A vacuum furnace is a specialized piece of equipment used for high-temperature processes in a vacuum environment, ensuring minimal contamination and precise thermal control. The temperature of a vacuum furnace can vary significantly depending on its design, application, and process requirements. Typically, the heating temperature ranges from 800°C to 2400°C, with specific programs often involving gradual temperature increases and holds at critical points. For instance, a program might start at 800°C, hold for 20 minutes, then gradually increase to 1100°C over an hour, followed by a 1.5-hour hold. Temperature control is critical and relies on thermocouples and advanced control systems like PID, touch screen, or PLC automation. Uniformity and stability are influenced by factors such as insulation design, gas flow patterns, and the number of heating zones.
Key Points Explained:
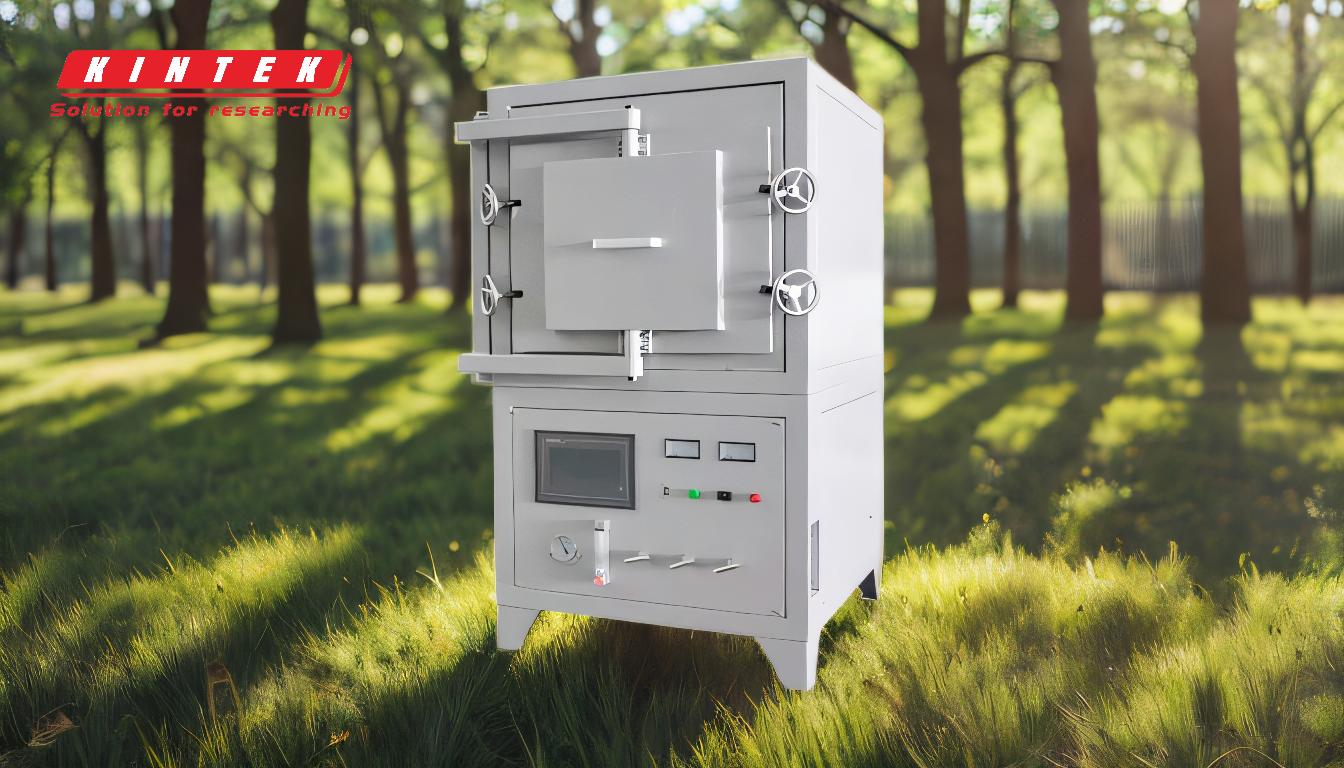
-
Typical Temperature Range of a Vacuum Furnace:
- The heating temperature of a vacuum furnace typically ranges between 1600°C and 2400°C, depending on the application.
- For specific processes, such as those in dental or industrial settings, temperatures may start lower (e.g., 800°C) and gradually increase to higher levels (e.g., 1100°C) to ensure proper material treatment.
-
Temperature Control Systems:
- The temperature control system in a vacuum furnace includes thermocouples for accurate temperature measurement and temperature controllers for precise regulation.
- Advanced systems like PID programmable control, touch screen control, and PLC fully automatic control ensure consistent and reliable temperature management.
-
Temperature Uniformity and Stability:
- Uniformity is influenced by factors such as insulation design, gas flow patterns, and the presence of openings or gaps in the hot zone.
- A minimum of three heating zones is recommended for proper power input trimming and adjustment, ensuring even heat distribution.
-
Common Temperature Control Failures:
- Failures can occur due to thermocouple wire disconnection or contamination, temperature control instrument failure, or reverse connection/short circuit of thermocouple compensation leads.
- Regular maintenance and calibration are essential to prevent these issues.
-
Process-Specific Temperature Programs:
- In many applications, temperature programs are designed with gradual increases and hold times to achieve optimal results.
- For example, a program might involve raising the temperature to 800°C, holding for 20 minutes, then slowly increasing to 1100°C over an hour, followed by a 1.5-hour hold.
-
Influences on Temperature Control:
- Over time, temperature control can be affected by chemical and physical influences, such as soiling or deposits from materials like ceramics, alloys, and soldering materials.
- Proper cleaning and maintenance of the furnace interior are necessary to maintain consistent performance.
-
Importance of Selecting the Right Temperature Range:
- The temperature range must align with the specific process requirements of the application, whether it involves sintering, brazing, annealing, or other thermal treatments.
- Choosing the appropriate range ensures optimal material properties and process efficiency.
By understanding these key points, equipment and consumable purchasers can make informed decisions when selecting and operating a vacuum furnace, ensuring it meets their specific thermal processing needs.
Summary Table:
Aspect | Details |
---|---|
Typical Temperature Range | 800°C to 2400°C, depending on application |
Control Systems | Thermocouples, PID, touch screen, or PLC automation |
Uniformity & Stability | Influenced by insulation, gas flow, and heating zones (minimum 3 zones) |
Common Failures | Thermocouple disconnection, contamination, or control system malfunctions |
Process-Specific Programs | Gradual increases and holds (e.g., 800°C to 1100°C with timed holds) |
Maintenance Needs | Regular cleaning and calibration to prevent performance degradation |
Key Application Range | Sintering, brazing, annealing, and other high-temperature processes |
Need a vacuum furnace tailored to your thermal processing needs? Contact us today for expert guidance!