Physical Vapor Deposition (PVD) coating is a sophisticated thin film deposition technique used to apply a thin layer of material onto a substrate in a vacuum environment. This process involves vaporizing a solid material, which then condenses onto the target surface, forming a highly durable and functional coating. PVD coatings are known for their excellent mechanical, chemical, and optical properties, making them ideal for applications requiring high durability, corrosion resistance, and aesthetic appeal. The process is carried out at relatively low temperatures, minimizing distortion and making it suitable for a wide range of materials, including metals, ceramics, and plastics.
Key Points Explained:
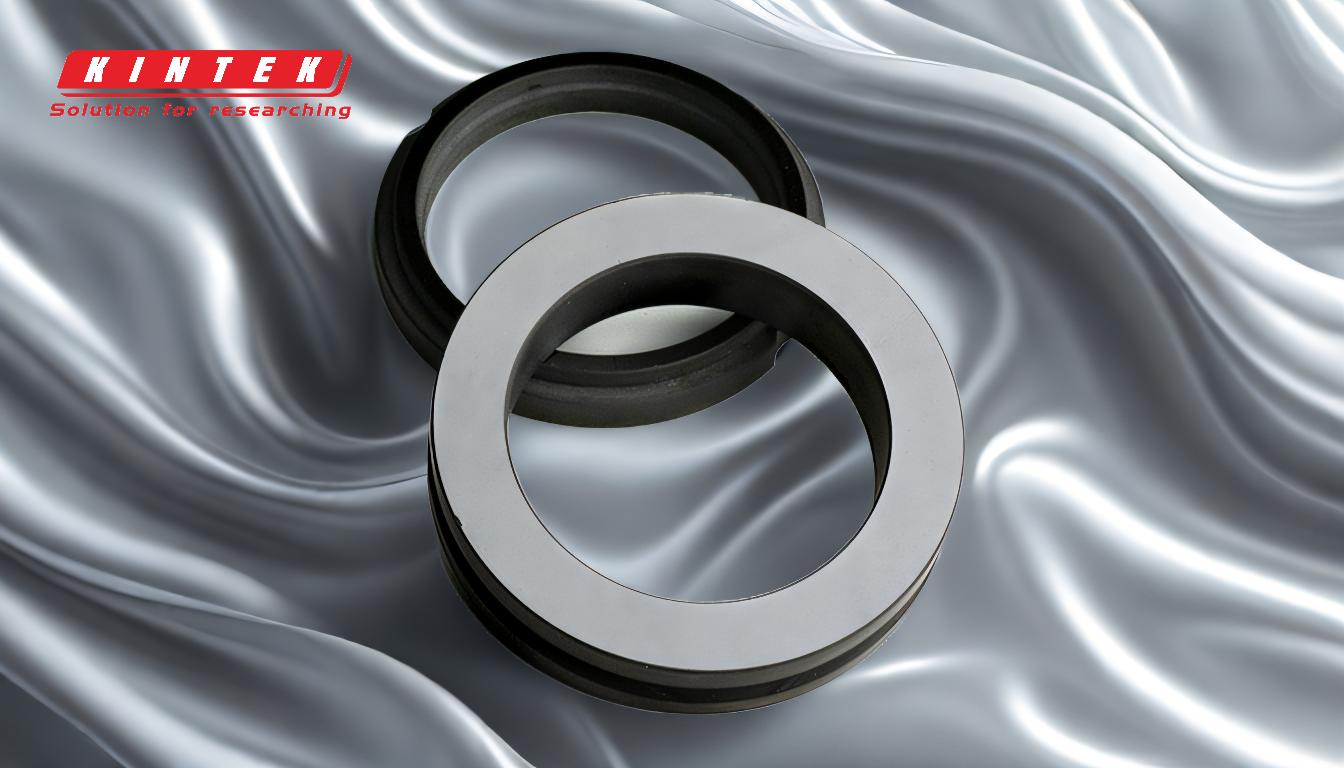
-
Definition and Basic Process:
- PVD stands for Physical Vapor Deposition, a technique where a solid material is vaporized in a vacuum and then deposited onto a substrate.
- The process involves three critical steps: Evaporation, Transportation, and Condensation.
- The vaporized material forms a thin film on the substrate, which can be a pure material or an alloy composition.
-
Vacuum Environment:
- The entire process occurs in a vacuum chamber, typically at pressures ranging from 10^-3 to 10^-9 Torr.
- The vacuum environment ensures that the vaporized material remains clean and uncontaminated, leading to high-quality coatings.
-
Vaporization Techniques:
- Various methods are used to vaporize the solid material, including:
- Heated Crucible: The material is heated until it vaporizes.
- Electron Beam: A focused electron beam is used to vaporize the material.
- Ion Bombardment: High-energy ions are used to sputter the material.
- Cathodic Arc: An electric arc is used to vaporize the material from a cathode.
- Various methods are used to vaporize the solid material, including:
-
Reactive Gases:
- Reactive gases, such as nitrogen, can be introduced into the vacuum chamber to modify the composition of the vaporized material.
- For example, adding nitrogen can result in the formation of a metal nitride, which enhances the coating's properties.
-
Deposition Process:
- The vaporized atoms travel through the vacuum and embed themselves into the surface of the substrate.
- The process is a 'line of sight' technique, meaning that the object must be properly positioned or rotated to ensure complete and uniform coating.
-
Coating Characteristics:
- PVD coatings are typically very thin, with thicknesses ranging from 0.02 to 5 microns.
- The coatings are highly durable, resistant to corrosion, and can withstand high temperatures.
- They improve the appearance, durability, and functionality of the coated parts.
-
Advantages of PVD Coating:
- Lower Process Temperatures: PVD is performed at temperatures between 50°C and 600°C, which minimizes distortion in most materials.
- Accurate Deposition: The process allows for precise control over the thickness and composition of the coating.
- Environmentally Friendly: PVD is considered more eco-friendly compared to other coating techniques like Chemical Vapor Deposition (CVD).
-
Applications:
- PVD coatings are widely used in various industries, including:
- Cutting Tools: High-speed steel (HSS) and carbide cutting tools benefit from the enhanced durability and wear resistance.
- Plastic Injection Molding: Components with tight tolerances are coated to improve performance and longevity.
- Fine Blanking Tools: PVD coatings enhance the wear resistance and lifespan of these tools.
- Optical Coatings: The technique is used to apply coatings that improve the optical properties of lenses and other components.
- PVD coatings are widely used in various industries, including:
-
Material Options:
- Common materials used in PVD coatings include titanium, zirconium, and chromium.
- These materials can be combined with reactive gases to form compounds like titanium nitride (TiN), which are known for their hardness and wear resistance.
-
Environmental and Safety Considerations:
- PVD coating is considered a modern and environmentally friendly process.
- The use of vacuum technology and the absence of harmful chemicals make it a safer alternative to other coating methods.
In summary, PVD coating is a versatile and advanced technique that offers numerous benefits, including high durability, precision, and environmental friendliness. Its applications span across various industries, making it a valuable process for enhancing the performance and longevity of a wide range of components.
Summary Table:
Aspect | Details |
---|---|
Definition | Thin film deposition technique in a vacuum environment. |
Process Steps | Evaporation, Transportation, Condensation. |
Vaporization Methods | Heated Crucible, Electron Beam, Ion Bombardment, Cathodic Arc. |
Coating Thickness | 0.02 to 5 microns. |
Advantages | High durability, corrosion resistance, low process temperatures, eco-friendly. |
Applications | Cutting tools, plastic injection molding, fine blanking tools, optics. |
Materials Used | Titanium, zirconium, chromium, and compounds like TiN. |
Interested in enhancing your components with PVD coating? Contact us today to learn more!