The temperature of a CVD (Chemical Vapor Deposition) chamber varies significantly depending on the specific type of CVD process being used. Traditional CVD processes typically operate at high temperatures, often exceeding 1000°C, to facilitate the deposition of materials. However, modified processes like Plasma-Enhanced CVD (PECVD) and proprietary low-temperature CVD methods operate at much lower temperatures, ranging from 200°C to 500°C, to accommodate temperature-sensitive substrates. The choice of temperature depends on the desired deposition rate, material properties, and substrate compatibility.
Key Points Explained:
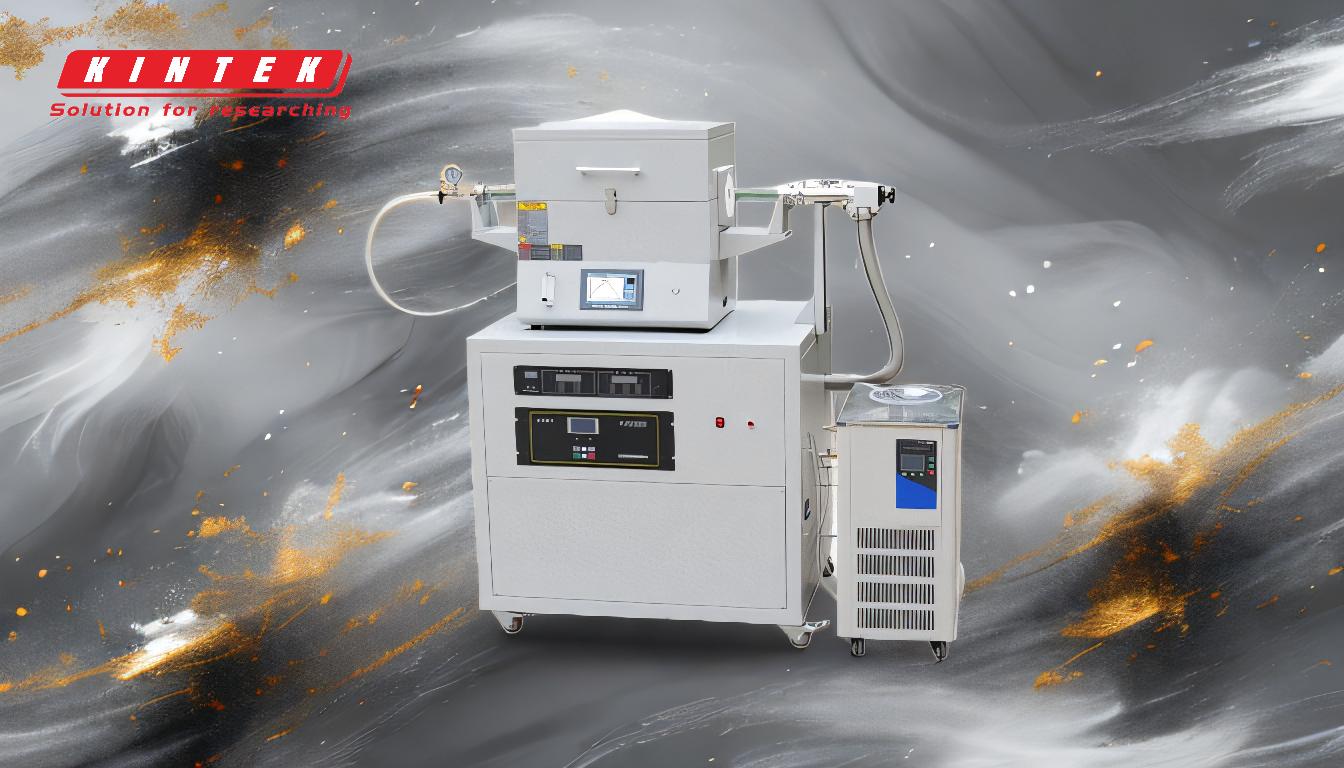
-
Traditional CVD Processes:
- Temperature Range: Traditional CVD processes typically operate at high temperatures, often between 900°C and 1400°C. This high temperature is necessary to achieve the required deposition rates and to ensure the proper chemical reactions occur for material deposition.
- Substrate Compatibility: High temperatures can limit the types of materials that can be used as substrates, as some materials may degrade or lose their mechanical properties at these elevated temperatures.
- Pressure Conditions: These processes often operate at low pressures, typically between a few Torr to atmospheric pressure, to reduce scattering and promote film uniformity.
-
Plasma-Enhanced CVD (PECVD):
- Temperature Range: PECVD systems operate at significantly lower temperatures, typically between 200°C and 500°C. This lower temperature range makes PECVD suitable for depositing films on temperature-sensitive substrates, such as polymers or certain metals.
- Pressure Conditions: PECVD systems usually operate at low pressures, generally in the range of 0.1-10 Torr, which helps in reducing scattering and promoting film uniformity.
- Advantages: The lower operating temperatures minimize substrate damage and allow for the deposition of a wide range of materials that would otherwise be incompatible with traditional high-temperature CVD processes.
-
Low-Pressure CVD (LPCVD):
- Temperature Range: LPCVD systems typically operate at temperatures between 600°C and 850°C. This temperature range is lower than traditional CVD but still higher than PECVD.
- Pressure Conditions: LPCVD systems operate at pressures between one-quarter and two Torr, maintained by vacuum pumps and pressure control systems.
- Applications: LPCVD is often used for depositing high-quality, uniform films, particularly in semiconductor manufacturing.
-
Proprietary Low-Temperature CVD:
- Temperature Range: Some proprietary CVD processes, such as those developed by IBC, operate at even lower temperatures, remaining under 450°C. This allows for the deposition of materials on substrates that would otherwise be damaged or altered at higher temperatures.
- Advantages: These low-temperature processes enable the use of a broader range of substrate materials, including those that are temperature-sensitive, without compromising their mechanical properties.
-
Other CVD Variants:
- Atmospheric Pressure CVD (APCVD): Operates at atmospheric pressure and typically requires high temperatures, similar to traditional CVD.
- Ultrahigh Vacuum CVD: Operates at very low pressures and may require high temperatures, depending on the specific materials and deposition requirements.
- Hot Wall and Cold Wall CVD: These methods differ in their heating mechanisms, with hot wall CVD heating the entire chamber, while cold wall CVD heats only the substrate. Both can operate at a range of temperatures depending on the specific process requirements.
In summary, the temperature of a CVD chamber is highly dependent on the specific CVD process being employed. Traditional CVD processes require high temperatures, often exceeding 1000°C, while modified processes like PECVD and proprietary low-temperature CVD methods operate at much lower temperatures, making them suitable for a wider range of materials and applications.
Summary Table:
CVD Process | Temperature Range | Pressure Conditions | Key Applications |
---|---|---|---|
Traditional CVD | 900°C - 1400°C | Few Torr to atmospheric | High-temp material deposition |
Plasma-Enhanced CVD (PECVD) | 200°C - 500°C | 0.1-10 Torr | Temperature-sensitive substrates |
Low-Pressure CVD (LPCVD) | 600°C - 850°C | 0.25-2 Torr | Semiconductor manufacturing |
Proprietary Low-Temp CVD | Under 450°C | Varies | Broad substrate compatibility |
Atmospheric Pressure CVD | High (similar to CVD) | Atmospheric | General-purpose deposition |
Ultrahigh Vacuum CVD | High (varies) | Very low pressures | Specialized material deposition |
Hot Wall/Cold Wall CVD | Varies | Varies | Customized heating for specific needs |
Need help selecting the right CVD process for your application? Contact our experts today for personalized guidance!