The standard thickness of plating typically ranges from 0.0005 inch to 0.0015 inch (0.012 mm to 0.038 mm) for engineering applications. This thickness range is often chosen to balance durability, functionality, and cost-effectiveness. Additionally, the hardness of the plating can vary between 48 to 52 Rockwell C, but when heat-treated at approximately 750°F (400°C) for one hour, the hardness can increase significantly to 58 to 64 Rockwell C. This heat treatment process enhances the mechanical properties of the plating, making it more suitable for demanding applications.
Key Points Explained:
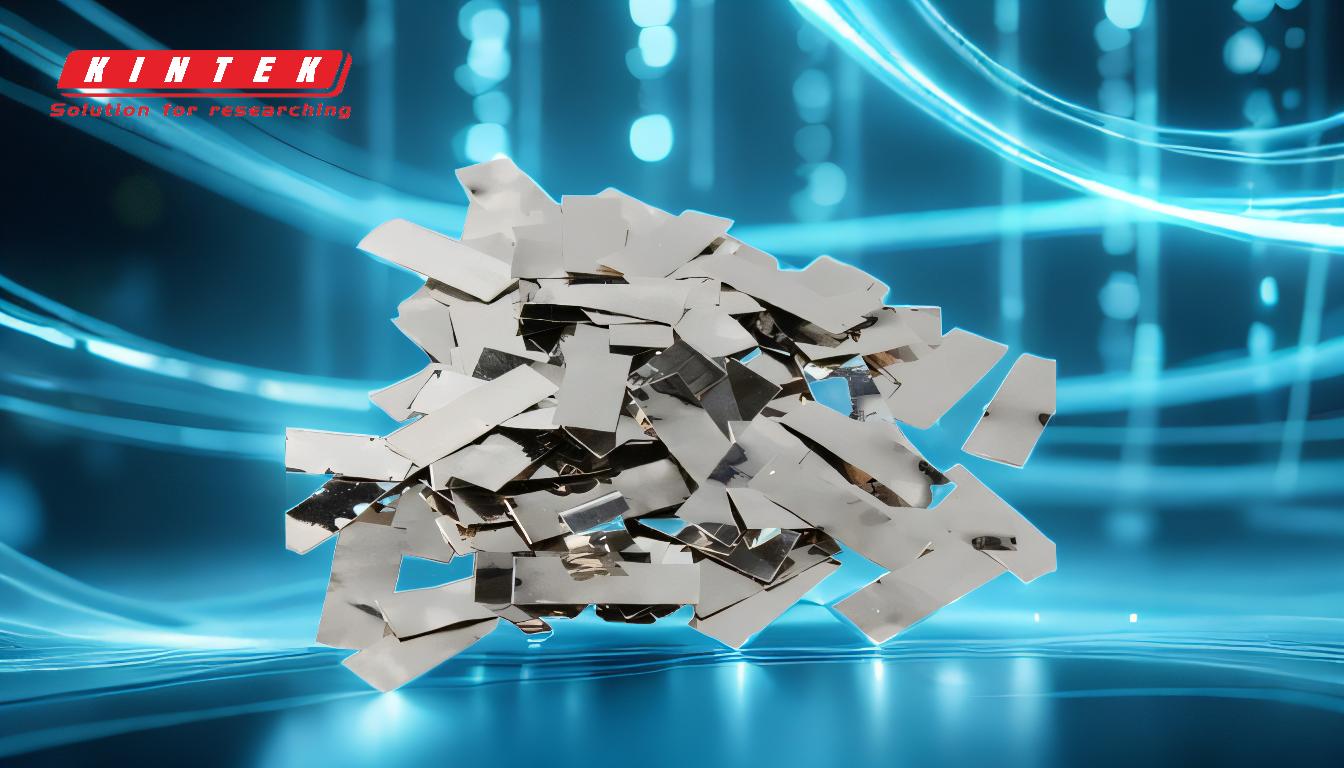
-
Standard Thickness Range:
- The typical thickness for plating in engineering applications is 0.0005 inch to 0.0015 inch (0.012 mm to 0.038 mm). This range is widely accepted as it provides adequate protection and performance for most industrial uses.
- Thinner coatings (closer to 0.0005 inch) are often used for applications where minimal material addition is required, while thicker coatings (up to 0.0015 inch) are chosen for more demanding environments.
-
Hardness of Plating:
- The hardness of the plating material typically ranges from 48 to 52 Rockwell C in its untreated state. This level of hardness is sufficient for many general-purpose applications.
- Hardness is a critical factor because it determines the plating's resistance to wear, abrasion, and deformation, which are essential for components subjected to mechanical stress.
-
Heat Treatment and Enhanced Hardness:
- When the plating is heat-treated at 750°F (400°C) for one hour, its hardness can increase significantly to 58 to 64 Rockwell C.
- Heat treatment alters the microstructure of the plating, improving its mechanical properties such as hardness, wear resistance, and durability. This makes it suitable for more severe operating conditions, such as high-stress or high-temperature environments.
-
Application Considerations:
- The choice of plating thickness and hardness depends on the specific application requirements. For example:
- Thinner coatings are often used in electronics or precision components where dimensional accuracy is critical.
- Thicker coatings are preferred for heavy machinery or automotive parts exposed to harsh conditions.
- Heat-treated plating is ideal for applications requiring enhanced wear resistance, such as cutting tools or industrial equipment.
- The choice of plating thickness and hardness depends on the specific application requirements. For example:
-
Cost and Performance Trade-offs:
- Thicker plating and heat treatment processes increase material and processing costs. Therefore, the selection of plating thickness and hardness should balance performance requirements with budget constraints.
- For cost-sensitive applications, untreated plating with standard thickness may suffice, while high-performance applications may justify the additional expense of heat treatment.
By understanding these key points, equipment and consumable purchasers can make informed decisions about plating specifications to meet their specific needs.
Summary Table:
Parameter | Details |
---|---|
Standard Thickness | 0.0005 inch to 0.0015 inch (0.012 mm to 0.038 mm) |
Untreated Hardness | 48 to 52 Rockwell C |
Heat-Treated Hardness | 58 to 64 Rockwell C (after heat treatment at 750°F/400°C for 1 hour) |
Applications | Electronics, precision components, heavy machinery, automotive parts |
Cost Considerations | Thicker plating and heat treatment increase costs but enhance performance. |
Need help selecting the right plating for your application? Contact our experts today for tailored solutions!