The temperature of a furnace tube depends on the type of furnace, its purpose, and the materials being processed. Furnace tubes can experience extreme temperatures, especially in high-pressure environments where hot spots, coking, and flame impingement can lead to tube ruptures. Continuous furnaces operate at consistent temperatures tailored to specific heat treatment processes like annealing or hardening. For muffle furnaces, the recommended operating temperature is 50°C below the maximum to ensure longevity. Environmental factors such as humidity and corrosive gases also play a role in determining safe operating temperatures. Understanding these factors is critical for maintaining furnace efficiency and safety.
Key Points Explained:
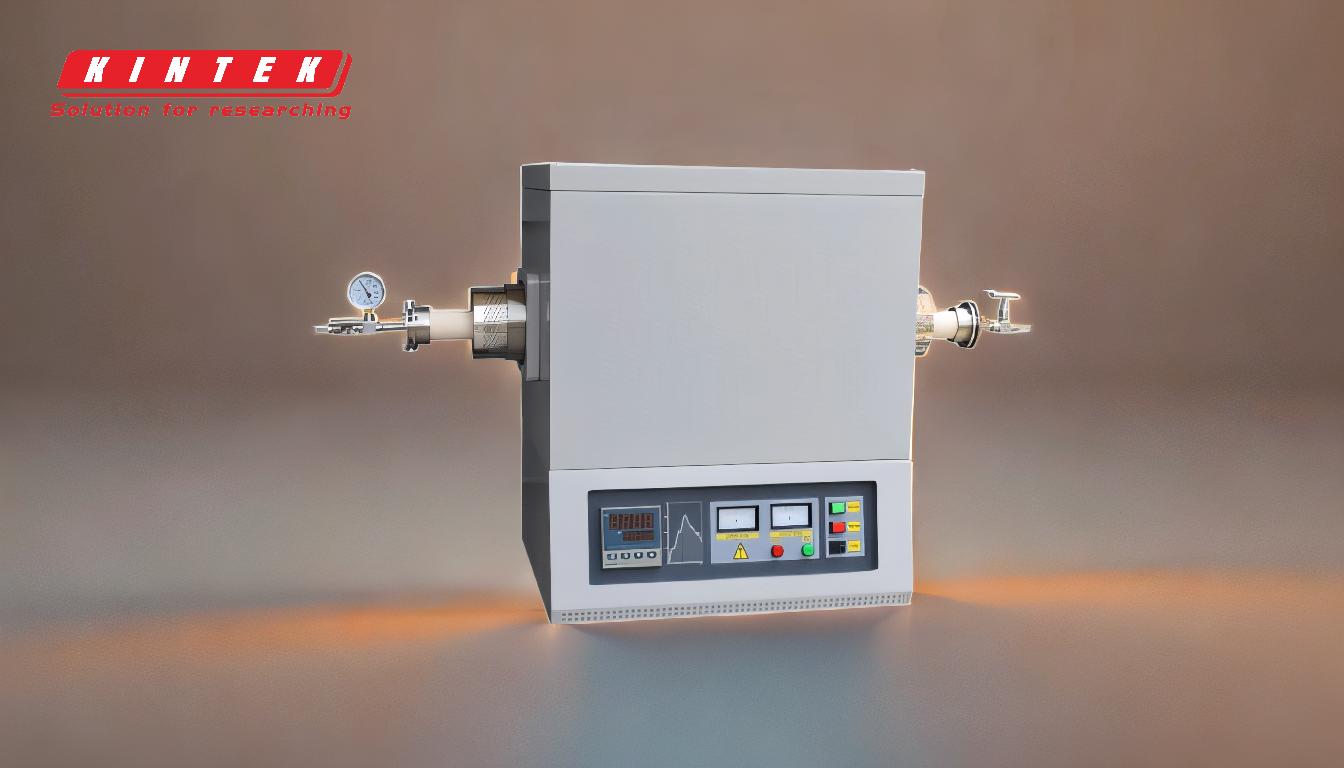
-
High-Pressure Furnace Tubes and Temperature Risks:
- Furnace tubes in high-pressure environments (above 1,500 psig) are prone to extreme temperatures.
- Hot spots can develop due to coking inside the tube and flame impingement on the outside, leading to tube ruptures and potential explosions.
- These risks highlight the importance of monitoring and controlling furnace tube temperatures to prevent catastrophic failures.
-
Continuous Furnaces and Consistent Temperatures:
- Continuous furnaces are designed to operate at stable, permanent temperatures.
- These furnaces are specialized for specific processes like annealing, hardening, normalizing, or carburizing.
- The consistent temperature is tailored to the grade of steel and the heat treatment cycle being applied, ensuring uniform results.
-
Muffle Furnace Temperature Guidelines:
- Muffle furnaces should operate at 50°C below their maximum rated temperature to prolong the lifespan of the heating elements.
- Operating within this range minimizes wear and tear on the furnace wire and reduces the risk of overheating.
- This guideline is particularly important for maintaining the furnace's efficiency and safety over time.
-
Environmental Factors Affecting Furnace Temperature:
- Furnaces should be used in environments with relative humidity not exceeding 85% to prevent damage to components.
- Exposure to conductive dust, explosive gases, or corrosive gases can compromise furnace performance and safety.
- When heating materials that release volatile gases, such as greasy metals, sealed containers or proper ventilation should be used to protect the heating elements.
-
Material-Specific Considerations:
- The type of material being heated influences the furnace tube temperature.
- For example, metals with grease require precautions to prevent volatile gases from corroding the heating elements.
- Understanding the properties of the materials being processed is essential for setting appropriate furnace temperatures and ensuring safe operation.
By considering these factors, furnace operators can optimize temperature settings, extend equipment lifespan, and ensure safe and efficient operation.
Summary Table:
Factor | Details |
---|---|
High-Pressure Environments | Extreme temperatures, hot spots, and flame impingement can cause ruptures. |
Continuous Furnaces | Stable temperatures for processes like annealing, hardening, and carburizing. |
Muffle Furnace Guidelines | Operate 50°C below max temperature to extend heating element lifespan. |
Environmental Factors | Humidity <85%, avoid conductive dust, explosive gases, and corrosive gases. |
Material-Specific Concerns | Adjust temperatures for materials like greasy metals to prevent corrosion. |
Optimize your furnace tube temperature for safety and efficiency—contact our experts today!