A protective atmosphere in heat treatment refers to a controlled environment of gases that shields the metal from harmful chemical reactions, such as oxidation or decarburization, during heating and cooling processes. This environment is critical for maintaining the integrity and desired properties of the metal, ensuring high-quality outcomes. Protective atmospheres are used in various heat treatment processes, including sintering, hot isostatic pressing (HIP), and vacuum operations. They are particularly important in industries like automotive, chemical, and nuclear power, where contamination or surface reactions can lead to rejected parts, financial losses, and safety risks. By preventing oxidation and contamination, a protective atmosphere ensures that the metal retains its strength, ductility, and dimensional stability.
Key Points Explained:
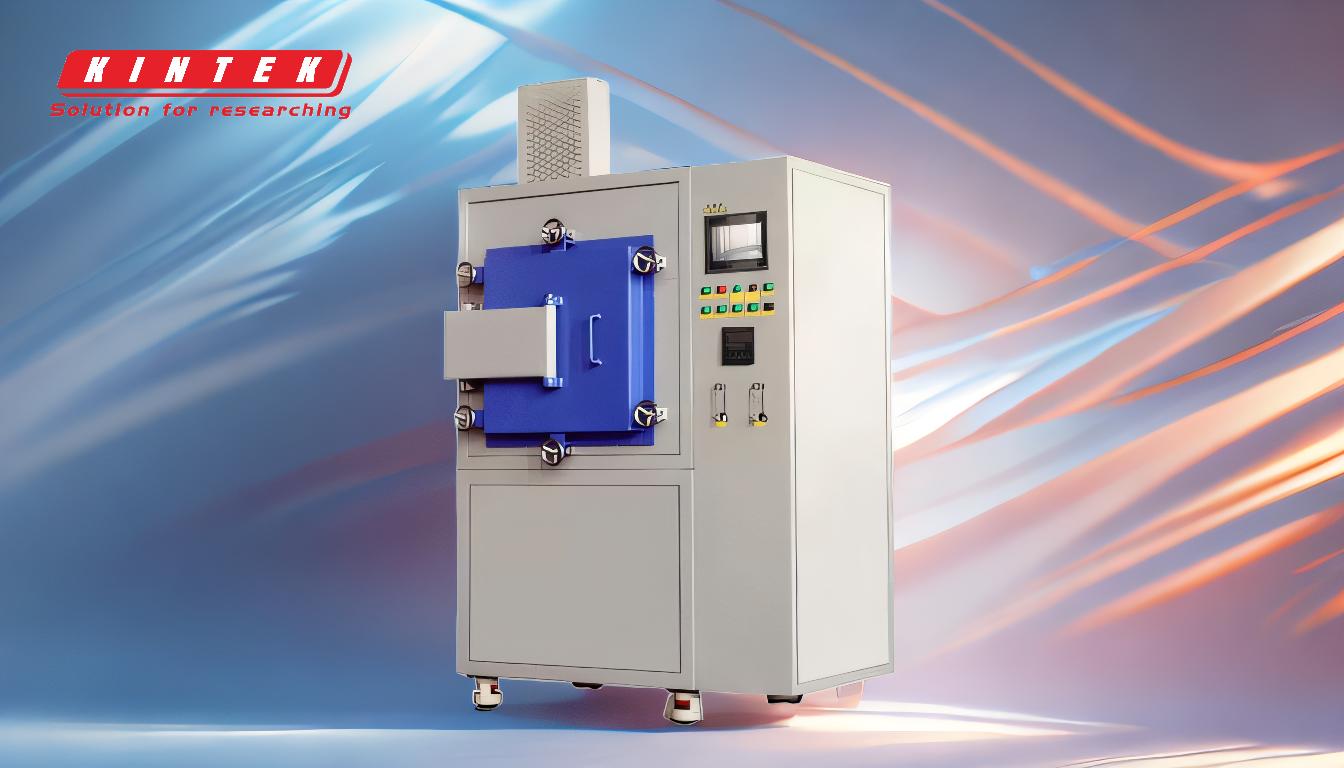
-
Definition and Purpose of Protective Atmosphere
- A protective atmosphere is a controlled gas environment used during heat treatment to prevent unwanted chemical reactions on the metal's surface.
- Its primary purpose is to shield the metal from oxidation, decarburization, and contamination, ensuring the material retains its desired properties.
- This is especially critical for expensive or high-performance parts, as surface reactions can compromise quality and lead to costly rejections.
-
Common Types of Protective Atmospheres
- Inert Gases: Gases like argon and nitrogen are commonly used because they do not react with the metal, preventing oxidation and contamination.
- Vacuum Environments: In some cases, a vacuum furnace is used to eliminate any reactive gases, creating an oxygen-free environment.
- Modified Atmospheres: These are tailored gas mixtures designed to achieve specific outcomes, such as preventing decarburization or enhancing surface properties.
-
Importance in Heat Treatment Processes
- Preventing Oxidation: Exposure to air during heat treatment can cause oxidation, which ruins the part's surface and compromises its performance. A protective atmosphere ensures the metal remains oxidation-free.
- Avoiding Decarburization: Decarburization, the loss of carbon from the surface of steel, weakens the material. A controlled atmosphere prevents this by maintaining the carbon content.
- Ensuring Dimensional Stability: By preventing surface reactions, the protective atmosphere helps maintain the part's dimensional accuracy and mechanical properties.
-
Applications in Key Industries
- Automotive: Heat-treated components like gears and crankshafts require precise control of surface properties to ensure durability and performance.
- Aerospace: High-performance alloys used in aerospace applications must maintain their strength and resistance to fatigue, which is achieved through protective atmospheres.
- Nuclear Power: In extreme environments, materials must resist corrosion and maintain structural integrity, making protective atmospheres essential.
-
Consequences of Poor Atmosphere Control
- Contamination: Without a protective atmosphere, reactive gases can contaminate the metal, leading to increased brittleness, corrosion, and other forms of damage.
- Rejected Parts: Contaminated or oxidized parts often fail quality checks, resulting in financial losses and wasted time.
- Safety Risks: In industries like nuclear power or aerospace, compromised materials can lead to catastrophic failures, posing significant safety risks.
-
Technological and Operational Considerations
- Furnace Design: Heat treatment furnaces must be tightly sealed to maintain the protective atmosphere and prevent external interference.
- Gas Composition Control: Precise control of gas mixtures is necessary to achieve the desired outcomes, such as preventing oxidation or enhancing surface properties.
- Process Monitoring: Advanced monitoring systems ensure that the protective atmosphere remains consistent throughout the heat treatment process.
By understanding and implementing protective atmospheres in heat treatment, manufacturers can ensure high-quality outcomes, reduce waste, and meet the stringent demands of modern industries.
Summary Table:
Aspect | Details |
---|---|
Purpose | Prevents oxidation, decarburization, and contamination during heat treatment. |
Common Types | Inert gases (argon, nitrogen), vacuum environments, modified gas mixtures. |
Key Benefits | Maintains strength, ductility, and dimensional stability of metals. |
Applications | Automotive, aerospace, nuclear power, and chemical industries. |
Consequences of Failure | Contamination, rejected parts, financial losses, and safety risks. |
Operational Considerations | Tight furnace sealing, precise gas control, and advanced monitoring. |
Ensure your heat treatment processes deliver top-quality results—contact our experts today to learn more!