The sintering process in manufacturing is a method used to create strong, precise, and complex components by compacting and heating powdered materials without melting them. This process enhances mechanical properties such as hardness, toughness, and abrasion resistance, while also reducing porosity and improving electrical and thermal conductivity. Sintering is widely used in metal manufacturing, ceramics, and glass production, offering flexibility and cost-effectiveness compared to traditional methods like casting or forging. By avoiding solid-liquid phase changes, sintering allows the creation of components from materials with high melting points, making it a versatile and essential technique in modern manufacturing.
Key Points Explained:
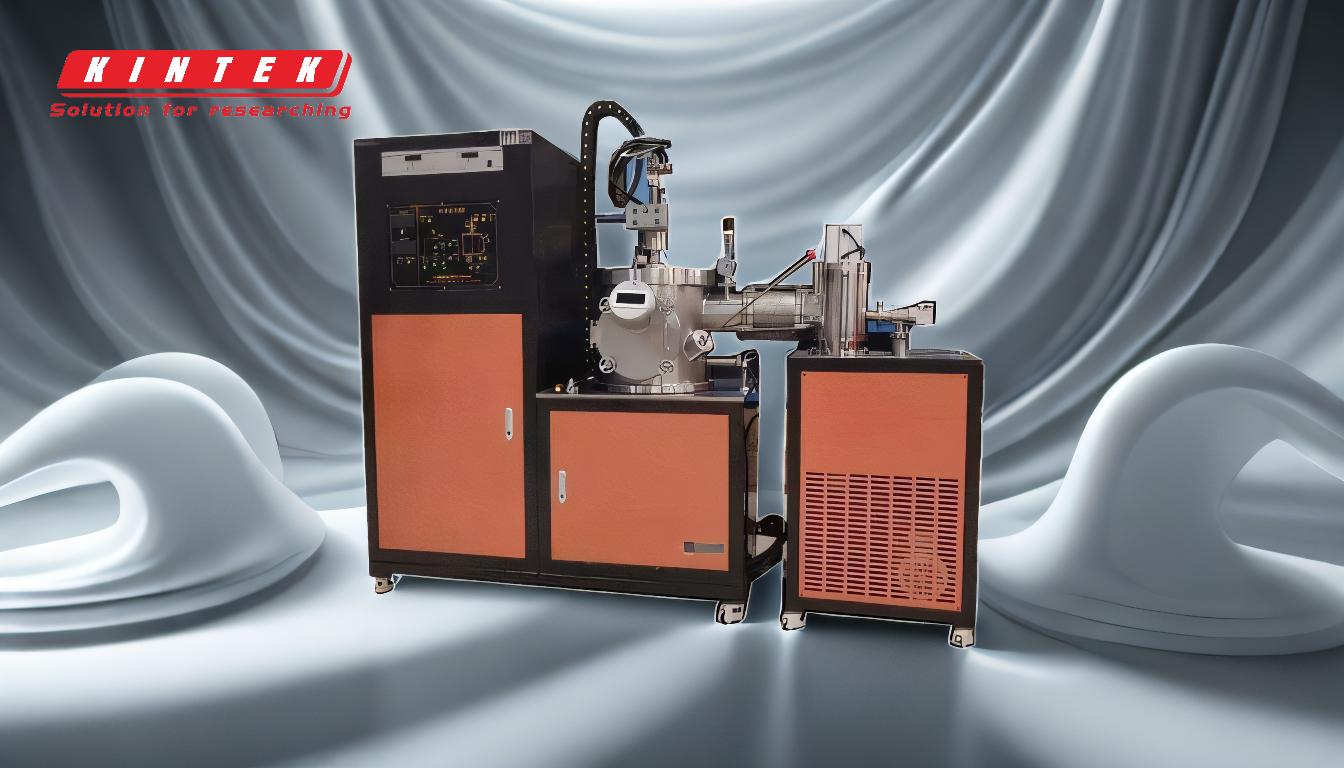
-
Definition and Purpose of Sintering:
- Sintering is a manufacturing process that uses heat and pressure to compact powdered materials into solid components without melting them.
- The primary purpose is to enhance mechanical properties such as hardness, toughness, and abrasion resistance, while also reducing porosity and improving electrical and thermal conductivity.
-
Materials Used in Sintering:
- Sintering is commonly applied to metals, ceramics, and glass.
- In metal manufacturing, powdered iron mixed with coke is often used. The process involves igniting the mixture to generate high heat, causing the particles to form lumps suitable for further processing in blast furnaces.
-
Process Mechanics:
- The sintering process begins with the compaction of powdered materials into a desired shape.
- Heat is then applied, often through a combustion reaction initiated by a gas burner and air flow, to fuse the particles together.
- The process avoids melting the materials, instead relying on diffusion to bond the particles at a microscopic level.
-
Advantages of Sintering:
- Complex Geometries: Sintering allows for the creation of intricate shapes and geometries that are difficult to achieve with traditional manufacturing methods.
- Cost-Effectiveness: Lower tooling costs and the ability to mass-produce components with high precision and repeatability.
- Material Flexibility: Enables the use of materials with high melting points, as the process does not require melting.
- Enhanced Properties: Improves mechanical, electrical, and thermal properties of the final product.
-
Applications in Various Industries:
- Metal Manufacturing: Used to produce structural steel parts, porous metals, and magnetic materials.
- Ceramics and Glass: Important in the manufacture of high-strength and high-precision ceramic and glass components.
- High-Tech Materials: Used to create advanced materials with specific properties, such as enhanced electrical conductivity or thermal insulation.
-
Comparison with Traditional Manufacturing Methods:
- Flexibility: Sintering is more flexible than casting, forging, and extrusion, as it does not require solid-liquid phase changes.
- Material Integrity: Allows the creation of components from materials that would otherwise decompose or degrade during traditional manufacturing processes.
-
Key Benefits for Equipment and Consumable Purchasers:
- Precision and Repeatability: Ensures consistent quality and performance of manufactured components.
- Cost Savings: Reduces tooling and production costs, making it an economical choice for mass production.
- Versatility: Suitable for a wide range of materials and applications, providing flexibility in product design and manufacturing.
By understanding the sintering process, manufacturers and purchasers can make informed decisions about the production and selection of components, ensuring optimal performance and cost-efficiency in their operations.
Summary Table:
Key Aspect | Details |
---|---|
Definition | Compacting and heating powdered materials without melting. |
Purpose | Enhances hardness, toughness, abrasion resistance, and conductivity. |
Materials | Metals, ceramics, and glass. |
Process Mechanics | Compaction + heat application via diffusion bonding. |
Advantages | Complex geometries, cost-effectiveness, material flexibility, enhanced properties. |
Applications | Metal manufacturing, ceramics, glass, high-tech materials. |
Benefits for Purchasers | Precision, repeatability, cost savings, and versatility. |
Unlock the potential of sintering for your manufacturing needs—contact our experts today!