Calcination is a thermal treatment process used to decompose materials, remove volatile substances, or induce phase transitions by heating them below their melting point, typically in the absence or limited supply of air or oxygen. This process is widely used in industries such as metallurgy, ceramics, and chemical manufacturing to produce inorganic materials like calcium oxide from calcium carbonate or to remove moisture from substances like borax. Rotary kilns are commonly employed for calcination, especially for materials like limestone, dolomite, and magnesite, as they ensure uniform heating and higher production rates. The process is essential for achieving chemical dissociation and producing high-quality, thermally stable materials.
Key Points Explained:
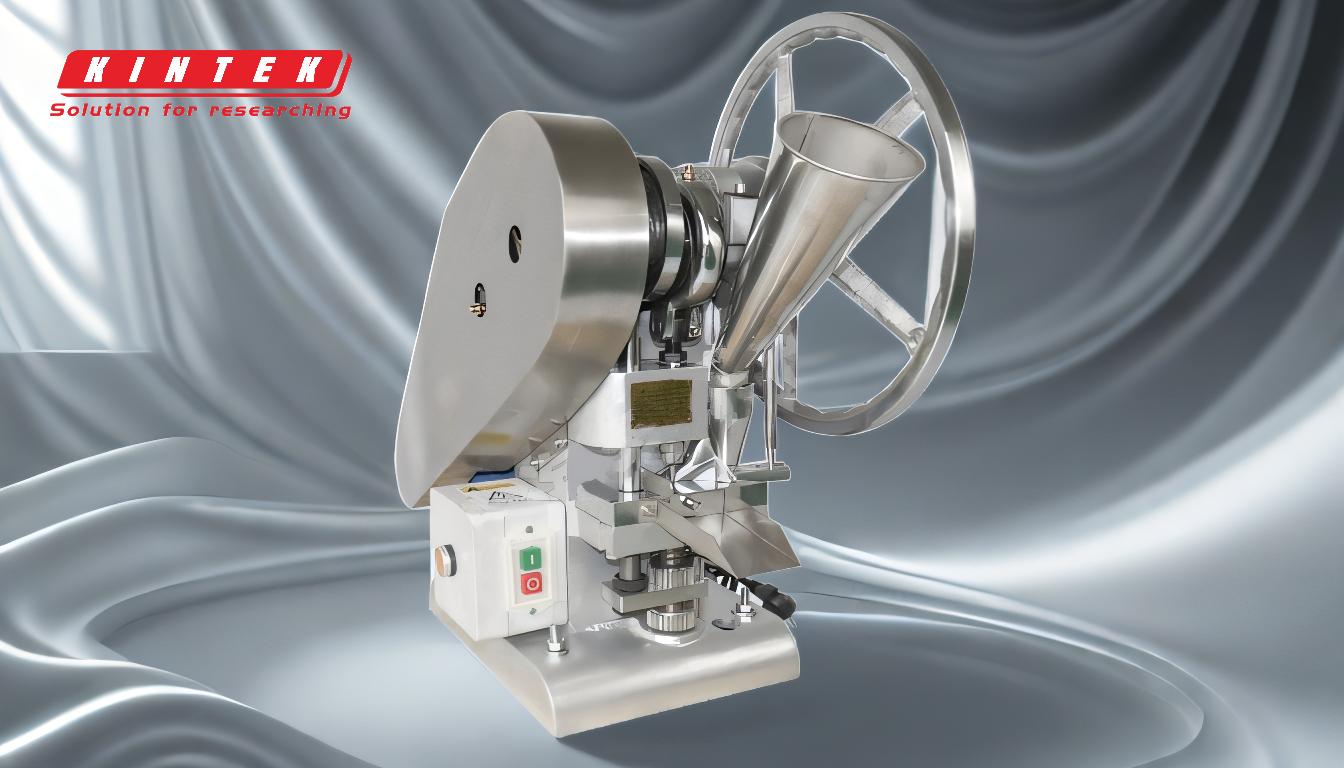
-
Definition of Calcination:
- Calcination is a heat treatment process where materials are heated to high temperatures, typically below their melting point, in the absence or limited supply of air or oxygen.
- It is used to induce thermal decomposition, remove volatile substances, or cause phase transitions in materials.
-
Purpose of Calcination:
- Thermal Decomposition: Breaks down compounds into simpler substances. For example, calcium carbonate (CaCO₃) decomposes into calcium oxide (CaO) and carbon dioxide (CO₂).
- Removal of Volatiles: Eliminates moisture, carbon dioxide, or other volatile components from materials like borax or ores.
- Phase Transition: Converts materials into more stable or usable forms, such as transforming hydrated minerals into anhydrous forms.
-
Materials Commonly Processed:
- Limestone (CaCO₃): Decomposes into lime (CaO) and CO₂, which is essential in cement production.
- Dolomite (CaMg(CO₃)₂): Used to produce magnesium oxide (MgO) and calcium oxide (CaO).
- Magnesite (MgCO₃): Converts to magnesium oxide (MgO), used in refractory materials.
- Borax (Na₂B₄O₇·10H₂O): Loses bound water to form anhydrous borax.
-
Process Conditions:
- Temperature: Calcination typically occurs at high temperatures, often between 800°C to 1200°C, depending on the material.
- Atmosphere: The process is carried out in the absence or limited supply of air or oxygen to prevent oxidation or combustion.
- Time: The duration of heating depends on the material and desired outcome, ensuring complete decomposition or removal of volatiles.
-
Equipment Used for Calcination:
- Rotary Kilns: Preferred for calcination due to their ability to handle large volumes and provide uniform heating. They are suitable for materials with particle sizes of 60 mm or less.
- Static Kilns: Used for smaller-scale operations or specific materials requiring precise temperature control.
- Fluidized Bed Reactors: Employed for fine particles, ensuring efficient heat transfer and uniform calcination.
-
Applications of Calcination:
- Metallurgy: Extracting metals from ores by removing impurities or decomposing metal carbonates.
- Cement Production: Producing lime (CaO) from limestone, a key ingredient in cement.
- Chemical Manufacturing: Creating inorganic materials like magnesium oxide or anhydrous borax.
- Ceramics: Preparing raw materials for ceramic production by removing moisture or decomposing carbonates.
-
Advantages of Calcination:
- High Purity: Produces materials with reduced impurities and volatile content.
- Thermal Stability: Enhances the thermal and chemical stability of materials.
- Versatility: Applicable to a wide range of materials and industries.
-
Challenges and Considerations:
- Energy Consumption: Calcination requires significant energy input due to high temperatures.
- Environmental Impact: The release of CO₂ during calcination, especially in limestone processing, contributes to greenhouse gas emissions.
- Material Handling: Ensuring uniform heating and avoiding overheating or underheating requires precise control and monitoring.
By understanding the calcination process, its purpose, and the equipment involved, industries can optimize material processing, improve product quality, and address environmental challenges.
Summary Table:
Aspect | Details |
---|---|
Definition | Heating materials below melting point to decompose or remove volatiles. |
Purpose | Thermal decomposition, volatile removal, and phase transitions. |
Common Materials | Limestone, dolomite, magnesite, borax. |
Temperature Range | 800°C to 1200°C. |
Equipment | Rotary kilns, static kilns, fluidized bed reactors. |
Applications | Metallurgy, cement production, chemical manufacturing, ceramics. |
Advantages | High purity, thermal stability, versatility. |
Challenges | High energy consumption, CO₂ emissions, precise material handling required. |
Optimize your calcination process today—contact our experts for tailored solutions!