Vacuum consumable electrode melting is a specialized metallurgical process used to produce high-purity metals and alloys. It involves melting a consumable electrode under vacuum conditions to refine the material and remove impurities. The process is particularly useful for materials that are highly reactive or require exceptional purity, such as titanium, zirconium, and superalloys. The key steps include electrode preparation, vacuum environment setup, melting, refining, and solidification. This method ensures minimal contamination, precise control over alloy composition, and superior material properties.
Key Points Explained:
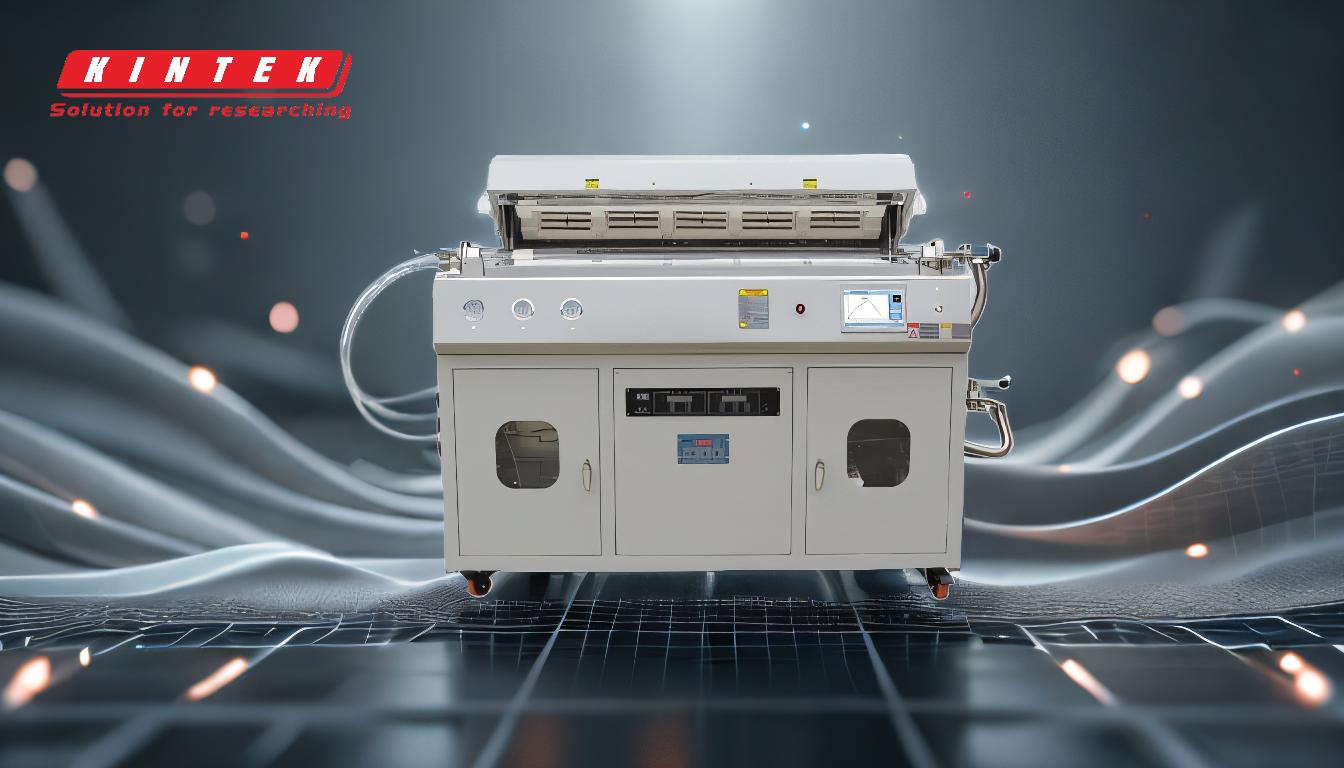
-
Electrode Preparation:
- The consumable electrode is typically made from the material to be melted and refined. It is carefully prepared to ensure uniformity and avoid contamination.
- The electrode is often pre-melted or sintered to achieve the desired shape and density, making it suitable for the vacuum melting process.
-
Vacuum Environment Setup:
- The melting process occurs in a vacuum chamber to prevent oxidation and contamination from atmospheric gases.
- Vacuum conditions are essential for removing volatile impurities and ensuring the purity of the final product. The vacuum also reduces heat loss and improves energy efficiency.
-
Melting Process:
- The consumable electrode is gradually melted using an electric arc or plasma arc. The heat generated by the arc melts the electrode, and the molten metal drips into a water-cooled copper crucible.
- The vacuum environment allows for the removal of gases like hydrogen, oxygen, and nitrogen, which can degrade the material's properties.
-
Refining:
- During melting, refining occurs as impurities are either vaporized or absorbed into the slag. The vacuum environment facilitates the removal of harmful elements such as sulfur and phosphorus.
- Alloying elements can be added at this stage to achieve the desired chemical composition.
-
Solidification:
- The molten metal solidifies in the crucible, forming an ingot. The controlled cooling rate ensures a uniform microstructure and minimizes defects like porosity or segregation.
- The resulting ingot is of high purity and has excellent mechanical properties, making it suitable for demanding applications in aerospace, medical, and energy industries.
-
Advantages of Vacuum Consumable Electrode Melting:
- High Purity: The vacuum environment prevents contamination and removes impurities, resulting in superior material quality.
- Precision Control: The process allows for precise control over alloy composition and microstructure.
- Environmental Benefits: Vacuum melting reduces emissions and waste compared to traditional melting methods.
- Versatility: The process is suitable for a wide range of reactive and refractory metals.
-
Applications:
- This process is widely used in industries requiring high-performance materials, such as aerospace (titanium alloys), medical (implants), and energy (superalloys for turbines).
- It is also employed in research and development to produce advanced materials with tailored properties.
By following these steps, vacuum consumable electrode melting ensures the production of high-quality, high-purity metals and alloys, meeting the stringent requirements of modern industries.
Summary Table:
Step | Description |
---|---|
Electrode Preparation | Prepare a uniform, contamination-free electrode, often pre-melted or sintered. |
Vacuum Setup | Create a vacuum environment to prevent oxidation and remove volatile impurities. |
Melting Process | Melt the electrode using an electric or plasma arc in a water-cooled crucible. |
Refining | Remove impurities and add alloying elements for desired composition. |
Solidification | Cool the molten metal to form a high-purity ingot with uniform microstructure. |
Advantages | High purity, precise control, environmental benefits, and versatility. |
Applications | Aerospace, medical implants, energy turbines, and advanced material research. |
Discover how vacuum consumable electrode melting can meet your high-purity metal needs—contact us today!