Vacuum melting, specifically through the vacuum induction melting (VIM) process, is a specialized technique used to melt and refine metals and alloys under vacuum conditions. This method is essential for materials that are highly reactive with oxygen, nitrogen, or other gases present in the atmosphere. The process involves placing metal raw materials in a crucible surrounded by an induction coil. When an alternating current passes through the coil, it generates eddy currents in the metal, causing it to heat up and melt. The vacuum environment ensures the removal of gas impurities, while electromagnetic stirring promotes uniform composition. The main stages of the process include charging, melting, refining, and pouring, all of which are carried out in a vacuum furnace designed to withstand high temperatures and vacuum conditions.
Key Points Explained:
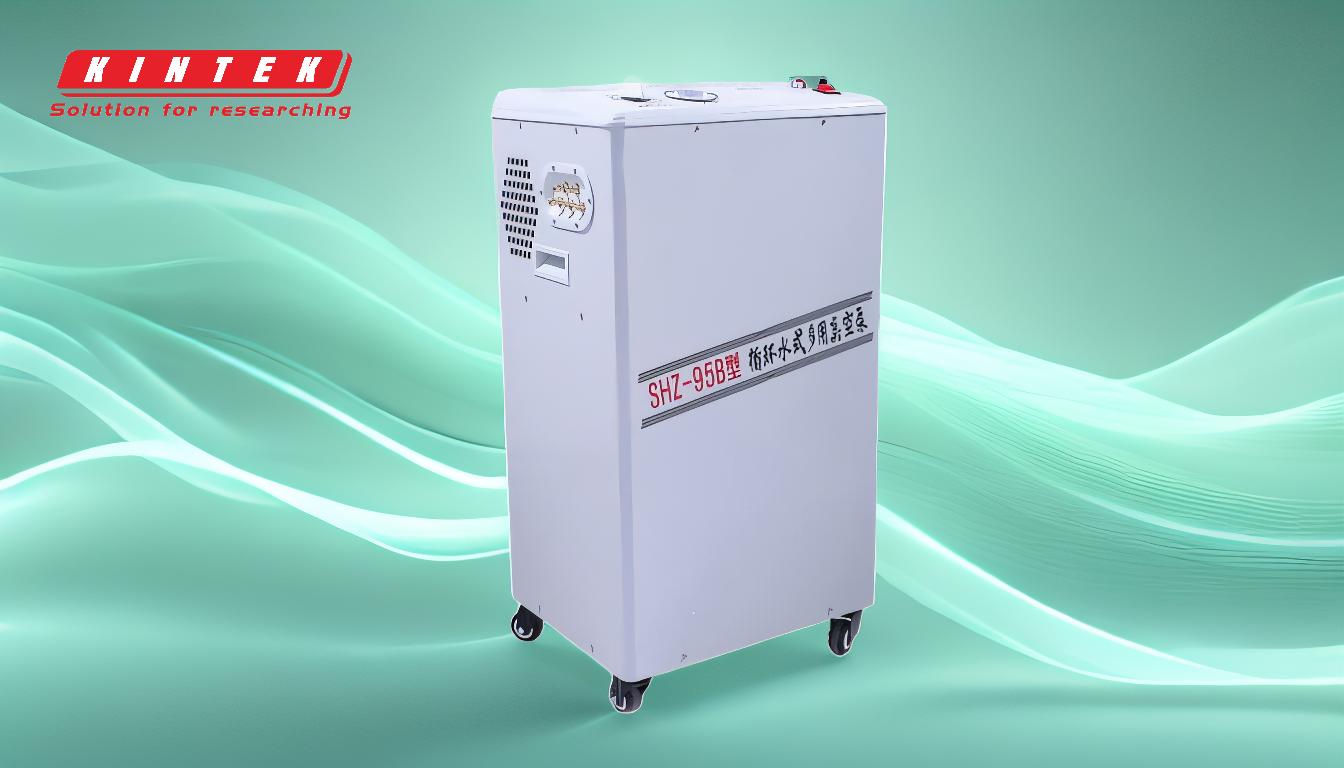
-
Crucible Selection and Preparation:
- The crucible is a critical component of the vacuum induction melting process. It must be made of refractory materials capable of withstanding extreme temperatures and chemical reactions with the molten metal.
- Proper preparation of the crucible ensures that it is free from contaminants that could affect the quality of the final product.
-
Charge Preparation:
- The charge consists of the raw materials to be melted, which can include metals, alloys, and additives.
- The materials are carefully selected and prepared to ensure they meet the required specifications for the final product.
-
Melting and Refining:
- The melting process begins when an alternating current is passed through the induction coil, generating eddy currents in the metal charge. These eddy currents cause the metal to heat up and eventually melt.
- The vacuum environment plays a crucial role in refining the molten metal by removing dissolved gases and impurities. This results in a cleaner, higher-quality metal.
- Electromagnetic stirring, induced by the alternating current, ensures a uniform composition throughout the molten metal.
-
Pouring:
- Once the metal has been melted and refined, it is poured into molds to form ingots or other desired shapes.
- The pouring process must be carefully controlled to ensure the metal fills the mold completely and solidifies with the desired properties.
-
Vacuum Furnace Components:
- The vacuum induction melting furnace is a complex system that includes several key components:
- Furnace Shell: Houses the melting chamber and is equipped with observation, temperature measurement, and charging devices.
- Inductor: The coil that generates the electromagnetic field necessary for induction heating.
- Crucible: Holds the metal charge and is lined with refractory materials.
- Tilting Mechanism: Allows the crucible to be tilted for pouring.
- Ingot Mold Mechanism: Used to shape the molten metal into ingots.
- Power Supply Device: Provides the alternating current needed for induction heating.
- Water Cooling System: Prevents the furnace components from overheating.
- The furnace is also equipped with a vacuum system to maintain the required vacuum conditions, a power supply system, and a control system to manage the entire process.
- The vacuum induction melting furnace is a complex system that includes several key components:
-
Batch Vacuum Induction Melting Furnace:
- In a batch vacuum induction melting furnace, the entire process—melting, refining, and pouring—occurs in a single chamber.
- After each cycle, the vacuum condition must be broken to remove the ingot mold, and the furnace must be refilled for the next cycle.
- This type of furnace is commonly used in industries that require high-purity metals and alloys, such as aerospace, automotive, and electronics.
-
Heating Mechanism:
- Heating in a vacuum furnace is primarily achieved through radiation. The workpieces must be properly spaced within the furnace to ensure even heating.
- The vacuum environment enhances the heating process by eliminating convective heat loss, allowing for more efficient and uniform heating.
-
Process Flow:
- The process flow of vacuum induction melting can be divided into four main stages:
- Charging: Loading the raw materials into the crucible.
- Melting: Heating the materials until they melt using electromagnetic induction.
- Refining: Removing impurities and gases under vacuum conditions.
- Pouring: Transferring the molten metal into molds to form the final product.
- The process flow of vacuum induction melting can be divided into four main stages:
In summary, the vacuum induction melting process is a sophisticated method for producing high-quality metals and alloys. It leverages the principles of electromagnetic induction and vacuum technology to achieve precise control over the melting and refining processes. The use of a vacuum furnace ensures that the final product is free from impurities and has a uniform composition, making it ideal for applications that demand high-performance materials.
Summary Table:
Stage | Description |
---|---|
Charging | Loading raw materials (metals, alloys, additives) into the crucible. |
Melting | Heating materials using electromagnetic induction until they melt. |
Refining | Removing impurities and gases under vacuum for cleaner, higher-quality metal. |
Pouring | Transferring molten metal into molds to form ingots or desired shapes. |
Ready to achieve high-purity metal production? Contact our experts today to learn more about vacuum induction melting!