Forging is a manufacturing process that involves shaping metal using localized compressive forces. It is typically performed at high temperatures to make the metal more malleable, although cold forging is also possible. The process begins with heating the metal to a specific temperature, followed by shaping it using dies or hammers. Forging enhances the mechanical properties of the metal, such as strength and durability, by aligning the grain structure. The final step often involves finishing processes like machining or heat treatment to achieve the desired dimensions and properties. Forging is widely used in industries like automotive, aerospace, and construction to produce high-strength components.
Key Points Explained:
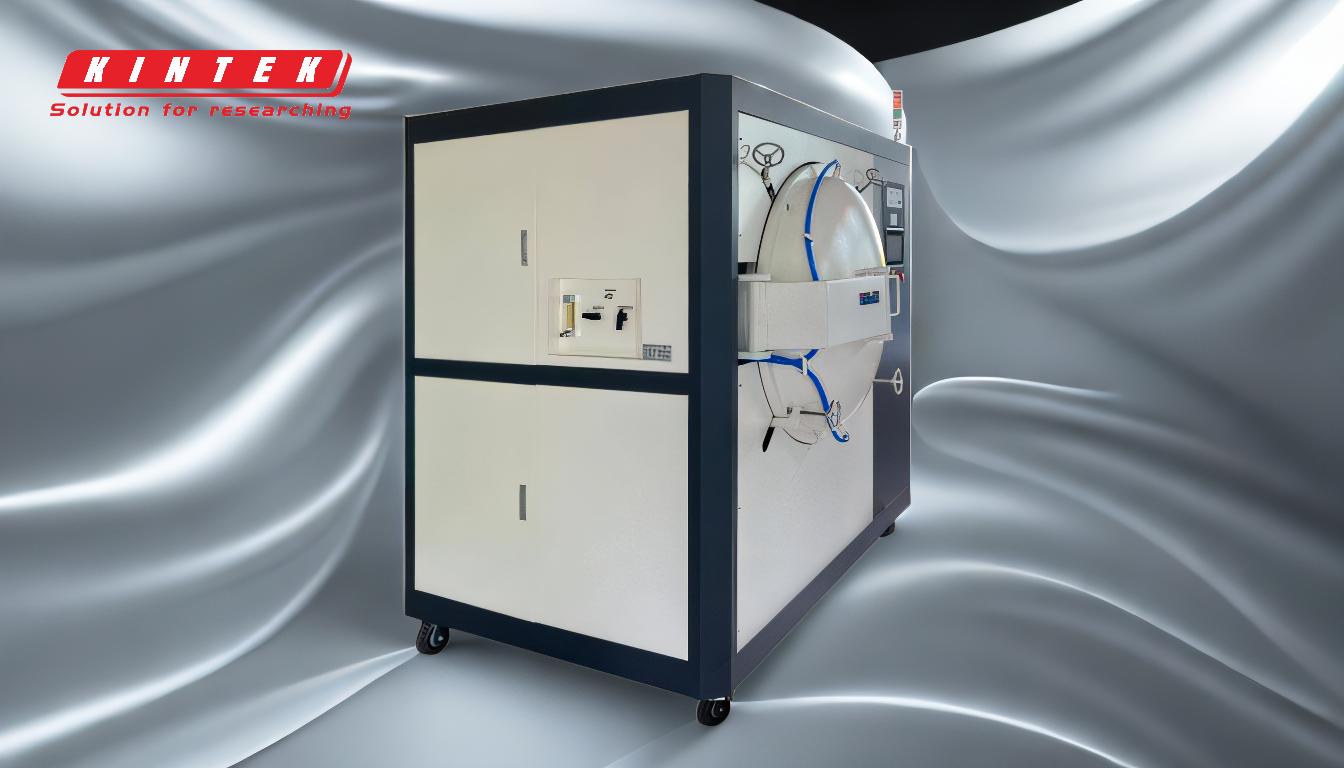
-
Heating the Metal:
- The first step in forging is heating the metal to a specific temperature, which makes it more malleable and easier to shape. The temperature varies depending on the type of metal being forged. For example, steel is typically heated to around 2,100°F (1,150°C).
-
Shaping the Metal:
- Once the metal is heated, it is placed on a die or anvil and shaped using compressive forces. This can be done through various methods such as hammering, pressing, or rolling. The shaping process can be done manually or with the help of machines, depending on the complexity and size of the part being forged.
-
Types of Forging:
- Open-Die Forging: This method involves shaping the metal between flat dies, allowing for more flexibility in the shape and size of the final product. It is often used for large or custom parts.
- Closed-Die Forging: In this method, the metal is placed in a die that contains a pre-shaped cavity. The metal is then forced into the cavity to take its shape. This method is more precise and is used for producing complex parts with tight tolerances.
- Roll Forging: This process involves passing the metal through a set of rollers to reduce its thickness and increase its length. It is commonly used for producing long, thin components like shafts or bars.
-
Enhancing Mechanical Properties:
- Forging improves the mechanical properties of the metal by aligning the grain structure along the contours of the final part. This results in increased strength, durability, and resistance to fatigue and impact. The process also eliminates internal voids and defects, resulting in a more uniform and reliable material.
-
Finishing Processes:
- After the forging process, the part often undergoes additional finishing processes to achieve the desired dimensions and surface quality. These processes may include machining, heat treatment, or surface finishing techniques like grinding or polishing. Heat treatment, in particular, is used to enhance the hardness and strength of the forged part.
-
Applications of Forging:
- Forging is used in a wide range of industries to produce high-strength components. In the automotive industry, forged parts include crankshafts, connecting rods, and gears. In aerospace, forged components are used in engines, landing gear, and structural parts. The construction industry also relies on forging for producing heavy-duty components like bolts, anchors, and structural beams.
-
Advantages of Forging:
- Strength and Durability: Forged parts are stronger and more durable than those produced by casting or machining.
- Material Efficiency: Forging minimizes material waste, as the process involves shaping the metal rather than removing material.
- Versatility: Forging can be used to produce a wide range of shapes and sizes, from small intricate parts to large structural components.
-
Challenges in Forging:
- Cost: The initial setup costs for forging can be high, especially for custom dies and tooling.
- Complexity: Producing complex shapes with tight tolerances can be challenging and may require specialized equipment and expertise.
- Material Limitations: Not all metals are suitable for forging, and some may require specific conditions or treatments to achieve the desired properties.
In summary, forging is a versatile and effective manufacturing process that enhances the mechanical properties of metal components. It involves heating, shaping, and finishing the metal to produce strong, durable parts used in various industries. Despite some challenges, the benefits of forging make it a preferred method for producing high-performance components.
Summary Table:
Step | Description |
---|---|
Heating the Metal | Metal is heated to a specific temperature to make it malleable. |
Shaping the Metal | Compressive forces shape the metal using dies, hammers, or rollers. |
Types of Forging | Open-die, closed-die, and roll forging for different shapes and precision. |
Enhancing Properties | Aligns grain structure for increased strength, durability, and reliability. |
Finishing Processes | Machining, heat treatment, or surface finishing to achieve desired properties. |
Applications | Used in automotive, aerospace, and construction for high-strength components. |
Discover how forging can elevate your manufacturing process—contact us today for expert guidance!