The Hot Isostatic Pressing (HIP) heat treatment process is a sophisticated technique used to enhance the physical properties of materials, such as strength and durability. It involves placing the material inside an HIP machine equipped with a furnace and a pressure vessel. Argon gas is introduced to increase both temperature and pressure within the vessel. After a specific duration, the vessel is cooled, and the treated material is removed, resulting in improved material characteristics.
Key Points Explained:
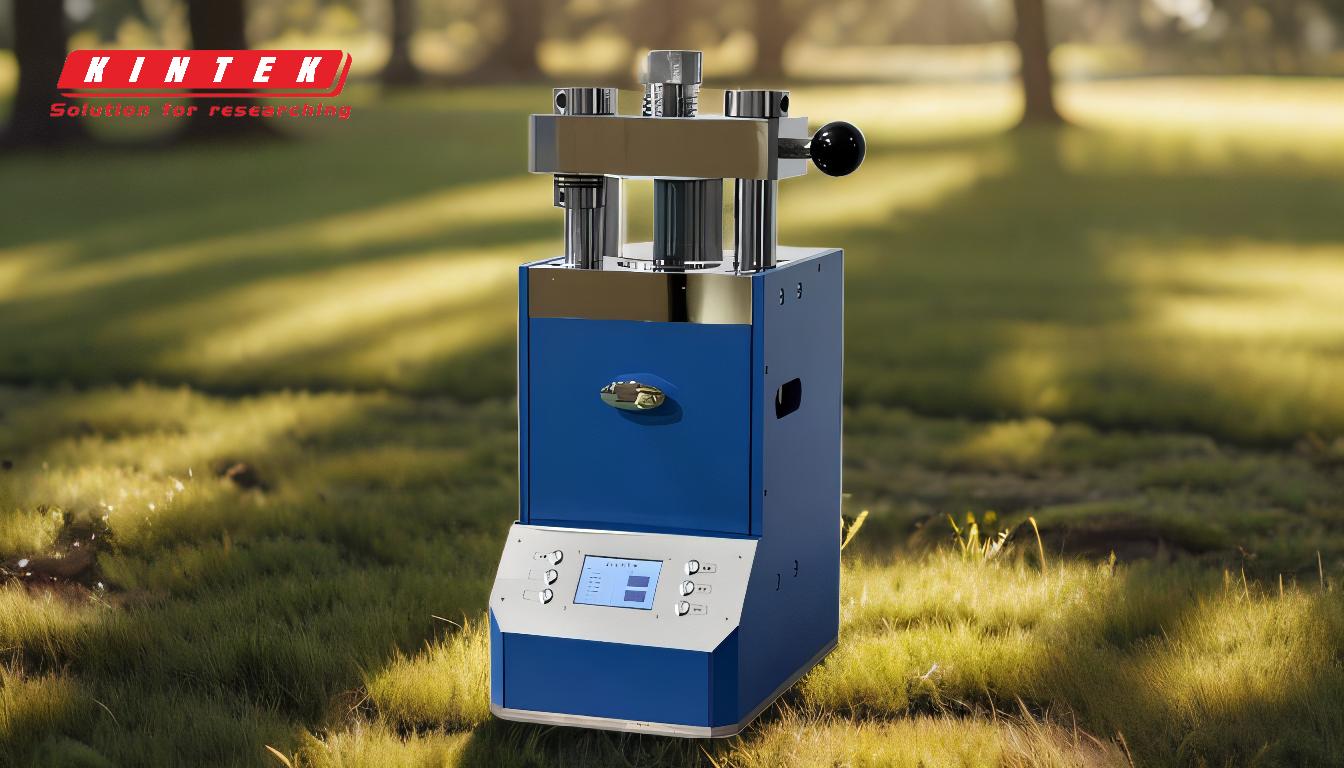
-
Introduction to HIP Heat Treatment:
- HIP is a process that combines high temperature and high pressure to improve the properties of materials. It is widely used in industries such as aerospace, automotive, and medical devices to enhance the strength, durability, and fatigue resistance of components.
-
Components of an HIP Machine:
- Furnace: The furnace within the HIP machine is responsible for heating the material to the desired temperature. The temperature can range from a few hundred to over 2000°C, depending on the material and the desired outcome.
- Pressure Vessel: The pressure vessel is designed to withstand the high pressures required for the HIP process. It is typically made from high-strength materials to ensure safety and durability.
-
Role of Argon Gas:
- Argon gas is used in the HIP process because it is inert, meaning it does not react with the material being treated. This ensures that the material's chemical composition remains unchanged.
- The gas is forced into the pressure vessel, increasing the internal pressure. This high pressure, combined with the high temperature, helps to eliminate voids and porosity within the material, leading to a more uniform and dense structure.
-
Temperature and Pressure Parameters:
- The specific temperature and pressure used in the HIP process depend on the material being treated. For example, metals like titanium and nickel-based alloys typically require higher temperatures and pressures compared to ceramics or composites.
- The process parameters are carefully controlled to ensure that the material reaches the desired state without causing any damage or degradation.
-
Cooling and Material Removal:
- After the material has been subjected to the desired temperature and pressure for a specific amount of time, the vessel is gradually cooled. This cooling process is crucial to prevent thermal shock, which could otherwise lead to cracking or other defects.
- Once the vessel has cooled to a safe temperature, the treated material is removed. The material is now stronger, more durable, and has improved mechanical properties.
-
Benefits of HIP Heat Treatment:
- Improved Material Properties: HIP treatment significantly enhances the strength, fatigue resistance, and overall durability of materials.
- Elimination of Defects: The process effectively eliminates internal voids, porosity, and other defects, leading to a more uniform and reliable material structure.
- Versatility: HIP can be applied to a wide range of materials, including metals, ceramics, and composites, making it a versatile solution for various industries.
-
Applications of HIP:
- Aerospace: HIP is used to treat critical components such as turbine blades, engine parts, and structural components, ensuring they can withstand extreme conditions.
- Medical Devices: The process is used to manufacture implants and prosthetics, providing them with the necessary strength and biocompatibility.
- Automotive: HIP-treated components are used in high-performance vehicles to enhance durability and reduce weight.
In summary, the HIP heat treatment process is a powerful method for improving the physical properties of materials. By combining high temperature and high pressure in a controlled environment, HIP effectively eliminates defects and enhances the strength and durability of a wide range of materials, making it an essential process in many high-tech industries.
Summary Table:
Aspect | Details |
---|---|
Process Overview | Combines high temperature and pressure to enhance material properties. |
Key Components | Furnace (heats material), Pressure Vessel (withstands high pressure). |
Role of Argon Gas | Inert gas ensures no chemical changes; increases pressure for uniformity. |
Temperature Range | Varies from a few hundred to over 2000°C, depending on material. |
Cooling Process | Gradual cooling prevents thermal shock, ensuring material integrity. |
Benefits | Improved strength, durability, and defect elimination. |
Applications | Aerospace, medical devices, automotive industries. |
Discover how HIP heat treatment can revolutionize your material performance—contact our experts today!