The sintering process of hot pressing combines the principles of pressure and heat to densify powdered materials into a solid structure. It begins with the preparation of powdered raw materials, which are then compacted under high pressure to form a "green" part. This part is then subjected to controlled heating in a sintering furnace, where temperatures are maintained just below the material's melting point to facilitate particle bonding through diffusion. The process results in densification, neck formation, and the creation of a cohesive, rigid structure. Hot pressing enhances the sintering process by applying continuous pressure during heating, which accelerates particle bonding and reduces porosity, leading to stronger and more durable final products.
Key Points Explained:
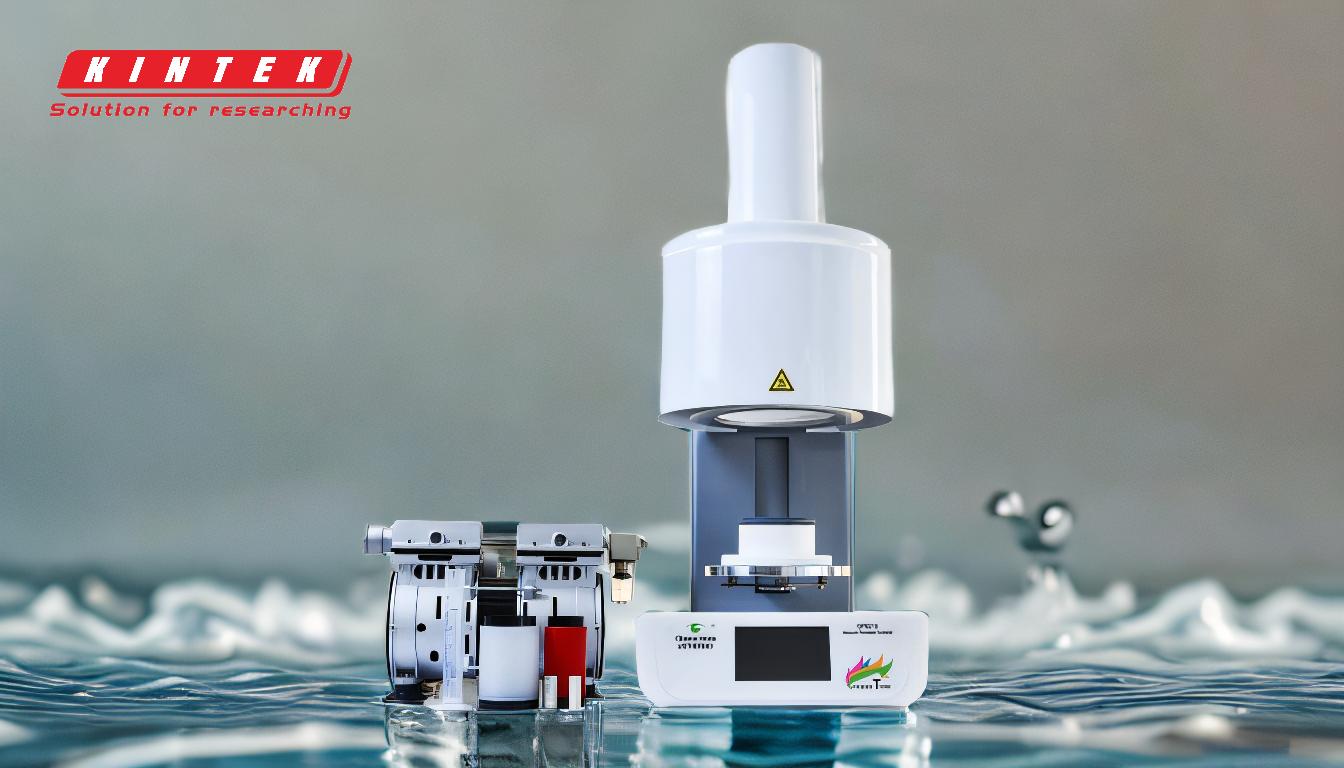
-
Preparation of Powdered Materials:
- The process begins with the selection and preparation of powdered raw materials, which may include metals like iron, nickel, molybdenum, or copper, as well as alloying elements and lubricants.
- The powder is carefully chosen based on the desired properties of the final product, such as strength, hardness, or corrosion resistance.
-
Compaction Under Pressure:
- The powdered material is compacted under high pressure using a mold or die to form a "green" part. This step ensures uniformity and eliminates voids, giving the part its initial shape and strength.
- The compaction process is critical for achieving a consistent density and structure in the final product.
-
Heating in a Sintering Furnace:
- The compacted part is placed in a sintering furnace, where it is heated to a temperature just below the material's melting point. This controlled heating facilitates particle bonding through diffusion without causing complete melting.
- During this stage, particles undergo neck formation and densification, leading to a reduction in porosity and an increase in structural integrity.
-
Application of Pressure During Heating (Hot Pressing):
- In hot pressing, continuous pressure is applied to the material during the heating process. This additional pressure accelerates particle bonding and further reduces porosity, resulting in a denser and stronger final product.
- Hot pressing is particularly effective for materials that require high density and minimal defects.
-
Cooling and Solidification:
- After the sintering process, the material is allowed to cool gradually. This cooling stage ensures that the sintered product solidifies into a rigid and cohesive structure.
- Proper cooling is essential to prevent cracking or warping and to achieve the desired mechanical properties.
-
Stages of Sintering:
- The sintering process can be broken down into several stages, including the removal of lubricants, reduction of oxides, bonding of particles, and cooling.
- Each stage plays a crucial role in determining the final properties of the sintered product, such as its strength, hardness, and dimensional accuracy.
-
Materials Used in Sintering:
- A wide range of materials can be sintered, including stainless steel, aluminum, nickel, copper, and titanium alloys. These materials are often refined and improved through advancements in sintering technologies.
- The choice of material depends on the specific application and the desired characteristics of the final product.
-
Advantages of Hot Pressing:
- Hot pressing offers several advantages over conventional sintering, including faster densification, reduced porosity, and improved mechanical properties.
- This method is particularly useful for producing high-performance components in industries such as aerospace, automotive, and electronics.
By combining pressure and heat, the hot pressing sintering process produces materials with superior density, strength, and durability, making it a valuable technique for manufacturing high-quality components.
Summary Table:
Key Stage | Description |
---|---|
Preparation of Powder | Select and prepare powdered materials (e.g., metals, alloys, lubricants). |
Compaction | Compact powder under high pressure to form a "green" part. |
Heating in Sintering Furnace | Heat just below melting point to bond particles through diffusion. |
Hot Pressing | Apply continuous pressure during heating for faster densification. |
Cooling | Gradual cooling to solidify the material into a rigid, cohesive structure. |
Materials Used | Stainless steel, aluminum, nickel, copper, titanium alloys, and more. |
Advantages | Faster densification, reduced porosity, and improved mechanical properties. |
Discover how hot pressing sintering can enhance your material production—contact our experts today!