Activated carbon regeneration typically involves heating the material to around 1000°F (538°C) to volatilize 75–90% of the adsorbed contaminants. Steam is then introduced to remove the remaining volatiles and fully reactivate the carbon, restoring its adsorption capacity for reuse. This process ensures the carbon is nearly completely restored, making it an efficient and sustainable method for recycling activated carbon in various industrial applications.
Key Points Explained:
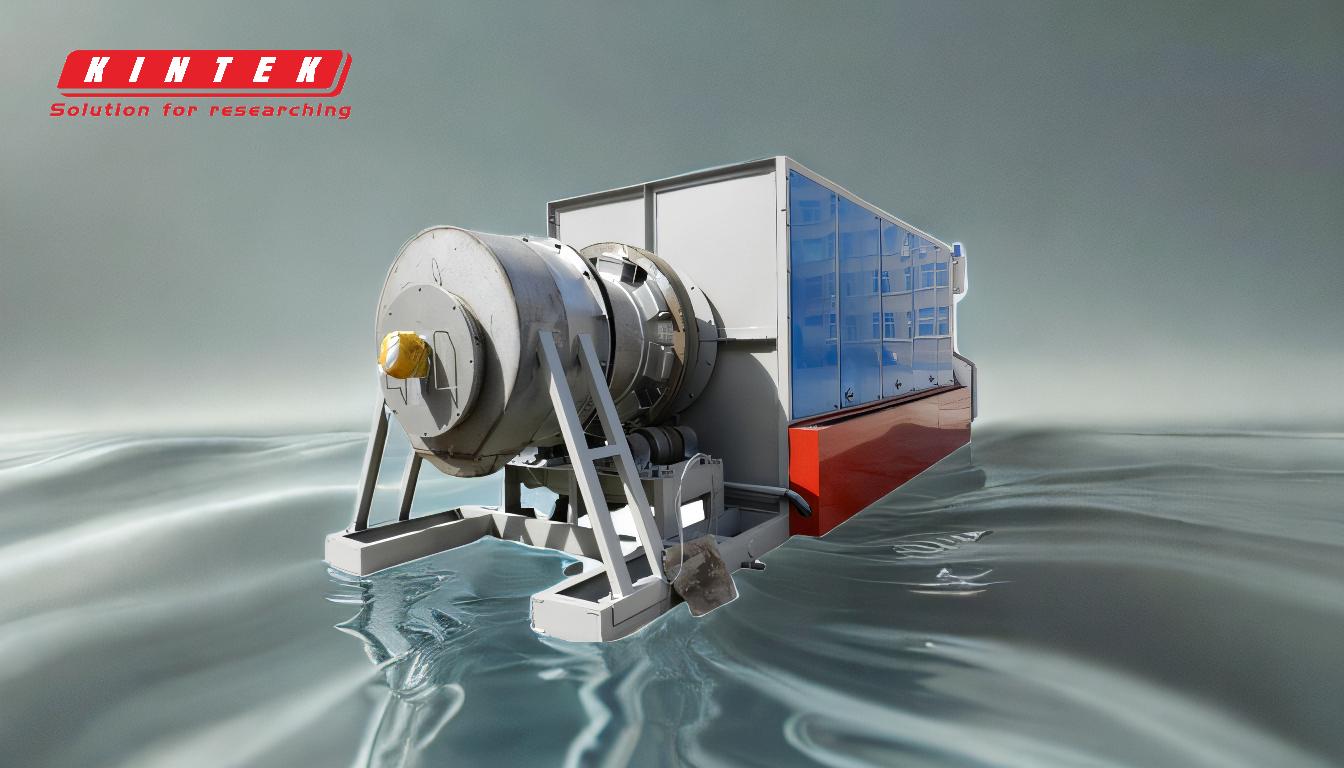
-
Regeneration Temperature:
- The regeneration process for activated carbon involves heating the material to approximately 1000°F (538°C). This high temperature is necessary to volatilize the majority of the adsorbed contaminants, which typically range between 75–90% of the total adsorbed materials. At this temperature, the organic compounds adsorbed on the carbon surface decompose or evaporate, preparing the carbon for further treatment.
-
Role of Steam in Regeneration:
- After heating, steam is injected into the system. The steam serves two primary purposes:
- It helps remove the remaining volatiles that were not fully eliminated during the heating phase.
- It reactivates the carbon by opening up its pores and restoring its adsorption capacity. This step ensures that the carbon is nearly fully restored to its original state, ready for reuse.
- After heating, steam is injected into the system. The steam serves two primary purposes:
-
Efficiency of the Process:
- The combination of high-temperature heating and steam treatment results in a near-complete restoration of the activated carbon. This makes the regeneration process highly efficient and cost-effective, as it allows the carbon to be reused multiple times without significant loss of performance.
-
Sustainability and Cost-Effectiveness:
- Regenerating activated carbon is a sustainable practice that reduces waste and minimizes the need for frequent replacement of fresh carbon. This not only lowers operational costs but also aligns with environmental goals by reducing the carbon footprint associated with manufacturing and disposing of activated carbon.
-
Applications of Regenerated Carbon:
- Regenerated activated carbon can be reused in a variety of applications, including:
- Water purification
- Air filtration
- Industrial gas treatment
- Chemical recovery processes
- Its restored adsorption capacity ensures it performs effectively in these roles, making it a versatile and valuable material in multiple industries.
- Regenerated activated carbon can be reused in a variety of applications, including:
By following this structured regeneration process, activated carbon can be efficiently recycled, providing both economic and environmental benefits.
Summary Table:
Key Aspect | Details |
---|---|
Regeneration Temperature | 1000°F (538°C) to volatilize 75–90% of contaminants |
Role of Steam | Removes remaining volatiles and reactivates carbon pores |
Efficiency | Near-complete restoration, enabling multiple reuse cycles |
Sustainability | Reduces waste, lowers costs, and minimizes environmental impact |
Applications | Water purification, air filtration, industrial gas treatment, and more |
Discover how activated carbon regeneration can benefit your operations—contact our experts today!