Heat treatment furnaces are specialized heating chambers designed to hold and heat steel or other materials to achieve specific material properties. Their primary purpose is to provide a controlled environment for precise and consistent heat treatment processes, including uniform heating, precise temperature regulation, and controlled cooling rates. This ensures that materials, particularly steel components, achieve desired properties such as improved mechanical strength, durability, and reproducibility. Heat treatment furnaces are essential in industries where material performance and reliability are critical, enabling the transformation of raw materials into high-quality, functional products.
Key Points Explained:
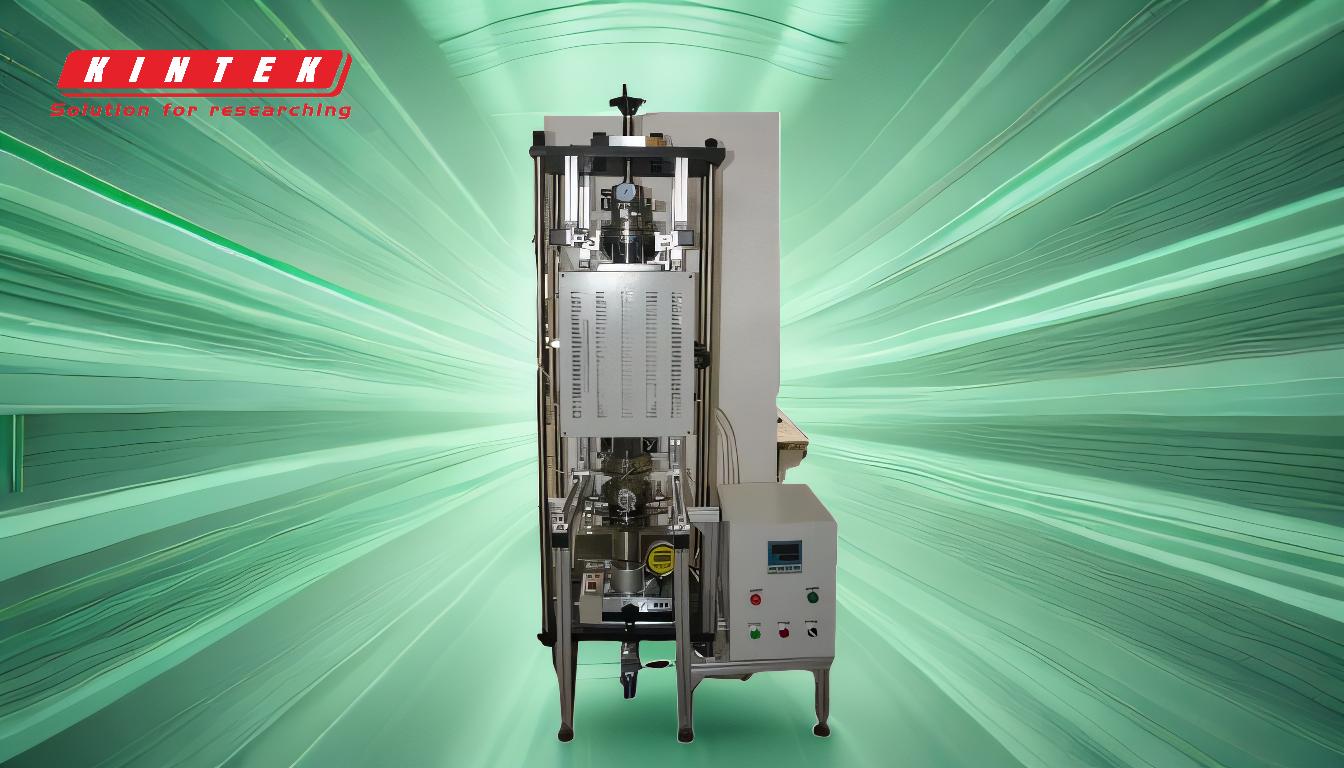
-
Controlled Heating Environment:
- Heat treatment furnaces create a controlled environment where materials, especially steel, can be heated uniformly and consistently.
- This controlled environment ensures that the material is exposed to precise temperatures, which is critical for achieving specific mechanical and physical properties.
-
Regulation of Heat Supply:
- The furnaces regulate heat supply based on the specific requirements of the material and the desired outcome.
- This regulation allows for reproducible results, ensuring that each batch of material undergoes the same treatment process, leading to consistent quality.
-
Uniform Heating and Temperature Control:
- Uniform heating is essential to avoid uneven material properties, which can lead to weak spots or failures in the final product.
- Precise temperature control ensures that the material reaches the exact temperature needed for the desired transformation, whether it’s hardening, annealing, or tempering.
-
Controlled Cooling Rates:
- After heating, controlled cooling is crucial to achieve the desired material properties. Different cooling rates can result in different microstructures and mechanical properties.
- The furnace ensures that cooling is done in a controlled manner, preventing issues like cracking or warping.
-
Imparting Reproducible and Useful Properties:
- The primary goal of heat treatment furnaces is to impart reproducible and useful properties to materials. These properties include increased hardness, improved strength, enhanced durability, and better wear resistance.
- By achieving these properties, the material becomes more suitable for specific applications, such as in automotive, aerospace, or construction industries.
-
Transformation of Raw Materials:
- Heat treatment furnaces play a pivotal role in transforming raw materials into high-performance products. For example, steel can be transformed from a soft, malleable state to a hard, durable state suitable for tools or machinery.
- This transformation is essential for creating products that meet stringent performance and safety standards.
-
Applications in Various Industries:
- Heat treatment furnaces are used in a wide range of industries, including automotive, aerospace, manufacturing, and construction.
- In these industries, the furnaces are used to treat components such as gears, shafts, bearings, and structural parts, ensuring they meet the required specifications and performance criteria.
-
Enhancing Mechanical Properties:
- Heat treatment processes, facilitated by these furnaces, enhance mechanical properties such as tensile strength, toughness, and fatigue resistance.
- These enhancements are critical for components that are subjected to high stress, wear, or extreme conditions during their service life.
In summary, heat treatment furnaces are essential tools in material science and engineering, enabling the precise control of heating and cooling processes to achieve desired material properties. Their ability to provide a controlled environment, regulate heat supply, and ensure uniform heating and cooling makes them indispensable in producing high-quality, reliable materials and components for various industrial applications.
Summary Table:
Key Feature | Description |
---|---|
Controlled Heating Environment | Ensures uniform and consistent heating for precise material properties. |
Regulation of Heat Supply | Adjusts heat based on material requirements for reproducible results. |
Uniform Heating & Temperature | Prevents weak spots by maintaining exact temperatures for hardening or tempering. |
Controlled Cooling Rates | Achieves desired material properties by preventing cracking or warping. |
Reproducible Properties | Imparts hardness, strength, durability, and wear resistance to materials. |
Transformation of Raw Materials | Converts raw materials into high-performance products for industrial use. |
Industry Applications | Used in automotive, aerospace, manufacturing, and construction industries. |
Enhanced Mechanical Properties | Improves tensile strength, toughness, and fatigue resistance. |
Discover how heat treatment furnaces can optimize your material processes—contact us today for expert advice!