through the fast pyrolysis of biomass. This process involves rapidly heating dry biomass to approximately 500°C in the absence of oxygen, followed by quick cooling of the resulting vapors to condense them into liquid bio-oil. The biomass components—cellulose, hemicellulose, and lignin—undergo simultaneous fragmentation and depolymerization during pyrolysis, leading to the formation of bio-oil. The liquid is typically brown, dark red, or black, with a density of about 1.2 kg/liter. Bio-oil can be further upgraded through methods like hydrodeoxygenation or catalytic pyrolysis to improve its quality and usability as a substitute for fossil fuels in heating, electricity generation, and transportation.
Key Points Explained:
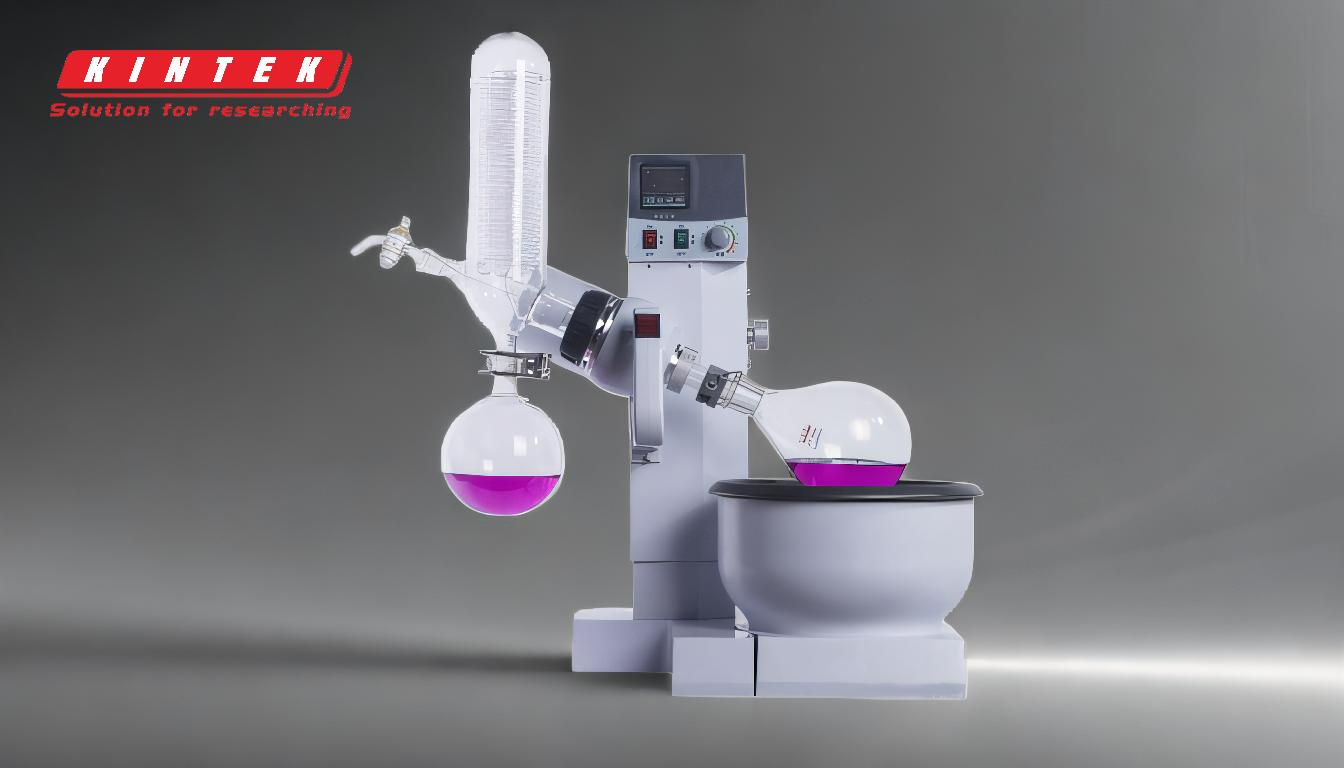
-
Definition and Composition of Bio-oil:
- Bio-oil is a liquid product derived from the pyrolysis of biomass, primarily composed of water and organic compounds from cellulose, hemicellulose, and lignin.
- It is typically dark brown, dark red, or black in color and has a density of approximately 1.2 kg/liter.
-
Pyrolysis Process:
- Pyrolysis is the thermal decomposition of biomass in the absence of oxygen.
- Fast pyrolysis, the most common method for bio-oil production, involves:
- Rapid heating of biomass to around 500°C.
- Quick cooling (quenching) of the resulting vapors to condense them into liquid bio-oil.
- This process converts biomass into three main products: gas, solid char, and liquid bio-oil.
-
Mechanism of Bio-oil Formation:
- During fast pyrolysis, the biomass components (cellulose, hemicellulose, and lignin) undergo simultaneous fragmentation and depolymerization.
- This results in the breakdown of complex organic molecules into simpler compounds, which are then condensed into bio-oil.
-
Properties of Bio-oil:
- Bio-oil is an emulsion of water and organic compounds, making it chemically complex and unstable.
- It has a high oxygen content, which contributes to its corrosive nature and low energy density compared to fossil fuels.
- The liquid is acidic, with a pH typically ranging from 2 to 4.
-
Upgrading Bio-oil:
- Hydrodeoxygenation: A method to upgrade bio-oil by removing oxygen under high pressure and temperature, improving its stability and energy content. However, this process is costly and energy-intensive.
- Catalytic Pyrolysis: An alternative method where catalysts are used during pyrolysis to deoxygenate bio-oil in situ, reducing the need for post-processing.
-
Applications of Bio-oil:
- Bio-oil can be used as a substitute for fossil fuels in various applications, including:
- Heating and electricity generation.
- Transportation fuels after further refining and upgrading.
- Its use helps reduce greenhouse gas emissions and reliance on non-renewable energy sources.
- Bio-oil can be used as a substitute for fossil fuels in various applications, including:
-
Challenges in Bio-oil Production:
- The high oxygen content and instability of bio-oil make it challenging to store and transport.
- Upgrading processes like hydrodeoxygenation are expensive and require significant energy input.
- The quality and consistency of bio-oil can vary depending on the feedstock and pyrolysis conditions.
-
Future Prospects:
- Research is ongoing to develop more efficient and cost-effective methods for bio-oil upgrading, such as advanced catalytic techniques.
- The integration of bio-oil production with other renewable energy systems could enhance its viability as a sustainable energy source.
By understanding the process of bio-oil production and its challenges, stakeholders in the energy and manufacturing sectors can make informed decisions about its potential as a renewable fuel source.
Summary Table:
Key Aspect | Details |
---|---|
Definition | Dark brown liquid from fast pyrolysis of biomass. |
Composition | Water and organic compounds (cellulose, hemicellulose, lignin). |
Production Process | Rapid heating to 500°C, followed by quick cooling to condense vapors. |
Properties | High oxygen content, acidic (pH 2-4), density ~1.2 kg/liter. |
Upgrading Methods | Hydrodeoxygenation, catalytic pyrolysis. |
Applications | Heating, electricity, transportation fuels. |
Challenges | High oxygen content, instability, costly upgrading processes. |
Future Prospects | Research on advanced catalytic techniques and renewable energy integration. |
Discover how bio-oil can transform your energy solutions—contact us today for expert guidance!