DC magnetron sputtering is a widely used thin-film deposition technique that involves the use of a direct current (DC) power source to generate plasma in a low-pressure environment. The process begins by evacuating the chamber to a high vacuum to minimize contaminants. An inert gas, typically argon, is introduced, and the pressure is maintained in the milli Torr range. A high voltage is applied to create plasma, and a magnetic field is used to concentrate the plasma near the target material (cathode). Positively charged ions from the plasma are accelerated towards the target, causing atoms to be ejected and deposited onto the substrate, forming a thin film. The magnetic field enhances the sputtering rate and ensures uniform deposition. This method is particularly effective for depositing pure metals like Iron (Fe), Copper (Cu), and Nickel (Ni).
Key Points Explained:
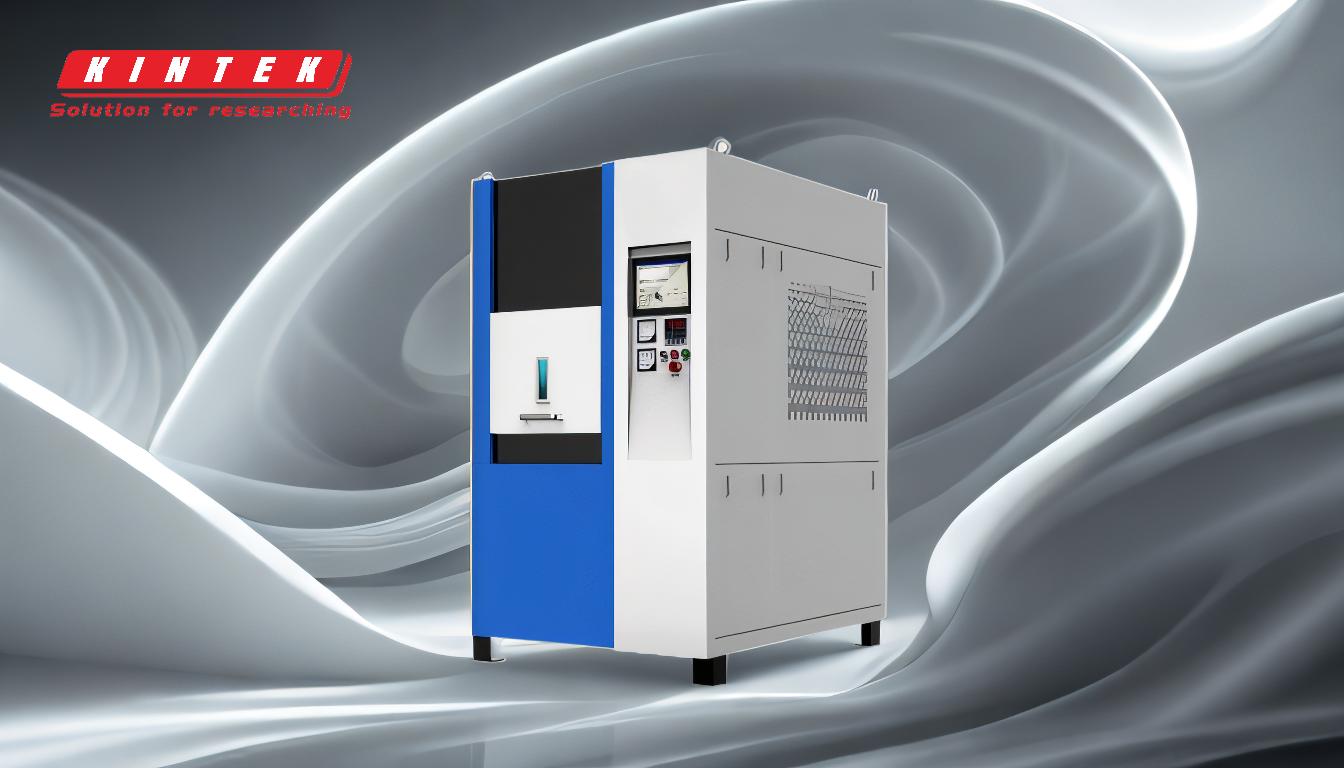
-
Vacuum Chamber Preparation:
- The process begins by evacuating the chamber to a high vacuum to reduce contaminants. This ensures a clean environment for the deposition process, which is crucial for achieving high-quality thin films.
-
Introduction of Inert Gas:
- An inert gas, usually argon, is introduced into the chamber. The pressure is maintained in the milli Torr range (1 to 100 mTorr). Argon is chosen because it is chemically inert and does not react with the target material or the substrate.
-
Generation of Plasma:
- A high voltage is applied to generate plasma within the chamber. The plasma consists of argon gas atoms, argon ions, and free electrons. The magnetic field generated by the magnetron concentrates the plasma near the target material, increasing the efficiency of the sputtering process.
-
Role of Magnetic Field:
- The magnetic field is crucial in DC magnetron sputtering. It traps electrons near the target surface, increasing their path length and the likelihood of collisions with argon atoms. This results in a higher density of positively charged argon ions, which are essential for the sputtering process.
-
Sputtering of Target Material:
- Positively charged argon ions are accelerated towards the target material (cathode) due to the electric field. When these ions strike the target, they eject neutral atoms, molecules, and secondary electrons from the target material. This process is known as sputtering.
-
Deposition on Substrate:
- The ejected atoms travel through the chamber and deposit onto the substrate, which is typically placed on the anode. The atoms condense on the substrate surface, forming a thin film of the target material. The magnetic field ensures that the deposition is uniform across the substrate.
-
Maintenance of Plasma:
- Secondary electrons emitted during the sputtering process collide with argon atoms in the chamber, ionizing them and helping to maintain the plasma. This self-sustaining process ensures continuous sputtering and deposition.
-
Applications and Materials:
- DC magnetron sputtering is commonly used for depositing pure metals such as Iron (Fe), Copper (Cu), and Nickel (Ni). The technique is favored for its ability to produce high-quality, uniform thin films, making it suitable for applications in electronics, optics, and coatings.
-
Advantages of DC Magnetron Sputtering:
- The use of a magnetic field increases the sputtering rate and improves the uniformity of the deposited film. The process is also relatively simple and can be used with a wide range of materials, making it versatile for various industrial applications.
-
System Components:
- A typical DC magnetron sputtering system consists of an evacuable chamber, a DC power source, a target material (cathode), a substrate holder (anode), and a magnetic assembly. The magnetic assembly is crucial for generating the magnetic field that enhances the sputtering process.
By understanding each of these key points, one can appreciate the complexity and efficiency of the DC magnetron sputtering process. This method is a cornerstone in the field of thin-film deposition, offering precise control over film properties and uniformity.
Summary Table:
Key Aspect | Description |
---|---|
Vacuum Preparation | Chamber evacuated to high vacuum to minimize contaminants. |
Inert Gas | Argon introduced at 1-100 mTorr for a chemically inert environment. |
Plasma Generation | High voltage creates plasma; magnetic field concentrates it near the target. |
Magnetic Field Role | Traps electrons, increasing ion density and sputtering efficiency. |
Sputtering Process | Argon ions eject target atoms, which deposit onto the substrate. |
Deposition Uniformity | Magnetic field ensures even film deposition across the substrate. |
Plasma Maintenance | Secondary electrons sustain the plasma for continuous sputtering. |
Applications | Used for depositing pure metals like Fe, Cu, and Ni in electronics and optics. |
Advantages | High sputtering rate, uniform films, and versatility for various materials. |
System Components | Includes chamber, DC power source, target, substrate holder, and magnetic assembly. |
Discover how DC magnetron sputtering can elevate your thin-film deposition process—contact our experts today!